What is undercut in plastic parts and how to release in tooling molds?
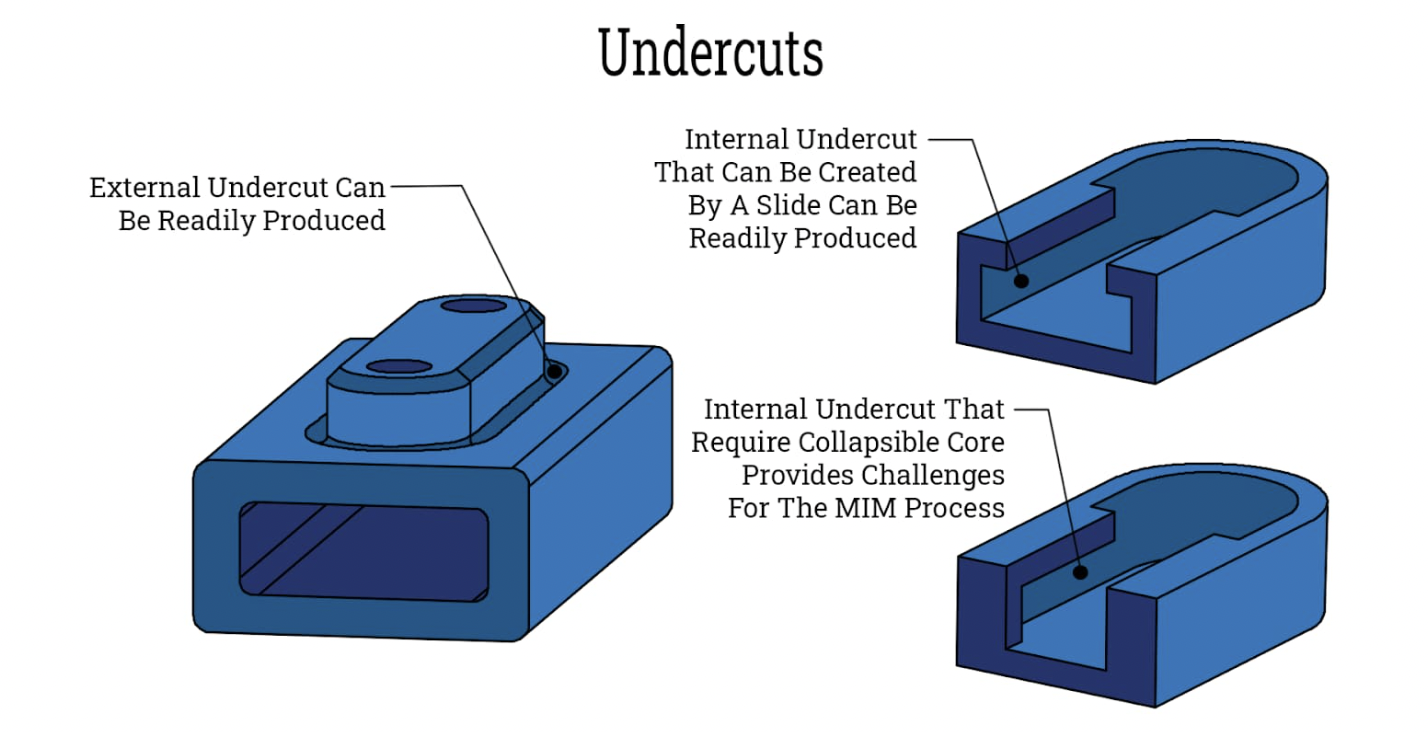
😎 😎 Embarking on the intricate landscape of #injectionmolding, my journey has recently led me to delve into the fascinating realm of undercuts. 👩🏫
📣 As a crucial aspect of plastic part design, #undercuts present both challenges and innovative solutions in the world of tooling molds. Exploring the techniques to address and overcome undercuts not only broadens my understanding of molding processes but also unveils the complexity and precision required to bring a design from concept to reality. 💡 💡
📃 An undercut in injection tooling refers to a feature or area on a molded part that prevents the part from being easily ejected from the mold.
📃 It is a recessed or protruding area that creates a mechanical lock between the molded part and the mold itself.
📌 📌 Undercuts are often used to incorporate complex shapes, details, or additional functionalities in the design of plastic parts. However, they pose a challenge during the ejection process because the mold cannot be pulled straight away from the part.
🤔 🤔 To address undercuts, various mechanisms such as #sliders, #lifters, or collapsible #cores may be employed in the #molddesign.
These mechanisms help release the molded part by allowing certain mold components to move, creating the necessary clearance for the part to be ejected successfully. Managing undercuts is an important aspect of designing injection molds to ensure efficient production and part release. 💪 💪
#undercuts #injectionmold #toolingsolutions
SIDE ACTION
In tooling molds, side actions, also known as side pulls or slide actions, are mechanical features designed to create undercuts or complex features in molded parts. They are needed to mold parts with intricate geometries or features that cannot be accommodated with a simple, straightforward mold design.
The purpose of side actions is to allow the mold to create complex shapes by moving in directions other than the standard mold opening and closing. These additional movements enable the mold to release the part with features such as internal threads, protrusions, or other intricate details that would otherwise be impossible to mold in a single piece.
Side actions are crucial for achieving more sophisticated part designs and enhancing the capabilities of the mold, enabling the production of intricate and detailed plastic or metal components.
Angle lifters
Lately, I've been delving into the intricacies of the undercut system in tooling molds. As I explored the concept of angle lifters, it sparked my curiosity about the distinctions between angle lifters, stripper plates, and strip blocks. I understand this might seem like a basic question, but as a novice in the field, I find myself eager to comprehend every aspect. Below are my study notes for your reference. I appreciate your insights and look forward to learning more about the tooling industry. Thank you for your comments!
In tooling and mold design, an "Angle Lifter" refers to a mechanism or component used to create an angled or undercut feature in a molded part. The purpose of an angle lifter is to facilitate the ejection of a molded part with features that would otherwise make it difficult to release from the mold.
Here's how it generally works:
Undercut or Angled Feature: When a molded part has features such as undercuts, protrusions, or complex geometries that prevent straightforward ejection, an angle lifter is employed.
Lifting Action: The angle lifter is a movable component within the mold that can be lifted or angled after the initial mold opening. This action helps to free the molded part from any undercut features in the mold.
Ejection Facilitation: By using an angle lifter, the mold can create parts with more intricate designs that might include features not parallel to the mold's parting line. The lifter ensures that these features do not hinder the ejection process.
Complex Molded Parts: Angle lifters are especially useful when dealing with complex parts in applications such as automotive, electronics, or consumer goods, where intricate shapes and undercuts are common.
The angle lifter adds a dynamic element to the mold design, allowing for increased flexibility in creating molded parts with more sophisticated geometries. This is crucial for industries where design complexity and part functionality are key considerations.
In tooling and mold design, "lifter" and "stripper" are two distinct components that serve different purposes, especially when dealing with complex molded parts. Here's a brief explanation of each:
Lifter:
Purpose: A lifter is a movable component designed to create undercuts or features in a molded part that would otherwise prevent easy ejection from the mold.
Function: After the initial mold opening, the lifter moves or lifts, creating additional space for the molded part to be released without interference from undercuts.
Application: Lifters are commonly used in molds where the part geometry includes features that are not parallel to the mold's parting line.
Stripper:
Purpose: A stripper, also known as a stripping plate, is a component used to push or strip the molded part off the core pins or other mold features during the ejection phase.
Function: The stripper plate is typically actuated after the mold has opened to a certain extent. It moves into the mold cavity, pushing the part off any protruding features and facilitating its complete ejection.
Application: Strippers are beneficial when dealing with parts that have deep-drawn or threaded features, helping to prevent any interference during ejection.
Key Differences:
Function: Lifters create space for ejection by moving or lifting to accommodate undercuts, while strippers push or strip the part off mold features during ejection.
Movement: Lifters move in a lifting or sliding motion to create space, while strippers move into the mold cavity to push the part off.
Interference: Lifters address undercuts, while strippers handle features that might interfere with the ejection process.
Both lifters and strippers are valuable components in mold design, offering solutions for molds with complex part geometries. The choice between them depends on the specific features of the molded part and the requirements of the molding process.