The 8 Common Mechanical Machining Processes
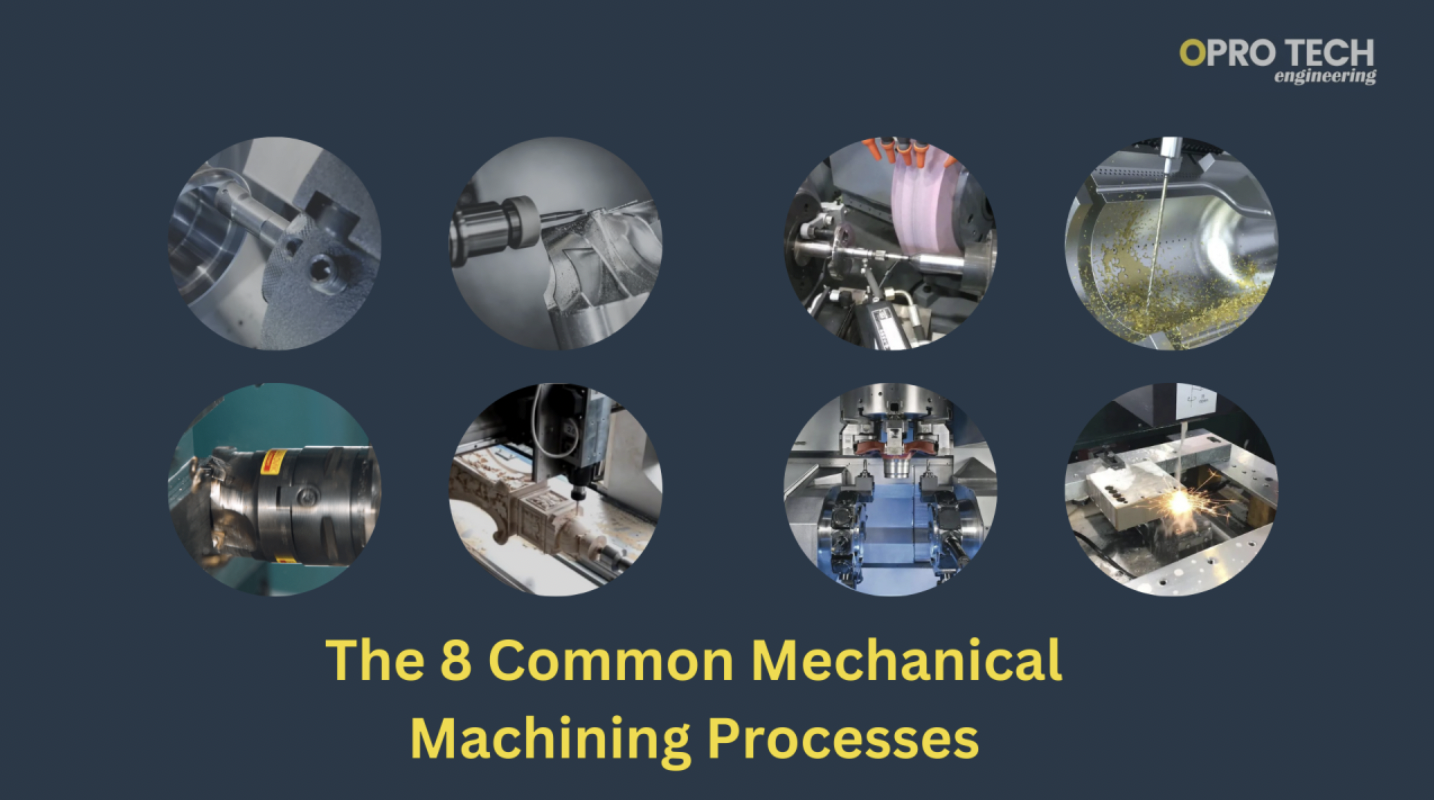
When it comes to manufacturing, mechanical machining processes are indispensable.
Mechanical machining is the process of transforming raw materials into desired shapes, sizes, and surface qualities, covering various precision machining methods to meet the needs of different parts.
The following will detail eight common mechanical machining processes:
- Turning Turning involves fixing the workpiece on a rotating workpiece holding device and then gradually cutting the material on the workpiece using a cutting tool to obtain the desired shape and size. This method is suitable for manufacturing cylindrical parts such as shafts and sleeves. The turning method and tool selection affect the final product's shape and surface roughness.
Turning can be divided into different types, including external turning, internal turning, facing, and threading.
External turning is typically used for machining shapes such as shafts, cylinders, and cones;
in internal turning, the tool enters the workpiece's inner hole to machine the diameter and surface to the required size and accuracy;
facing is commonly used to create flat surfaces, such as the base or end face of parts;
threading is accomplished by gradually cutting the thread shape by moving the cutting edge of the tool relative to the workpiece's surface, including internal and external threading.
- Milling Milling involves rotating a cutting tool on the workpiece surface to cut material, allowing for the manufacture of flat surfaces, contours, gears, and other complex-shaped parts by controlling the tool's movement. Milling includes face milling, end milling, gear milling, profile milling, and other methods, each suitable for different machining requirements.
In face milling, the cutting edge of the tool cuts on the workpiece's surface to obtain a flat surface;
end milling is used to cut along the workpiece's height direction for grooves and holes;
gear milling typically utilizes special tools with cutting edges to cut gear teeth shapes;
profile milling is used for machining complex curves or profile shapes, with the tool path precisely controlled according to the profile.
- Drilling Drilling involves cutting material on the workpiece surface using a rotating drill bit to create holes with the desired diameter and depth, widely used in manufacturing, construction, and maintenance fields. Drilling is commonly categorized into conventional drilling, center drilling, deep hole drilling, multi-axis drilling, etc.
Conventional drilling uses drill bits with spiral cutting edges, generally for smaller holes and general drilling needs;
center drilling creates a small hole on the workpiece surface first before drilling with a larger drill bit to ensure the accurate position of the larger hole;
deep hole drilling is used for deeper holes, requiring special drill bits and cooling techniques to ensure machining accuracy and quality;
multi-axis drilling utilizes multiple drill bits to drill simultaneously at different angles, suitable for situations requiring drilling multiple holes simultaneously.
- Grinding Grinding involves gradually cutting or grinding material on the workpiece surface using an abrasive tool to obtain the desired shape, size, and surface quality. Grinding is commonly used for parts with high precision and surface quality requirements, such as molds, precision mechanical parts, and tools.
Grinding is divided into surface grinding, cylindrical grinding, internal grinding, and profile grinding.
Surface grinding is used for machining flat workpiece surfaces to obtain smooth surfaces and precise dimensions;
cylindrical grinding is used for machining the outer cylindrical surface of cylindrical workpieces, such as shafts, pins, etc.;
internal grinding is used for machining the inner surface of holes, such as internal holes, shaft holes, etc.;
profile grinding is used for machining complex profile shapes, such as the cutting edges of molds and tools.
- Boring Boring is commonly used to machine internal circular holes in workpieces, cutting within existing holes to achieve precise dimensions and flatness goals. Unlike drilling, which cuts material on the workpiece surface to form holes, boring cuts holes by inserting the tool into the workpiece's interior.
Boring is divided into manual boring and CNC boring.
Manual boring is suitable for small-batch production and simple machining tasks;
CNC boring achieves automated high-precision machining by programming cutting paths, feed rates, and rotation speeds.
- Planing Planing involves cutting material on the workpiece surface using a planer to obtain flat surfaces, precise dimensions, and surface quality. Planing is commonly used for machining large workpieces' flat surfaces, such as bases and beds. It provides smooth surfaces for workpieces, making them suitable for use with other components.
Planing is typically divided into roughing and finishing stages.
In the roughing stage, the planer's cutting depth is large to quickly remove material.
In the finishing stage, the cutting depth decreases to achieve higher surface quality and dimensional accuracy.
Planing is classified into manual planing and automatic planing.
Manual planing is used for small-batch production and simple machining tasks;
automatic planing uses automated machine tools to control the planer's movement for a more stable and efficient machining process.
- Broaching Broaching gradually deepens the cut using a broaching tool to create internal complex contours, commonly used for machining workpiece contours, grooves, holes, and other complex shapes. Broaching can achieve higher machining accuracy and surface quality and is suitable for parts requiring high precision and good surface quality. It is generally categorized into surface broaching, profile broaching, groove broaching, hole broaching, etc.
Surface broaching is used for machining flat workpiece surfaces to obtain smooth surfaces and precise dimensions;
profile broaching is used for machining complex profile shapes, such as molds, parts, etc.;
groove broaching is used for machining grooves and slots, with the cutting edge entering the workpiece and cutting along the workpiece's surface;
hole broaching is used for machining the inner contour of holes, with the cutting edge entering the hole and cutting the inner surface of the hole.
- Electrical Discharge Machining (EDM) EDM cuts and machines conductive materials using electrical discharge arcs to obtain high-precision, complex-shaped parts such as molds and tools. It is commonly used in manufacturing molds, plastic injection molds, aerospace engine parts, medical devices, etc. EDM is typically used for hard, brittle, or high-hardness materials that are difficult to cut using traditional machining methods, such as tool steel, hard alloys, titanium alloys, etc.
Main features of EDM:
- Non-contact cutting: Unlike traditional mechanical cutting, EDM is a non-contact machining method. There is no direct physical contact between the tool and the workpiece; instead, material is removed through electric arc discharge.
- High precision: EDM can achieve high-precision machining, usually reaching sub-micron level dimensional accuracy. This makes it suitable for manufacturing molds, models, and other precision parts.
- Complex shapes: Since EDM is a non-contact machining method, it can be used for machining very complex shapes, including internal contours, small holes, grooves, etc.
- Suitable for high hardness materials: EDM is suitable for materials with high hardness because it does not depend on the tool hardness as in traditional cutting methods.
These are the eight common mechanical machining processes, each with its specific applications and advantages.
Choosing the appropriate process depends on the material, shape, size, and surface requirements of the part.
THE OPRO TECH ENGINEERING TEAM INCLUDES DIVERSIFIED AND EXPERIENCED SYSTEM ENGINEERS, WE CAN SUPPORT YOUR PROJECT AT EVERY STAGE OF DEVELOPMENT.
WE HAVE DEMONSTRATED OUR ENGINEERING, ANALYSIS, AND DESIGN CAPABILITIES OVER MANY PROGRAMS FOR THE MEDICAL, HOUSEHOLD, AUTOMOTIVE, AND COMMERCIAL INDUSTRIES.
For more information, please feel free to contact: xiu@opro-tech.com