Understanding Insert Tooling Molds: Focus on Screw Thread Bushings and Solutions for Overflow Issues
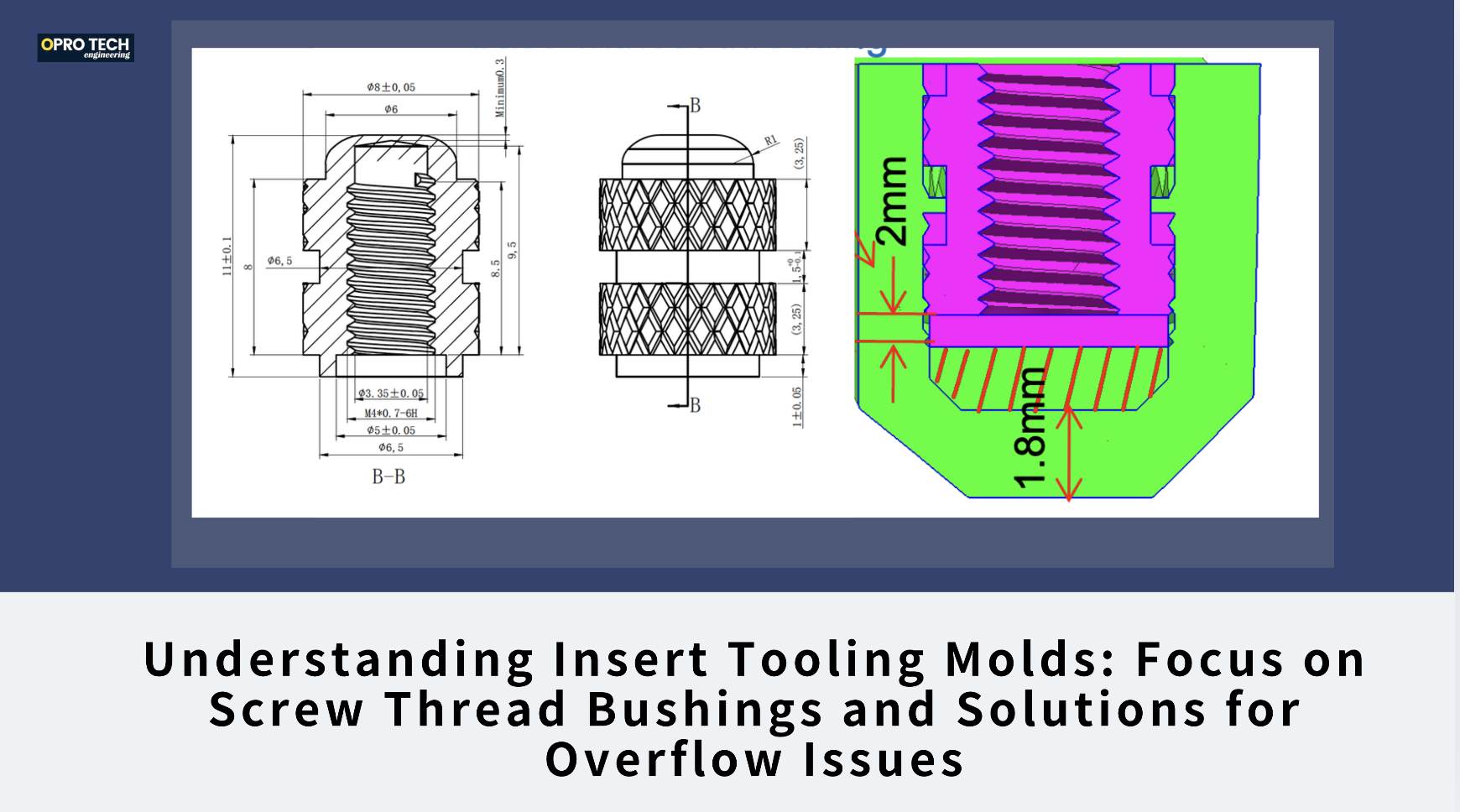
Insert tooling mold is a widely used process in plastic injection molding, especially when combining metal components (like nuts, screws, or bushings) with plastic parts to create functional, durable products. Among these, screw thread bushings are essential components in many mechanical assemblies, allowing for strong fastening and disassembly without damaging plastic threads.
However, while insert molding can greatly enhance product functionality, it also introduces challenges in the molding process — particularly material overflow (flash) around the insert. This article will explain what insert tooling molds are, the issues often encountered with screw thread bushings, and actionable solutions to prevent defects.
1. What is Insert Tooling Mold?
Insert molding is an injection molding process where metal inserts (such as screw thread bushings, nuts, or other fasteners) are placed inside a mold, and plastic material is injected around them to form a single, integrated part. This process provides several benefits:
- Strong mechanical connection between plastic and metal.
- Improved product durability and load-bearing capacity.
- Allows functional components like threads to be integrated without costly post-processing.
2. Focus on Screw Thread Bushings
Screw thread bushings are commonly used inserts designed to accept threaded fasteners. They allow for:
- Secure and repeatable fastening.
- Maintenance and repair-friendly design (disassembly and reassembly).
- Distribution of stress loads on the plastic part.
Typical industries using these inserts include automotive, electronics, consumer products, medical devices, and industrial equipment.
3. Common Problems in Insert Molding with Screw Thread Bushings
Despite its advantages, insert molding presents several challenges when it comes to bushings, including:
⚙️ a) Material Overflow / Flash Around Insert
- Plastic material flows into the screw threads or gaps, leading to defective threads or unclean appearance.
- Causes functional failure (e.g., screws can't be inserted properly).
⚙️ b) Insert Shift or Misalignment
- Insert moves from its intended position during injection, causing improper placement or incomplete encapsulation.
⚙️ c) Weak Bonding Between Insert and Plastic
- Insufficient bonding leads to insert pull-out or spinning inside the plastic part under load.
4. Why Does Overflow Happen?
Several reasons contribute to overflow (flash) and other defects during the molding process:
5. How to Solve Insert Molding Problems with Screw Thread Bushings
Here are practical solutions that manufacturers and molders can apply:
✅ a) Precision Mold Design for Insert Seating
- Design tight tolerance cavities that perfectly match the insert’s shape.
- Avoid oversized cavities — aim for light press-fit when possible.
✅ b) Incorporate Locating Features
- Use locating pins, shoulders, or pockets to hold inserts firmly in place.
- Consider robotic or magnetic positioning for high-precision requirements.
✅ c) Optimize Injection Parameters
- Reduce injection pressure and speed when molding around inserts to minimize force pushing plastic into gaps.
- Use multi-stage injection (slow-fast-slow) to control flow around sensitive areas.
✅ d) Preheat Metal Inserts (Optional)
- Preheating inserts can reduce thermal expansion gaps and promote better bonding with plastic.
- Typical preheating temperature: 50-80°C, depending on material combination.
✅ e) Mold Venting
- Design proper vents near inserts to allow trapped air to escape and prevent back pressure buildup.
✅ f) Modify Insert Design for Better Bonding
- Use knurled, undercut, or grooved inserts to mechanically lock into the plastic.
- Ensure the insert surface is clean and free of oils or contaminants.
6. Case Study Example: Overcoming Overflow on Threaded Bushing Insert
In one of our recent projects, we were molding a glass-filled Nylon part with threaded brass bushings. Initially, plastic overflowed into the internal threads, rendering them unusable. After analysis, we applied these improvements:
- Redesigned the insert cavity with tighter tolerance for a precise fit.
- Added locating shoulders to fix axial and radial movement.
- Reduced injection pressure by 20% and used a slow initial injection speed.
- Preheated inserts to 60°C before molding.
As a result, we achieved perfect, clean threads with no flash and strong insert bonding.
Insert tooling molds, especially those involving screw thread bushings, are critical for manufacturing functional plastic parts. While challenges like overflow and misalignment are common, proper mold design, optimized process parameters, and thoughtful insert engineering can eliminate these issues and ensure high-quality results.
If you're facing challenges with insert molding or need consultation on mold design, feel free to reach out — we'd be happy to share insights or support your project!
Dan
Factory add: No 39, Zhen an west road, Changan town , Dong guan city, China.