Understanding Plastic Material Data Sheets: Why They Matter in Mold Design and Injection Molding
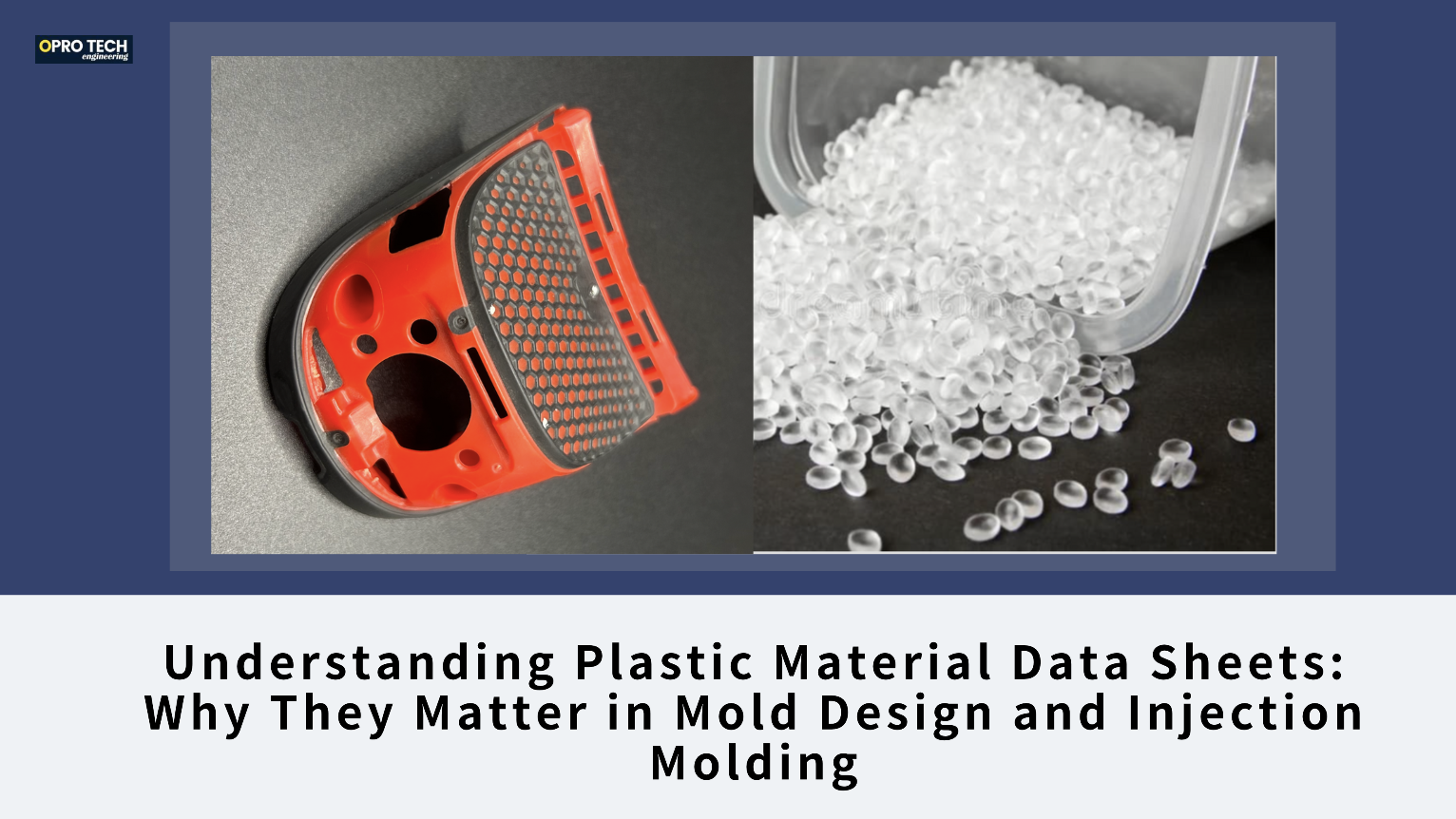
Understanding Plastic Material Data Sheets: Why They Matter in Mold Design and Injection Molding
As someone in sales, I always strive to learn more about the technical aspects of the manufacturing process. One key area I’ve been diving into is how plastic material data sheets influence mold design and injection molding. Understanding this is essential, not just for engineers but also for those of us in sales who want to provide real value to our clients.
What is a Plastic Material Data Sheet?
A plastic material data sheet provides essential information about a specific plastic resin, including its physical, mechanical, thermal, and processing properties. Manufacturers use this data to determine how the material behaves during molding and what parameters should be set to achieve the best results.
Key Parameters in a Plastic Material Data Sheet
When designing a mold and setting up injection molding processes, several key parameters must be considered:
1. Shrinkage Rate (%)
o Plastic shrinks as it cools. The shrinkage rate helps designers determine how much to compensate for in the mold cavity to ensure the final part dimensions are accurate.
2. Melt Flow Index (MFI or MFR, g/10min)
o Indicates how easily the material flows when melted.
o Affects injection pressure and the ability to fill complex geometries.
3. Glass Transition Temperature (Tg, °C)
o The temperature at which the plastic changes from rigid to rubbery.
o Helps in choosing suitable working temperatures for the part.
4. Melt Temperature (Tm, °C)
o The temperature at which the material fully melts.
o Must be controlled to avoid degradation and ensure proper flow.
5. Mold Temperature (°C)
o A crucial factor in controlling cooling time, part warpage, and surface finish.
o Too low a mold temperature can lead to poor filling, while too high can slow down production.
6. Drying/Moisture Content
o Some plastics, like PA (Nylon), PET, and PC, absorb moisture and need proper drying before molding.
o Excess moisture can lead to defects like bubbles, weak parts, and surface imperfections.
7. Injection Pressure & Holding Pressure
o Determines how effectively the molten plastic fills the mold and maintains shape during cooling.
8. Cooling Time
o The estimated time required for the part to solidify before ejection.
o Longer cooling times ensure stability but affect cycle time efficiency.
Do We Need to Follow the Data Sheet Exactly?
Yes and no. While the data sheet provides recommended settings, real-world adjustments are often necessary. Here’s how different parameters play a role:
· Shrinkage Rate Must Be Considered in Mold Design
o If ignored, the final part may be too large or too small.
· Mold Temperature Affects Quality and Efficiency
o If too low, the part may have poor surface quality or incomplete filling.
o If too high, it extends cooling time and affects productivity.
· Moisture Content is Critical for Some Plastics
o Ignoring drying recommendations can lead to defective parts with poor mechanical properties.
· Processing Temperatures and Pressures Can Be Adjusted
o While recommended ranges exist, fine-tuning during mold trials ensures the best balance between quality and cycle time.
Why This Matters to Sales Professionals
As a sales professional, knowing this information allows me to communicate better with clients. If a client is experiencing issues with their molded parts, I can ask the right questions and offer insights rather than just passing the issue to the engineering team. It helps build trust and positions me as a knowledgeable partner rather than just a salesperson.
Learning a little every day about mold design and processing makes a huge difference. While following the plastic material data sheet is crucial, practical adjustments are often necessary for optimal results. By understanding these key parameters, we can ensure high-quality parts, efficient production, and better customer satisfaction.
If you're working with injection molding and want to discuss material selection or troubleshooting, feel free to reach out! I’d love to learn and exchange knowledge with you.
Dan
Factory add: No 39, Zhen an west road, Changan town , Dong guan city, China.