Understanding Mold Materials: P20, S50C, 718H, and 1.1730 – A Practical Guide for Manufacturing Professionals
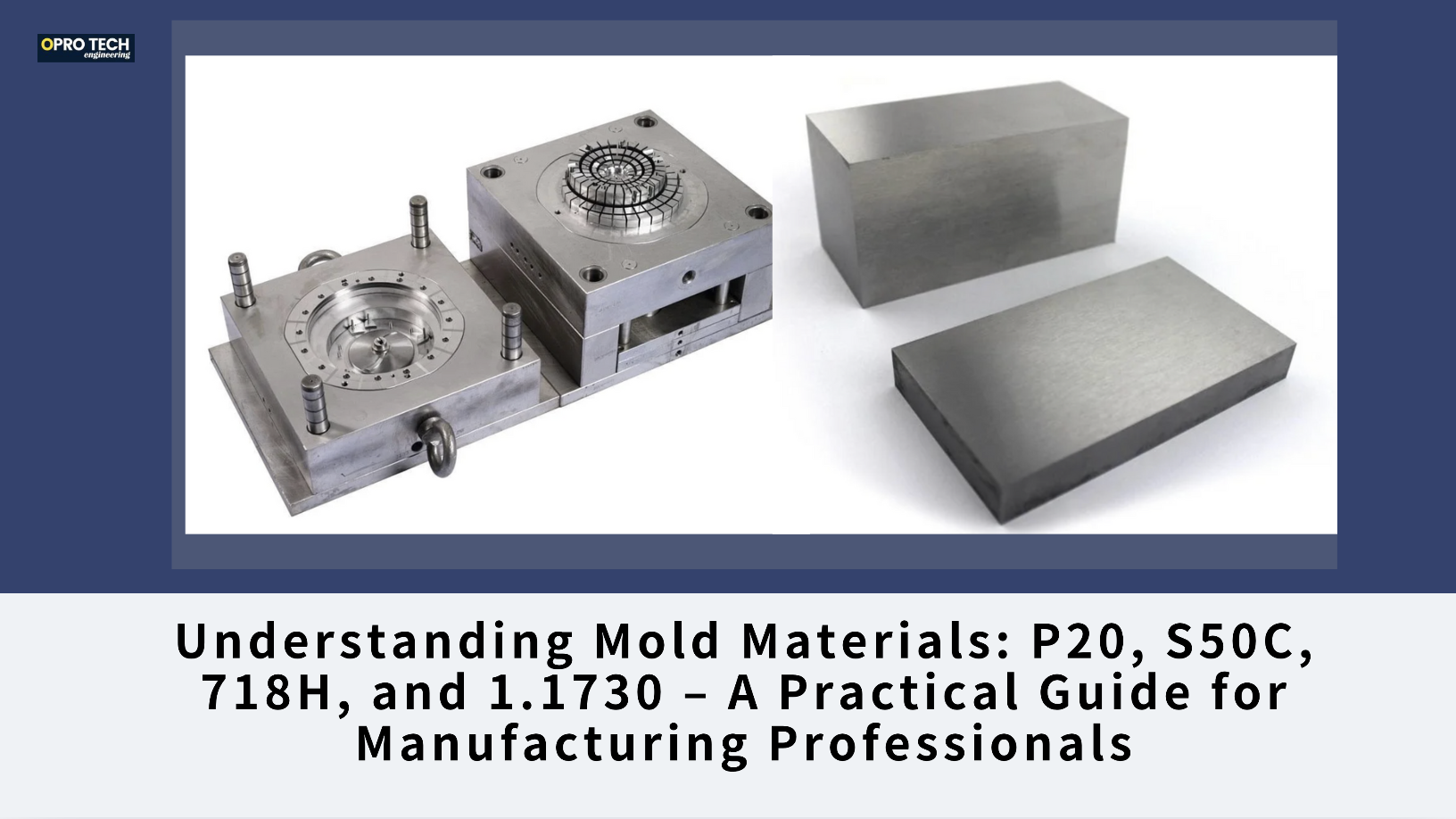
In the mold and tooling industry, choosing the right steel is crucial for product quality, cost control, and production efficiency. In this article, I want to explore some common questions I had while learning about key materials used in mold making: P20, S50C, 718H, and 1.1730. These insights may help fellow professionals like me gain a clearer understanding of how to make smart material choices in daily work.
🔍 What Is Pre-Hardened Material?
A pre-hardened steel is one that has already undergone heat treatment to achieve a specific hardness level (usually 28–38 HRC), before it's machined. This means it can be used directly for making mold cavities or bases without needing further hardening.
✅ Advantages of Pre-Hardened Materials:
- Saves time and cost: No need for post-machining heat treatment.
- Dimensional stability: No distortion risk from heat treatment.
- Good toughness: Can handle injection pressure without cracking.
- Better efficiency: Speeds up the overall mold-making process.
Common pre-hardened steels include P20 and 718H.
❓ Why Do We Need to Harden Steel If It’s Not Pre-Hardened?
If a steel is not pre-hardened (like S50C or 1.1730 in annealed condition), it’s still soft and:
- Can wear out quickly
- Might deform under pressure
- Doesn’t have the required surface hardness for mold cavities
That’s why post-machining heat treatment is essential — it improves wear resistance, strength, and service life.
Typical steps:
- Machine the soft material (easy to cut)
- Then heat treat it to achieve final hardness
📦 Material Standards: What Do AISI, DIN, and JIS Codes Mean?
Each country or region has its own steel standard system:
Code | Organization | Region |
AISI | American Iron & Steel Institute | USA |
DIN | Deutsches Institut für Normung | Germany / EU |
JIS | Japanese Industrial Standards | Japan |
For example:
- AISI 1050 ≈ JIS S50C
- DIN 1.2311 ≈ AISI P20
These codes help global teams communicate clearly across regions when specifying materials.
🔧 Comparison of P20, S50C, 718H, and 1.1730
Here’s a practical comparison for engineers, mold makers, and project managers:
Property | P20 | S50C | 718H | 1.1730 |
Type | Pre-hardened tool steel | Medium-carbon steel | Modified pre-hardened tool steel | Mild carbon steel |
Hardness | 28–32 HRC | 15–20 HRC (annealed) | 33–38 HRC | 12–18 HRC (annealed) |
Heat Treatment Needed | ❌ No | ✅ Yes | ❌ No | ✅ Rarely |
Machinability | Good | Excellent | Moderate | Excellent |
Polishability | Medium | Poor | Excellent | Poor |
Use Case | Mold cavity / base | Mold base | High-end mold cavity | Mold frame or plate |
🧠 Practical Application Guide
Use Case | Recommended Material |
Mold cavity (standard) | P20 |
Mold cavity (mirror finish/textured) | 718H |
Mold base (cost-effective) | S50C or 1.1730 |
Mold base (durable) | P20 |
General mechanical part | S50C |
💬
For professionals in mold manufacturing, understanding the differences between these materials helps ensure better mold design, lower costs, and more reliable production. As I learned through exploring these questions, pre-hardened materials like P20 and 718H are often ideal for cavities, while cost-effective steels like S50C and 1.1730 are great for bases and structural parts.
Whether you’re working with clients, suppliers, or your own team, knowing the “why” behind material selection can improve communication and decision-making across the board.
Dan
Factory add: No 39, Zhen an west road, Changan town , Dong guan city, China.