Solving Demolding Issues in Injection Molding: Causes, Solutions, and a Real-World Case Study
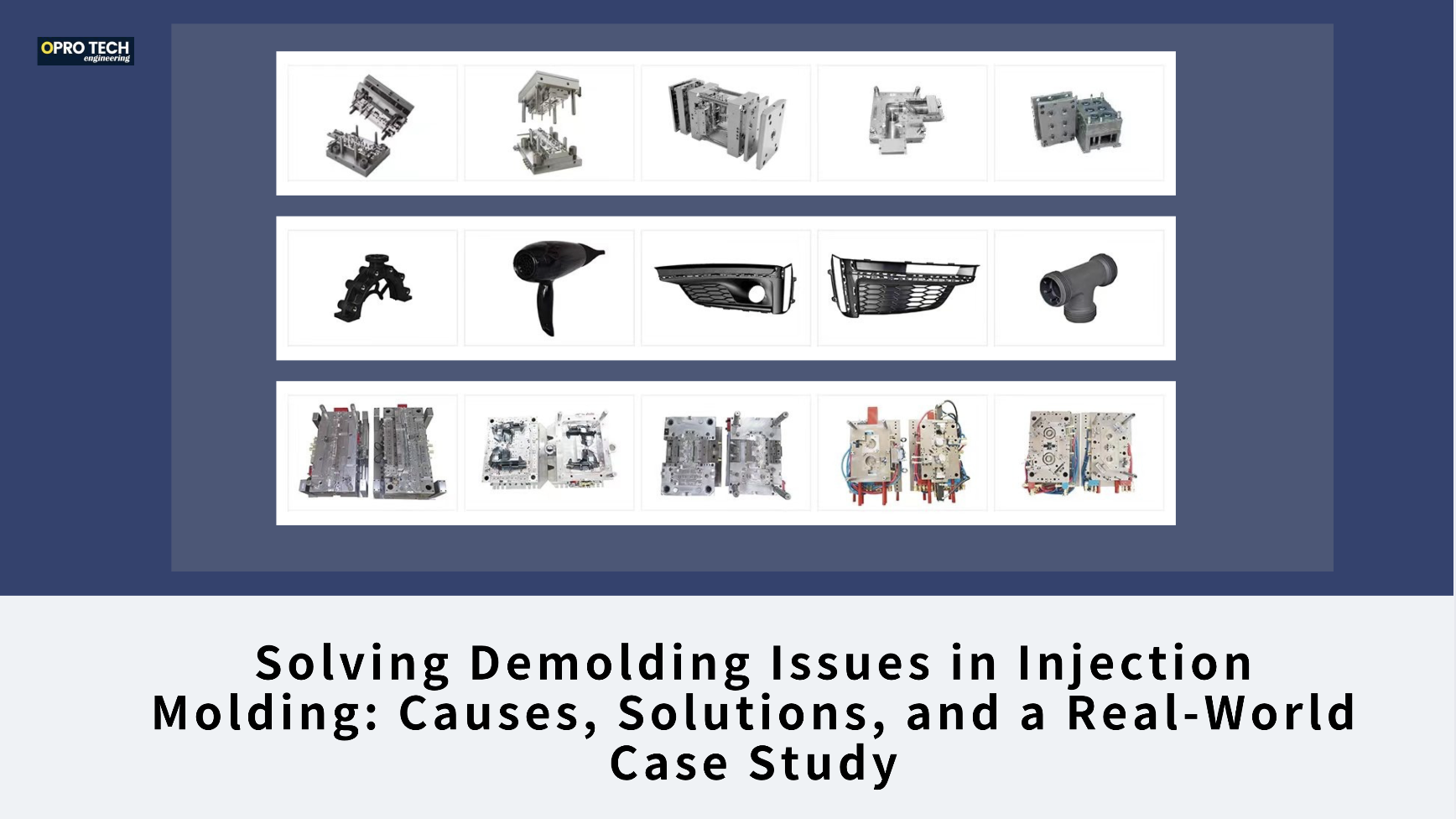
In injection molding, one of the most common challenges manufacturers face is the demolding problem, where the molded part sticks to the cavity or core side of the mold, making it difficult to eject the part properly. This problem can lead to increased cycle times, reduced productivity, and even part defects. In this article, we will explore the common causes of demolding issues, potential solutions, and a real-world case study of how we tackled this issue during the production of a bottom housing part.
Understanding the Demolding Issue
Demolding is the process of removing the molded part from the injection mold after the plastic material has solidified. However, if a part gets stuck, it can affect the quality of the product and the efficiency of the manufacturing process. In many cases, the part sticks to the cavity side (where the texture is applied) and is difficult to eject. This can cause damage to both the part and the mold, as well as extend production times.
Key Factors That Contribute to Demolding Problems:
1. Texture on the Cavity Side
The cavity side often contains surface textures for aesthetic or functional purposes. Textured surfaces naturally create friction, and the part can "stick" to the cavity during demolding, especially if the mold opening is too tight or there is insufficient ejection force.
2. Lack of Features on the Core Side
If the part lacks mechanical features on the core side, such as ribs or bosses, the plastic material may shrink and cling tightly to the cavity side after cooling, making it difficult for ejector pins to push the part out.
3. Uneven Cooling and Shrinkage
Improper cooling can cause uneven shrinkage, which increases the likelihood of the part sticking to one side of the mold, typically the cavity side, due to how the material contracts as it cools.
4. Inadequate Ejector System
An insufficient or poorly placed ejector system on the core side can lead to a lack of proper force to release the part. In extreme cases, this can result in the part remaining stuck to the cavity after the mold is opened.
Root Causes of Demolding Issues
1. Shrinkage and Grip on the Cavity Side
- Texture and surface features can increase friction between the molded part and the cavity surface. As the plastic material cools, it shrinks and sticks to the cavity side, creating a strong bond.
2. Imbalance in Forces
- If the core side lacks sufficient features (e.g., ribs), the part may cling to the cavity side. Without ribs or undercuts on the core side, the part might be unable to separate properly when the mold opens.
3. Mold Design and Venting
- Poor mold design or lack of proper venting can create suction forces during demolding, which can make the part "stick" in the cavity. Proper venting allows air to escape, reducing the chances of a vacuum forming between the part and the cavity surface.
4. Inadequate Ejection Mechanism
- If the ejector pins or ejector plates are not properly placed or aligned, it may not provide enough force to push the part out of the mold, leading to it being stuck on the cavity side.

Solutions to Demolding Problems
1. Adding Features to the Core Side
To counteract the forces that cause the part to stick to the cavity side, adding ribs, bosses, or other mechanical features on the core side can help. These features act as anchors, ensuring that the plastic material does not cling too tightly to the cavity side, thus balancing the forces and aiding proper ejection.
2. Improving Ejector System
Ensure that the ejector pins or ejector plates are placed strategically on the core side. These should be positioned in areas where they can apply force to push the part out evenly, preventing it from staying attached to the cavity side.
3. Optimizing Mold Cooling
Implement even cooling by ensuring that cooling channels are properly designed and uniformly distributed around the mold. This helps prevent uneven shrinkage and reduces the likelihood of the part sticking.
4. Applying Proper Draft Angles
Applying draft angles to the part design (especially for vertical walls) reduces friction during demolding. Typically, a 1-2 degree draft is sufficient, but deeper textures may require larger angles.
5. Enhancing Mold Venting
Proper mold venting is essential to allow trapped air to escape. Without adequate venting, the air trapped inside the mold can create vacuum forces that hold the part to the cavity. Ensure that venting holes are added to critical areas.
Real-World Case Study: Solving Demolding Issues in Bottom Housing Part
The Challenge
We encountered a demolding issue during the production of a bottom housing part that featured a textured surface on the cavity side. After injection, the part would get stuck to the textured cavity side, making it difficult to eject. This problem led to increased cycle times and, in some cases, part defects.
Our Solution
To resolve this, we added strong ribs on the core side of the part. These ribs acted as mechanical features that helped balance the forces during cooling and ejection. The result was that the part no longer clung to the textured cavity side and could be easily ejected.
By creating more features on the core side, we ensured that the plastic material would not shrink and stick exclusively to the cavity side. Instead, the added ribs helped the part stay anchored to the core side, allowing the ejector system to perform its function smoothly.
Outcome
After the implementation of the core-side ribs, the demolding issue was successfully resolved. The part was ejected consistently without sticking, and production cycle times returned to normal.
Conclusion
Demolding issues are a common challenge in injection molding, but with careful attention to mold design, cooling systems, and ejection mechanisms, they can be effectively addressed. By understanding the root causes and applying solutions such as adding features on the core side, optimizing ejector systems, and ensuring proper cooling, manufacturers can reduce cycle times and improve part quality.
Our real-world case study demonstrates how a seemingly small design change, like adding ribs to the core side, can have a significant impact on solving demolding issues and improving production efficiency.
By sharing this knowledge and learning from practical experiences, we aim to improve our processes and continue delivering high-quality molded parts for our clients.
About Us:
[Opro tech engineering] is committed to providing innovative manufacturing solutions for a variety of industries. Our expertise in injection molding, CNC machining, and prototyping allows us to tackle complex challenges and deliver high-quality, precise parts every time.
Factory add: No 39, Zhen an west road, Changan town , Dong guan city, China.