Why Is It Called Vacuum Casting Rather Than Vacuum Molding?
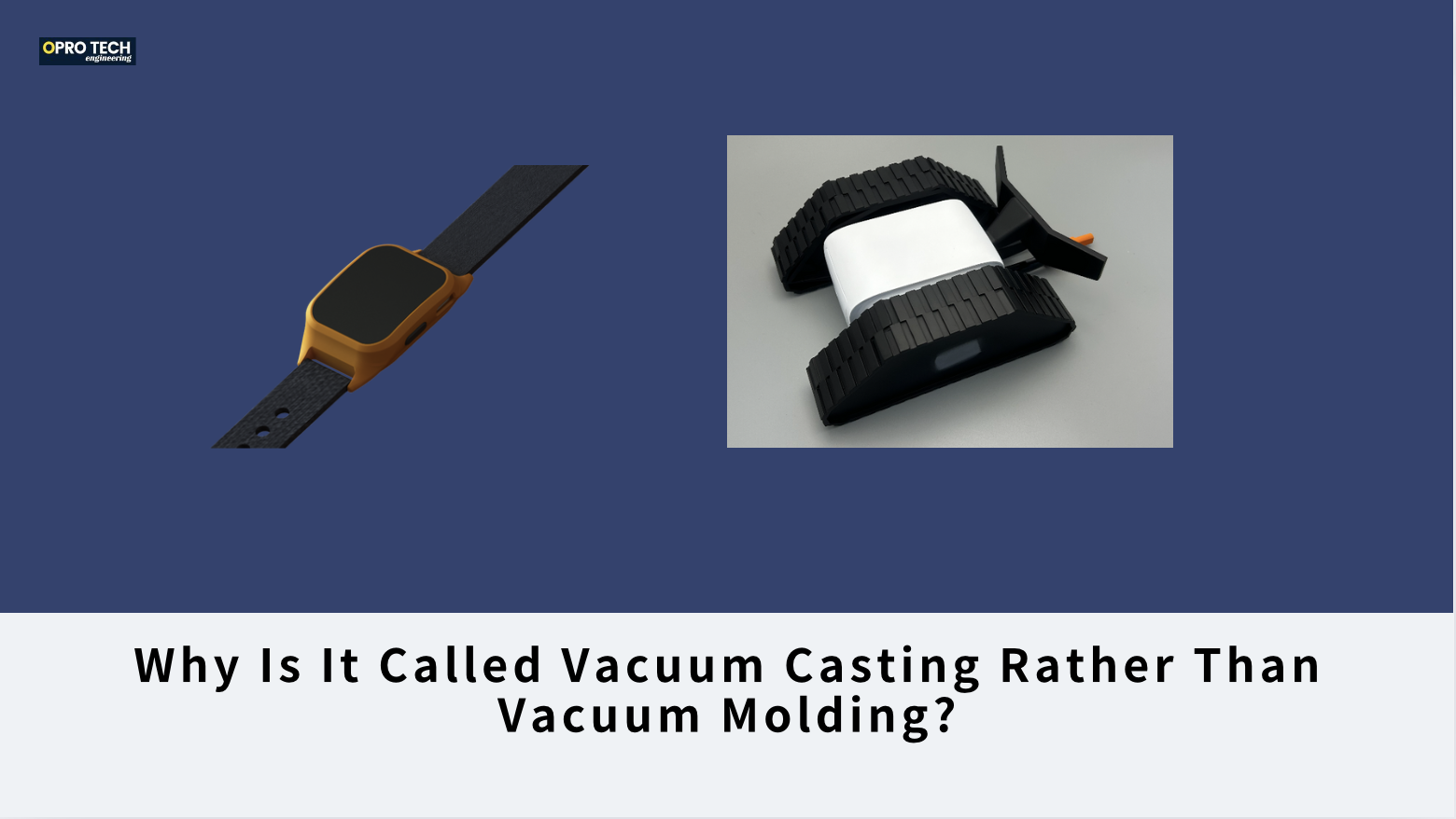
As someone who's been working closely with various manufacturing techniques, I've always been curious about the terminologies we use every day. Recently, I found myself pondering: why is it called vacuum casting and not vacuum molding? After all, both casting and molding involve shaping materials using molds, so what exactly makes vacuum casting different? This question sparked a deeper investigation into the processes, and it made me reflect on the fundamental differences between casting and molding.
Let's start with what I learned.
What is Casting?
Casting, at its core, involves pouring a liquid material—often metal, resin, or urethane—into a mold. The material then solidifies into the shape of the mold as it cools or reacts chemically. The key feature of casting is that the material starts as a liquid and then hardens into the desired shape. Think of metal foundries where molten steel is poured into large molds to create heavy-duty parts.
Casting relies heavily on gravity to allow the liquid material to flow into all the nooks and crannies of the mold, making it perfect for producing large or intricate parts. The process can be used with metals, ceramics, plastics, and even food products!
What is Molding?
On the other hand, molding involves shaping materials that are either semi-solid or molten but generally not in a purely liquid state. Molding typically involves materials like plastics or rubbers. In processes like injection molding or compression molding, the material is injected or pressed into a mold, taking its shape as it cools or hardens.
One of the key differences is that in molding, the material is forced into the mold under pressure, rather than simply poured in. The pressure helps the material fill every detail of the mold.
So, Why Vacuum Casting?
Now, let’s get back to vacuum casting. The term vacuum casting describes a process where a liquid material, such as resin or silicone, is poured into a mold under a vacuum to remove air bubbles and ensure a high-quality finish. The key here is that the material is poured in a liquid state, and the vacuum ensures that no air pockets remain. It’s still a casting process because the material goes through the same steps: pour, solidify, and release from the mold.
While the vacuum ensures precision, the essence of the process remains true to the principles of casting. The vacuum is a technique used to improve the quality of the final part, but it doesn’t change the fact that liquid material is involved and is allowed to harden naturally.
Why Not Vacuum Molding?
If you're like me, you might wonder: “But isn't it still going into a mold? Why not call it vacuum molding?”
Here’s where the distinction lies: Molding, as a term, is reserved for processes where the material is injected or compressed into the mold, often while it's still molten or pliable, not fully liquid. Vacuum casting, on the other hand, works with completely liquid materials that flow into the mold under the force of gravity (with the vacuum ensuring air removal). The focus in casting is on the solidification of a liquid material, whereas molding often deals with shaping soft or pliable materials.
Conclusion
So, after diving into the details, I can confidently say that vacuum casting stays true to the principles of traditional casting. The vacuum element improves the quality, but at its core, it’s about pouring and solidifying a liquid material into a mold. Molding, by contrast, typically involves shaping semi-solid or plastic materials under pressure.
It’s fascinating how a small difference in terminology opens up a deeper understanding of the processes we use every day. Next time you hear "vacuum casting," you’ll know why it’s not called vacuum molding!
Dan
Factory add: No 39, Zhen an west road, Changan town , Dong guan city, China.