Compression Molding
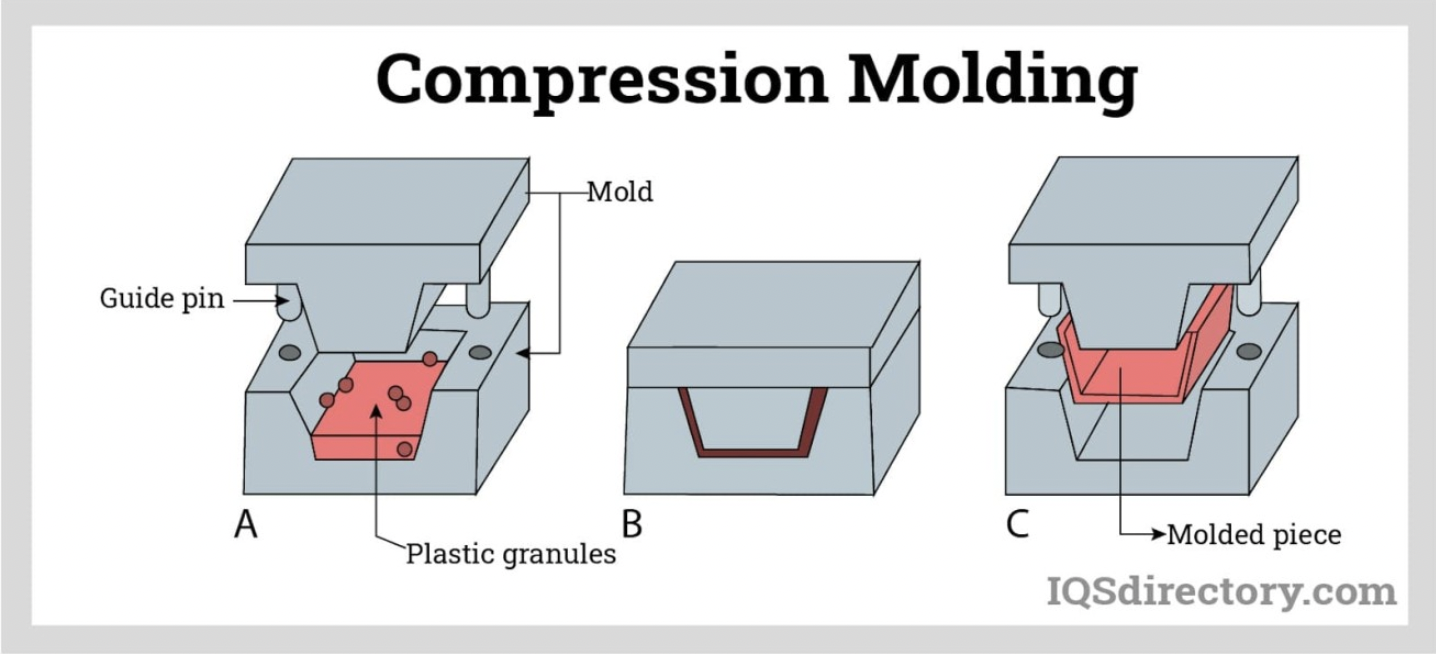
This artical credited by Industrial Quick Search
Introduction
This article will take an in-depth look at compression molding.
The article will give a better understanding of the following topics:
This article will take an in-depth look at compression molding.
The article will give a better understanding of the following topics:
- What is compression molding
- The process of compression molding
- Types of compression molds
- Technology/innovation in compression molding
- Compression molding in comparison to other molding processes
- Applications of compression molding
- Materials used in compression molding
- Advantages of compression molding
- Standards used in compression molding
- And much more…
What is Compression Molding?
Compression molding is a molding process that uses compressive force to squeeze a charge to conform to the shape of a mold that consists of a lower and upper half. Parts may consist of several components that work as one mechanism when compression is applied . When the halves of the mold meet, a cavity is left between them that defines the desired shape. Parts meet at the widest cross-section of the shape to facilitate the ejection of the product once it is cured.
Of the various types of molding, compression molding was the technique developed for synthetic material. It is the least expensive molding method for thermosetting materials. For thermoplastics, injection molding is a better process.
The four types of compression molds are flash, positive, landed positive, and semi-positive mold with flash type being the most used. The types of compression molding are bulk and sheet with bulk molding using a mixture of fillers, catalysts, stabilizers, pigments, and fiber reinforcers. Regardless of the process, the benefits of compression molding of thermoset plastics are exceptional strength, lightweight products, and resistance to corrosion.
The Process of Compression Molding
Compression molding is a permanent molding process that is practical and commercially viable.
The molds for compression molding can be reused for multiple production cycles, which is unlike expendable molding processes that disposed of or recycled after each cycle.
The key steps involved in the compression molding process are detailed below.
Mold Preheating or Preparation
Primarily, the mold needs to be prepared. The typical preparation steps include:
- Cleaning the mold
- Applying release agent
- Heating – this process is done to induce/increase the viscosity of the charge when it is eventually loaded
Charge Preparation
Compression molding is performed on a wide range of materials. As a result, they come in many shapes, sizes, compositions, conditions, and packages.
Preparation changes the material from the state it is delivered into one more ideal for compressing. The charge preparation includes any of the following:
- Unpacking
- Cleaning
- Cutting
- Sizing and weighing
- Heating
Charge preparation is often the most manually demanding part of the compression molding process. This is because it is generally the least automated.
Charge Loading
This involves placing the charge on the lower part of the mold. This way, to ensure the best compression result. Then, the charge is spread on the mold as desired, depending on the shape of the mold, intended thickness, and other factors.
Compression
Relative motion between the two parts of the mold is induced to bring those parts as close as would be desired. As the parts get closer, they compress the charge along the way. Compression is done to achieve any of the following:
- Force the charge to fill the entirety of the intended volume in the cavity left by the mold
- Ensure the desired density of the product
- Facilitate curing
There are three parameters of importance during compression:
- Temperature – This induces or reduces viscosity. Lower viscosity improves the flow and consistency of the charge. In contrast to deformation:Flow leaves no residual stresses.The charge can be heated during preparation and then pressed in a cold mold.The charge may be loaded in the mold cold and heated during compression. This is common with pelletized chargesSome materials do not require heat at any stage.
- Pressure – This should be higher for a more dense charge to achieve a comparable effect. Carbon fiber reinforced polymers typically require between 2 - 14 MPa depending on the necessary fiber density. Higher densities need higher pressure.
- Time – The charge may be compressed gradually, sometimes withholding time (a period during which the charge remains compressed and heated). The compressive force may also be applied and removed very rapidly, without necessarily being a sudden blow, as is the case in forging.
Curing
This part of the molding process facilitates the hardening/setting of the compressed charge into the final product. It may simply involve lowering the temperature or using hardening agents and catalysts to enable setting and hardening.
Some of the cure types are:
- Condensation type. This type of cure uses a tin catalyst.
- Addition type. This one uses a platinum catalyst.
Dimethyl stannane and Tetraethoxysilane-based curing agents are used on various materials like resins, polyurethane, silicon, etc. These are condensation-type cures.
Chemicals like organopolysiloxane are used as additional cures for curing a range of silicones.
Other agents include Benzoyl peroxide, Peroctoate, and t-butyl perbenzoate.
Cooling
Cooling has numerous purposes that include the following:
- Ensuring the mold has the ideal temperature for subsequent molding cycles.
- Ensuring the mold develops the desired mechanical (and thermal) properties for the subsequent removal and storage/shipment/usage.
Ejection
Ejection refers to the release of the product after curing. It can be manual or automated. Manual ejection is more common in recreational and small-scale molding applications like medical accessories manufacture. Automated ejection typically uses a plunger that telescopes from the underside of the mold when ejection is due or uses a separate mechanism of suckers.
Ejection often comes with a release agent, and some coating applied to the mold to prevent the product from sticking to the mold and ease ejection. Application of the release agent is also known as mold curing (not to be confused with the previously discussed curing). The ejection phase of the process significantly influences (and limits) the geometry of the compression molded products. Products with threads, holes, and grooves can be compression molded, albeit the extra features make the ejection less straightforward and more challenging to automate.
The following substances are examples of release agents:
- PVA (polyvinyl alcohol)
- PTFE (poly tetra fluoro ethylene)
- Polysiloxanes
De-flashing
The charge is often loaded in excess (however slight the excess) to the product volume required. This excess will be “flashed out” of (expelled from) the mold cavity at the mold partition line(s) as the charge is compressed. After ejection, this flash remains attached to the product and should be removed in the next part of the process – de-flashing.
De-flashing can be a manual or an automated process. The flash can be cut off with a blade. Manual de-flashing is typically done where the molded product is exceptionally large and cannot be handled by automated deflashing machines. Other reasons for manual de-flashing are financially motivated. Automated de-flashing typically uses water jets and ice blasting. It is typical to have the blasting done under cryogenic conditions. Another alternative for automated de-flashing is vibration tumbling. The flash can be vertical or horizontal depending on how the two parts of the mold meet, which defines the parting line's geometry.
Types of Compression Molds
Some of the types of compression molds are discussed below:
Open Flash type
In the flash type of compression molding, the charge is loaded in excess, such that flash is generated at the end of the compression. As a result, the mold parts do not meet – they leave a small space through which flash is expelled. As a result, this type of molding generates significant waste. However, it is less prone to blistering.
Positive type
This type requires an accurately measured charge. It does not leave space between parts on the mold's parting line. It has the following features:
- It controls part density better.
- It might trap air spaces and cause blistering on the product surface.
- It has the least wastage and is the most convenient when the charge is made up of expensive materials.
Semi-Positive type
This is in between the other two methods of controlling flash and is the most expensive of the three. However, it combines the advantages of the two different mold types.
Charge measurement does not need to be as accurate as with positive type molds. However, there can be an excess that may be allowed to escape during compression.
Technology/Innovation in Compression Molding
Like the rest of industrial technology, compression molding continues to develop and evolve, particularly in the aspects of automation and environmental sustainability.
There are different technologies used in the following aspects of compression molding:
Press
In most applications, hydraulic systems are used for pressing. However, lighter presses may use pneumatic systems.
The pressing motion is almost always vertical. This aids in simplifying the design of the pressing mechanism and its support structure – also considering that the weight of the mold can be large. Technically, the pressing mechanism is capable of being designed in any orientation. However, bringing the mold parts together (hence applying the compression) is usually achieved through telescoping.
Molds
Compression molding uses non-expendable, non-pliable molds. Commercially, molds are made from steel. They are machined from blocks rather than casting into shape because they are not often mass-produced enough to justify the latter.
The machining can be manual (milling, drilling, etc.) or automated (CNC). The primary material for making molds is steel, and the machining is usually subtractive rather than additive.
Scaling
Compression molding is a scalable technique used in an array of applications. These applications include:
Laboratory
Bench-top compressors are used in experimentation (e.g., improving molding methods and developing new molding materials). Such a scale is also often done in prototyping, in which space it competes with 3D printing.
Molding at such a scale also accommodates recreational molding. Furthermore, with the relatively straightforward underlying principle, it is feasible to put the necessary components together and make demonstrations.
Small scale molding
This may be done as part of the back-office activities that are not part of the core business of an enterprise. An example would be a firm that services irrigation equipment as a third party, then opts to mold some of the components on its own.
Medium-scale molding
This is often done by enterprises whose main activity is selling compression-molded products (or those with compression-molded components). However, economic factors may constrain the scale of production.
Large scale molding
This involves mass production of molded products and the production of large-sized products. This scale fully justifies the requirement of automation.
Wet Compression Molding
This involves the fusion of fabrics with a liquid (or molten) charge, such as epoxies. Which results in durable products, and technology is increasingly being applied in the automotive industry.
Vacuum Compression Molding
This technology rapidly depressurizes the mold cavity during pressing. Doing so improves the surface finish of the products.
Transfer Molding
Technologically, this is an extension of compression molding. The charge is held in the transfer port. First, the two parts of the mold are brought together, and then the charge is transferred into the mold cavity. Its main difference with compression molding is the presence of the transfer port in transfer molding and the fact that for compression molding, the charge is placed in the mold cavity before the mold parts are brought together.
Transfer molding is usually used for too intricate products for compression molding.
Injection Compression Molding
This is like transfer molding. The difference is that the charge is injected into a partly open mold. It is partially open because the mold parts would not have fully met, implying that the volume of the cavity during injection will be larger than the final volume after compression.
When the injection is complete, the mold parts come together to meet fully, compressing the injected charge throughout the process. The process is faster than compression molding but uses more expensive equipment.
Insert Molding
In this process, a charge is compressed onto a prefabricated component. Then, the charge encapsulates or is attached to the prefabricated component. The said component is the insert. It is prepared separately before being brought for encapsulation/attachment.
The insert can be a knife blade, and the result of the insert molding process can be the attachment of a plastic handle. Other standard inserts are threads (alternatively called nutsets) and electrical contacts.
Insert molding is an alternative means of assembling components, especially those that do not need to be disassembled once they begin their service life. Insert molding has the following advantages:
- It provides the designer with more flexibility
- It is fast, more so on products that have more than one insert that can be compressed all at once
It also has the following disadvantages:
- It requires more intricately designed molds.
- It also raises the risk of residual stresses in the finished product because a combination of materials with different mechanical properties may be subjected to temperature gradients.
Overmolding
Overmolding involves the molding of material onto a pre molded component. It is usually done on materials with different mechanical properties to combine their advantages.
Examples would be a power tool handle and a toothbrush. To produce the handle, an elastomer can be over-molded onto a PTFE substrate (the PFTE substrate molded in some previous stage). The PTFE would provide rigidity for the handle, and the elastomer would improve the handle's grip, ergonomics, and aesthetics.
Though both methods may be technically feasible, the over-molding is more often injection molded than compression-molded. This is because the substrate onto which the overmolding is done is more likely to have been compression molded.
Overmolding has a variant, i.e., two-shot molding. This is entirely done using injection molding.
Compression Molding in Comparison to Other Molding Processes
Compression molding is acknowledged as one of the more conventional techniques to be developed, with several more coming afterward. Below are some of the other molding techniques:
Extrusion Molding
Extrusion molding is ideal for products with a uniform cross-section or for long products where a mold with the full dimensions of the final product would be inconvenient to make. Even if the dimensions are small, it is faster to produce products with a uniform cross-section using extrusion molding (then subsequently cutting the extruded product to size) than other molding methods like injection molding.
Blow Molding
Blow molding is used for hollow objects, often with an opening smaller than the cavity of the product. Bottles are the most blow molded product. A preform is placed at the beginning of the mold. The mold is closed and heated, and then the preform is blown – filling the mold and taking its shape in the process.
Injection Molding
In injection molding, the material is pushed into a mold. The mold is fully closed before the material is injected. The viscosity of the material should be low enough to facilitate its flow into the intended mold – under the desired pressure. Thus, the charge is continuously heated. Preforms for blow molding are often injection molded. Technically, all thermoplastic products that can be compression molded can also be injection molded. The charge preparation is much more straightforward as they simply use plastic pellets. Injection-molded components suffer the same geometrical limitations as do compression-molded ones. Most thermoplastic products are made more economically using injection molding than compressin molding.
Thermoforming
Thermoforming is used for manufacturing very thin products, like fast food packaging material. First, the material is spread over the mold and heated. A vacuum then sucks the material onto the mold.
Rotational Molding
This method is used to manufacture large hollow objects, where blowing would face technical or otherwise limitations.
3D Printing
Technically, 3D printing has a different underlying principle from molding. However, it competes with molding techniques in the application of prototyping. Molding techniques are more suited to mass production, and 3D printing is more suited to variety.
Casting
Casting involves pouring liquid material into molds under gravity. This process cannot be done at scale for plastic products. It is the only method mentioned hereunder that can use pliable and temporary molds.
Leading Rubber Compression Molders and Molding
- RD Rubber Technology Corporation
- Britech Industries
- Pierce-Roberts Rubber Co.
- Accurate Products, Inc.
- REDCO Rubber Engineering amp; Development Company
- Mason Rubber Co., Inc.
- Minnesota Rubber amp; Plastics
- Kent Rubber Supply Co.
- Device Technologies, Inc.
- Dynatect Ro-Lab, Inc.
- Jet Rubber Company
Applications of Compression Molding
Most of the compression-molded products are thermosets. Rubber, thermoplastics, and polymer composites are also trendy. The presence and scale of compression molding in various areas are dictated by demand.
Compression molding is practical on products that are generally flat (or solid and flat-surfaced), such as the following:
- Kitchenware, e.g., plastic utensils and utensil handles and knobs
- An array of handles, e.g., mirrors, pots, etc.
- Rubber clothing
- Automotive parts, e.g., fenders, casings for engine components, etc.
- Flatware
- Computer and gaming equipment, e.g., keyboards, mouse, and joystick covers.
- Appliance housing, e.g., for irons, kettles, plugs, etc.
- Casings for electrical equipment etc.
- Gaskets
- Biomass (pelletizing) – biomass can be compressed for storage and handling and later used for fuels, amongst other uses.
- Medical accessories, e.g., syringe stoppers and other plastic and silicone components.
Materials Used in Compression Molding
There are several materials used in compression molding. Some of the examples include the following:
Thermosets
Thermosets are plastic materials that can only be liquefied once. Once they are hardened, these cannot be liquefied again. Thus it can neither be remolded nor recycled (the hardening involves an irreversible chemical reaction – polymerization and cross-linking). In addition, once they set, they would instead smolder and char rather than melt when heated enough.
This incapacity to be recycled comes as the most significant disadvantage of thermosets. They are particularly challenging to dispose of sustainably. However, they do have specific properties that make them more convenient for particular applications:
When compared to metals:
- They are lightweight
- They are good insulators
- It cost less to produce
When compared to thermoplastics:
- They have good dimensional stability and heat-resistant qualities.
In molding, thermosets are often combined with other materials, mainly carbon fibers, to make composites.
Some of the thermosets used in molding are listed below:
- Phenolic molding compound
This is so-called because of the chemical structure of its monomer, which contains a phenyl group. It is commonly called Bakelite. It has good heat-resisting qualities and dimensional stability.
- Epoxy resin
This is an array of substances because of the epoxide group found in their chemical structure. Mechanically, they perform almost like phenolic molding compounds.
- Polyester
Polyester can be found both as a thermoset and as a thermoplastic.
- Polyurethane
This is another thermosetting plastic.
Thermoplastics
Thermoplstics can be melted repeatedly. Polyester is one of the few materials to fit in both lists: thermosets and thermoplastics, depending on how it is hardened. Thermoplastics can be disposed of more sustainably. They are relatively low cost. However, their mechanical performance is bettered by thermosets.
Some of the thermoplastics used in molding are listed below:
Polypropylene
Polypropylene foam is produced using compression molding with a chemical blowing agent (foaming agent).
Nylon
This is another example of thermoplastic.
High-density polyethylene
Polyethylene can be mixed with rubber to make a composite that can be molded as an elastomer.
Polyester
Polyester forms a thermoplastic if it is not mixed with a hardening agent
PTFE
A thermoplastic with very high viscosity and good non-stick properties.
High temperature materials
Polyaryletherketones (PAEK) are compression molded to replace metals in certain applications. Polyetheretherketones (PEEK) and polyetherketoneketones (PEKK) also fall into this family of materials.
Glass Fiber
Fibers are added to resins to form composite materials. Composites combine the advantages of their constituent materials and are therefore better than either constituent individually. For example, materials like sheet molding compounds are glass-reinforced composites.
Carbon Fiber
Carbon fibers serve the same purpose as glass fibers but generally give a more rigid composite and cost more.
Sheet Molding Compound (SMC)
Typically, this consists of two layers of polymer resin, e.g., polyester, enveloping a layer of glass fibers. A polythene film covers the compound to facilitate more convenient handling. The film is part of the packaging and is removed before molding. The finished sheets are about 5mm thick. To make products of substantial thickness using SMC, several layers may have to be stacked on top. There is a Thick-walled SMC variant, whose thickness can go up to 50mm.
Bulk Molding Compound (BMC)
BMC is a doughy combination of polymer resins, chopped fibers (those for SMC are left long), and a hardening agent. Loading the BMC onto the mold only involves ensuring the required mass of charge is taken. As a result, BMC tends to be more pliable than SMC.
Elastomers
Chemically, an elastomer is a polymer with viscoelasticity. Their applications arise because of their properties as insulators and their resistance against an array of substances.
The following are some of those used in molding.
Nitrile
This is an acrylonitrile-butadiene rubber. It is an oil-resistant rubber that can be compression molded, injection-molded, transfer molded, over-molded, etc.
Styrene-butadiene rubber
This is a water-resistant rubber and performs well in resisting organic acids. However, it does not perform well with strong acids, ozone, oils, etc.
Ethylene propylene diene monomer rubber
This elastomer has good resistance to ozone and weather elements. Therefore, it finds use in applications like sealing hot water. It also performs well with greases, alcohols, detergents, etc. However, it performs poorly when exposed to petroleum fuels.
Viton (vinylidene fluoride and hexafluoropropylene)
Viton is one of the most expensive and durable elastomers. It performs well in high temperatures or exposure to fuel and water. Viton can be used on O rings, fuel injectors, boat propeller fittings, etc.
Silicone Rubber
These find use in mechanically demanding applications, where the rubber is subjected to significant stretching and temperature variations. They also perform well in very low temperatures. In addition, they find use in aerospace applications and electrostatic discharge protection.
Advantages of Compression Molding
Compression molding has several benefits/advantages. These advantages include:
- Low-cost operation
- Good surface finish
- Faster than some methods
- Flexible design
- High product uniformity
- Good dimensional accuracy
- No residual stress
- Minimizes wastage
- Extra features to consider like boss attachments, insert, etc.
However, some demerits can be associated with compression molding. These include:
- The product's geometry is limited to enable ejection while ensuring the reuse of the mold. For example, the product cannot have undercuts.
- A product with the shape of a bottle cannot be viably produced using compression molding, chiefly because of ejection and mold reuse concerns.
- It gives a high carbon footprint and energy consumption challenges.
- The energy consumption is typically lower than injection molding but higher than the rest of the molding processes.
Overall, the merits/advantages of compression molding outweigh the demerits.
Standards Used in Compression Molding
Some of the standards used in compression molding are listed below:
- ISO 293:2004 Plastics: This details the compression molding of thermoplastic material test specimens.
- ISO 295:2004 Plastics: This details the compression molding of thermosetting test specimens.
- ISO 286 Geometrical product specifications (GPS): This is an ISO code system for tolerances on linear sizes, with Part 1 being the basis of tolerances, deviations, and fits.
- BS EN 289:2014 Plastics and rubber machines: This details the compression molding machine's safety precautions. The transfer molding machine's safety is also considered.
- ISO 2393 Rubber test mixes detail the preparation, mixing, and vulcanization. Equipment and procedures
Conclusion
Compression molding finds itself amidst a rapidly advancing manufacturing industry, to which new techniques are continually introduced. As a result, it has endured some moderate longevity compared with some methods competing in the same space. Its ability to meet the evolving needs of the industry has been aided by its adaptation into emerging trends, for instance, robotics. In the broader context of the manufacturing industry, compression molding is not an end in itself but a means to some other end.