What is SPI AN-102-78? What is the Classification of Injection Molds?
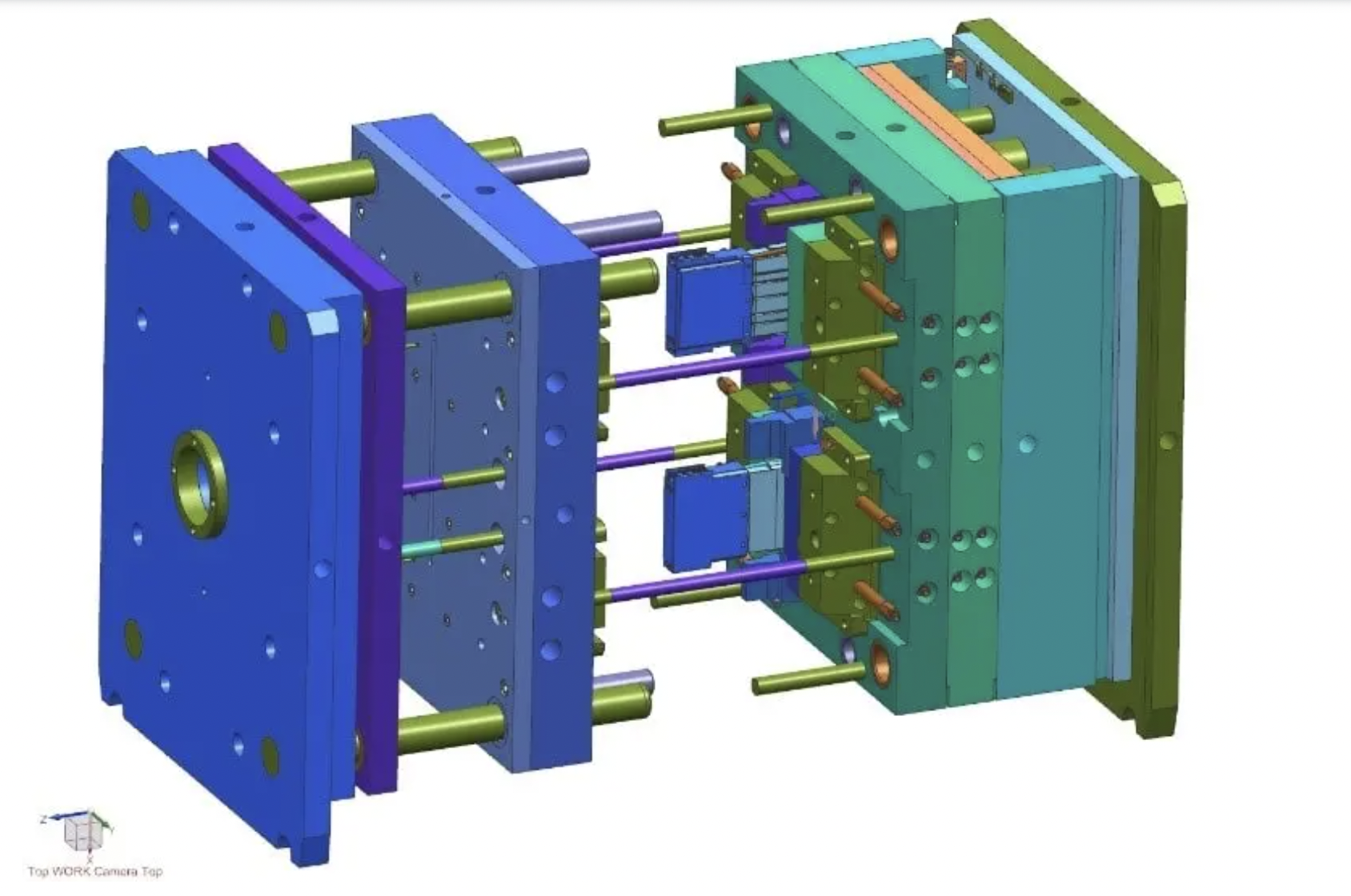
I came across some valuable information about SPI AN-102-78 in my recent learning endeavors. I hope it proves helpful for you if you happen to be seeking insights into this mold standard.
But honestly, I'm uncertain about the accuracy of this summary, considering the learning material I consulted isn't officially authorized. If you come across anything that seems inaccurate, please feel free to share your observations below.
According to this material, the SPI standard classifies molds based on tonnage, distinguishing between those for up to 400 tons and those for 400 tons or more.
For molds up to 400 tons, it further categorizes them into Class 101, Class 102, Class 103, Class 104, and Class 105 molds. Additionally, it includes Class I Unit Insert and Class II Unit Insert.
On the other hand, molds for 400 tons or more fall into categories such as Class 401, Class 402, Class 403, and Class 404 molds.
For more detailed information, please refer to the content provided below . Your insights are appreciated. Thanks.
(A) Classification of Injection Molds for up to 400 Tons.
Class 101 Mold
Cycles: One million or more.
Description: Built for extremely high production. This is the highest-priced mold and is made with only the highest quality materials.
Requirements:
(1) Detail mold design required.
(2) Mold base to be minimum hardness of 280 BHN.
(3) Molding surfaces (cavities and cores) must be hardened to a minimum of 48 R/C range. All other details, such as slides, heel blocks, gibs, wedge blocks, etc. should also be of hardened tool steels.
(4) Ejection should be guided.
(5) Slides must have wear plates.
(6) Temperature control provisions to be in cavities, cores and slides wherever possible.
(7) Over the life of the mold, corrosion in the cooling channels decreases cooling efficiency thus degrading part quality and increasing cycle time. It is therefore recommended that plates or inserts containing cooling channels be of a corrosive resistant material or treated to prevent corrosion.
(8) Parting line locks are required on all molds.
Class 102 Mold
Cycles: Not exceeding one million.
Description: Medium to high production mold, good for abrasive materials and/or parts requiring close tolerances. This is a high quality, fairly high-priced mold.
Requirements:
(1) Detail mold design required.
(2) Mold base to be minimum hardness of 280 BHN.
(3) Molding surfaces (cavities and cores) must be hardened to a minimum of 48 R/C range. All other details should be made and heat treated.
(4) Temperature control provisions to be in cavities, cores and slides wherever possible.
(5) Parting line locks are recommended for all molds.
(6) The following items may or may not be required depending on the ultimate production quantities anticipated. It is recommended that those items desired be made a firm requirement for quoting purposes.
(a) Guided ejection.
(b) Slide Wear plates.
(c) Corrosive resistant temperature control channels.
(d) Plated cavities.
Class 103 Mold
Cycles: Under 500,000.
Description: Medium production mold. This is a very popular mold for low to medium production needs. Most common priced range.
Requirements:
(1) Detail mold design recommended.
(2) Mold base to be minimum hardness of 165 BHN.
(3) Cavities and cores must be 280 BHN or higher.
(4) All other extras are optional.
Class 104 Mold
Cycles: Under 100,000.
Description: Low production mold. Used only for limited production preferably with non-abrasive materials. Low to moderate price range.
Requirements:
(1) Mold design recommended.
(2) Mold base can be of mild steel or aluminum.
(3) Cavities can be of aluminum, mild steel or any other agreed upon metal.
(4) All other extras are optional.
Class 105 Mold
Cycles: Not exceeding 500.
Description: Prototype only. This mold will be constructed in the least expensive manner possible to produce a very limited quantity of prototype parts.
Requirements:
May be constructed from cast material or epoxy or any other material offering sufficient strength to produce minimum prototype pieces.
Class I Unit Insert
Cycles: Approximately 500,000.
Description: Top quality materials for medium to high production requirements.
Requirements:
(1) Detail mold design required.
(2) Insert retainer to be uniform of at least 280 BHN.
(3) All molding or functional details are to be made of tool steel hardened to at least 48 R/C.
(4) Slides must have wear plates.
(5) Temperature control provisions to be in cavities, cores and slides wherever possible.
(6) Over the life of the mold, corrosion in the cooling channels decreases cooling efficiency thus degrading part quality and increasing cycle time. It is therefore recommended that plates or inserts containing cooling channels be of a corrosive resistant material or treated to prevent corrosion.
(7) Parting line locks are required on all molds.
(8) Insert retainers must have leader pins and bushings or some similar guidance system.
Class II Unit Insert
Cycles: Under 100,000.
Description: Similar to Class 104 Mold. Most commonly used insert. Low to medium production.
Requirements:
(1) Detail mold design recommended.
(2) Insert retainer to be uniform of at least 165 BHN.
(3) Cavities and cores must be 280 BHN or higher.
(4) Water channels to be included.
(5) All other extras are optional.
Cycles: Less than 500.
Description: Similar to Class 105 Mold. Least expensive insert for very limited quantities. Insert built with the least expensive materials.
Requirements:
May be constructed from aluminum, cast epoxy or any material with sufficient strength to produce minimum prototype pieces.
(B) Classification of Injection Molds for 400 Tons or more.
Class 401 Mold
Cycles: 500,000 or more.
Description: Built for extremely high production. This is the highest-priced mold and is made with only the highest quality materials.
Requirements:
(1) Detail mold design required.
(2) Mold base to be minimum hardness of 280 BHN.
(3) Molding surfaces (cavities and cores) must be hardened to a minimum of 48 R/C range. All other details, such as slides, heel blocks, gibs, wedge blocks, etc. should also be of hardened tool steels.
(4) Ejection should be guided.
(5) Slides must have wear plates.
(6) Temperature control provisions to be in cavities, cores and slides wherever possible.
(7) Over the life of the mold, corrosion in the cooling channels decreases cooling efficiency thus degrading part quality and increasing cycle time. It is therefore recommended that plates or inserts containing cooling channels be of a corrosive resistant material or treated to prevent corrosion.
(8) Parting line locks are required on all molds.
Class 402 Mold
Cycles: Not exceeding 500,000.
Description: Medium to high production mold, good for abrasive materials and/or parts requiring close tolerances. This is a high quality, fairly high-priced mold.
Requirements:
(1) Detail mold design recommended.
(2) Mold base to be minimum hardness of 165 BHN.
(3) Molding surfaces should be hardened to 280-310 BHN or 320-350 BHN depending
on the complexity of the part and performance expected. The higher hardness the longer the mold life.
(4) All other functional details should be made at least 48 R/C.
(5) Parting line locks are recommended for all molds.
(6) The following items may or may not be required depending on the ultimate production quantities anticipated. It is recommended that those items desired be made a firm requirement for quoting purposes.
(a) Guided ejection.
(b) Slide Wear plates.
(c) Corrosive resistant temperature control channels.
(d) Plated cavities.
Class 403 Mold
Cycles: Under 100,000.
Description: Medium production mold, this is a very popular mold for low to medium production needs. Most common price range.
Requirements:
(1) Mold design recommended.
(2) Mold base can be of mild steel or aluminum.
(3) Cavities can be of aluminum, mild steel or any other agreed upon metal.
(4) All other extras are optional.
Class 404 Mold
Cycles: Not exceeding 500.
Description: Prototype only. This mold will be constructed in the least expensive manner possible to produce a very limited quantity of prototype parts.
Requirements:
May be constructed from cast metal or epoxy or any other material offering sufficient strength to produce minimum prototype parts.
Thanks for your reading and looking forward to your feedback. Thanks.