Moisture Management in Injection Molding: Why Dew Point Control Matters
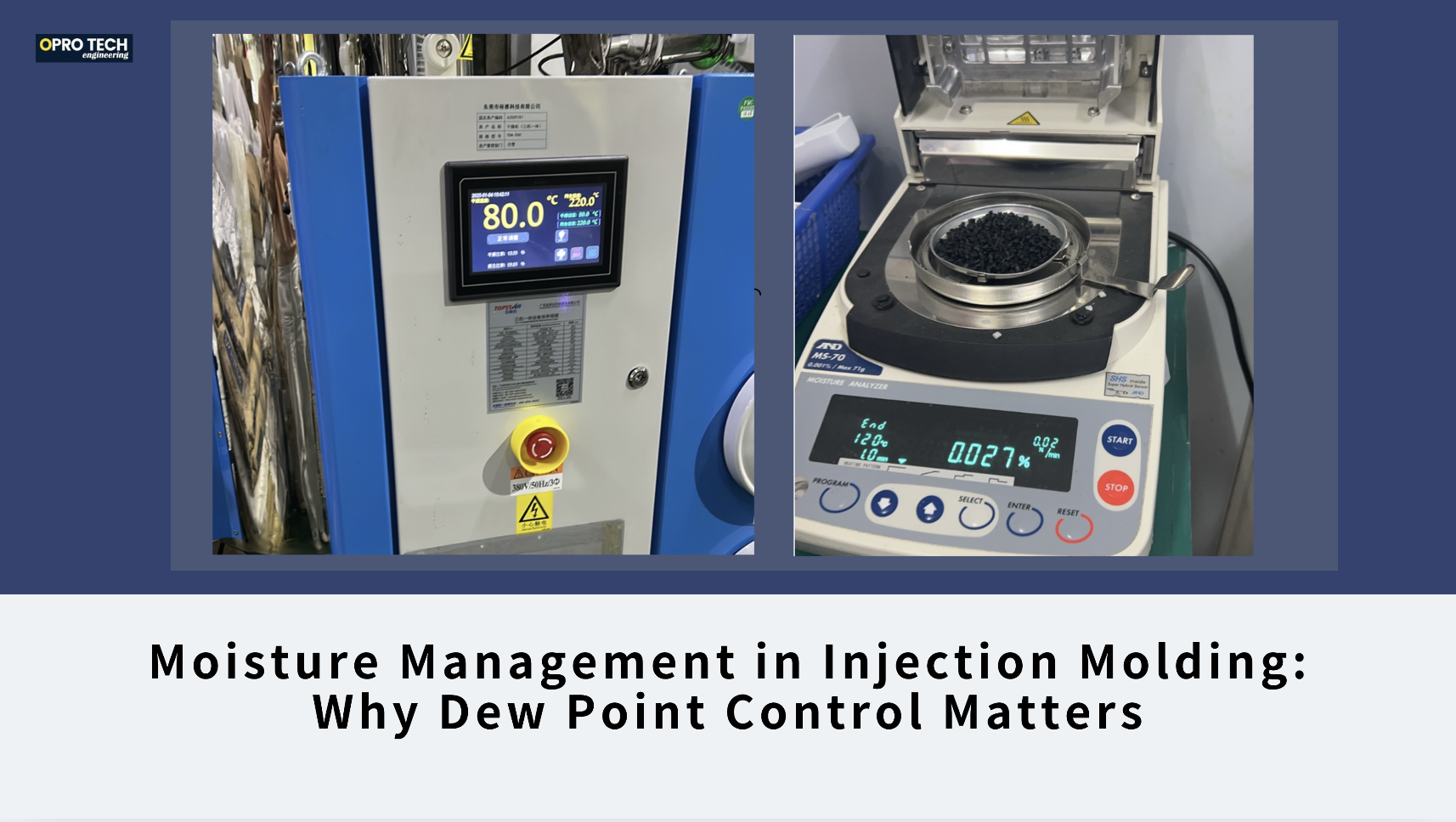
When it comes to plastic injection molding, do you strictly control the moisture content of your materials? How crucial is moisture control in ensuring high-quality, defect-free parts? And more importantly, how can you effectively manage and reduce moisture to prevent issues like bubbling, warping, or poor surface finish?
One of the key ways to maintain the right moisture levels is by using a dehumidifying dryer. But how do you determine the optimal dew point for your material, and why does it matter in the drying process? Let’s dive into the science behind moisture content control and explore how to set up your drying system for success.
Moisture content control is critical in many manufacturing processes, especially in industries like plastics, injection molding, and mold-making. Excess moisture in materials can cause defects, inconsistencies, and reduced quality in the final product.
For example, in injection molding, especially when working with hygroscopic materials like nylon, the material absorbs moisture from the air. When the material is heated during processing, the moisture inside can vaporize, leading to defects like bubbles, surface blemishes, or dimensional changes in the finished part. Controlling the moisture content ensures that the material behaves as expected during molding.
A dehumidifying dryer is a key tool used for this purpose. It dries and controls the humidity of the material before it's processed, ensuring that the moisture content is kept within an optimal range. These dryers work by using desiccant materials or refrigeration methods to absorb or remove moisture from the air or material, which helps maintain consistent quality and reduces waste.
While both dehumidifying dryers and normal heaters serve the purpose of reducing moisture in materials before molding, they operate in different ways, and one is definitely more effective for certain types of materials.
Dehumidifying Dryer:
- Precise Control of Humidity: Dehumidifying dryers are designed to control both the temperature and humidity of the material. They reduce moisture by pulling humidity from the air around the material, which is crucial for materials like nylon, PET, or other hygroscopic plastics that absorb moisture from the environment.
- Consistent Drying: These dryers ensure that the moisture content is brought down to a specific level, often measured by the percentage of water in the material, and this consistency helps prevent defects like bubbles, warping, or poor part finish.
- Energy Efficiency: Though these dryers might seem more expensive, they can be more energy-efficient in the long run, especially for high-volume production, as they can dry large quantities of material more quickly and effectively compared to a traditional heater.
Normal Heater:
- Heating Only: A normal heater will typically just heat the material to a certain temperature but doesn’t directly control humidity. It relies on the assumption that moisture will naturally evaporate as the material heats up.
- Less Control Over Moisture: While heaters can be used for drying, they don’t provide a consistent level of moisture removal. The material may still contain moisture, leading to defects during the molding process, which can result in quality issues that are harder to address.
- Faster Drying, but Less Effective for Certain Materials: Heaters may work fine for some materials that don’t absorb moisture as quickly, but for more hygroscopic materials, they’re not as reliable as a dehumidifying dryer.
Is it Necessary?
It depends on the type of material you're using and the quality you're aiming for. For certain high-quality or complex injection molding processes, like those with hygroscopic materials (e.g., Nylon, PBT), having a dehumidifying dryer is definitely beneficial. It ensures consistency, reduces defects, and maintains production efficiency.
However, for small-scale runs or less sensitive materials, some suppliers may get by without dehumidifying dryers, especially if the moisture content doesn’t significantly affect the quality of the finished parts. In those cases, a normal heater might suffice.
For Smaller Suppliers:
It’s common for smaller injection molding suppliers to skip this equipment if they aren’t working with materials that are prone to moisture issues. For example, with less moisture-sensitive materials (like some types of ABS or polystyrene), they may not see the need for the added cost of a dehumidifying dryer. However, if they’re working with more demanding materials, investing in a dehumidifier may help in the long run to avoid rework and defects.
the dew point of a dehumidifying dryer is an important factor in moisture control. The dew point refers to the temperature at which the moisture in the air starts to condense into liquid water. In dehumidifying dryers, controlling the dew point is critical for ensuring that the air around the material is dry enough to remove moisture effectively.
Typically, dehumidifying dryers are designed to maintain a dew point of around -40°C to -20°C (-40°F to -4°F). A lower dew point indicates that the air in the dryer is very dry, which is crucial for drying materials like nylon or other hygroscopic plastics that easily absorb moisture from the environment.
Here’s why the dew point matters:
- Lower Dew Point = Better moisture removal: A low dew point ensures that the dryer is pulling as much moisture as possible out of the air, which is ideal for materials that are sensitive to humidity.
- Higher Dew Point = Less effective drying: If the dew point is too high, the dryer won't be able to remove enough moisture, and your material might still contain too much water, leading to defects during molding.
The exact dew point you need can vary depending on the type of material you're working with, but in general, a dew point of around -40°C is considered optimal for drying hygroscopic plastics.
Maintaining precise moisture control is essential for producing high-quality molded parts and optimizing the efficiency of your injection molding process.
A dehumidifying dryer with the right dew point setting ensures that your materials are dried consistently and effectively, reducing the risk of defects and improving overall production quality. Whether you’re working with hygroscopic materials or striving to meet the highest standards in manufacturing, understanding and managing moisture content can make all the difference.
By investing in proper moisture control techniques, you’re not just enhancing your production; you’re also safeguarding your product quality, reducing waste, and increasing cost-efficiency in the long run.
Dan
Factory add: No 39, Zhen an west road, Changan town , Dong guan city, China.