Understanding IMD, IML, IMT, and IME Technologies in the Injection Molding Industry
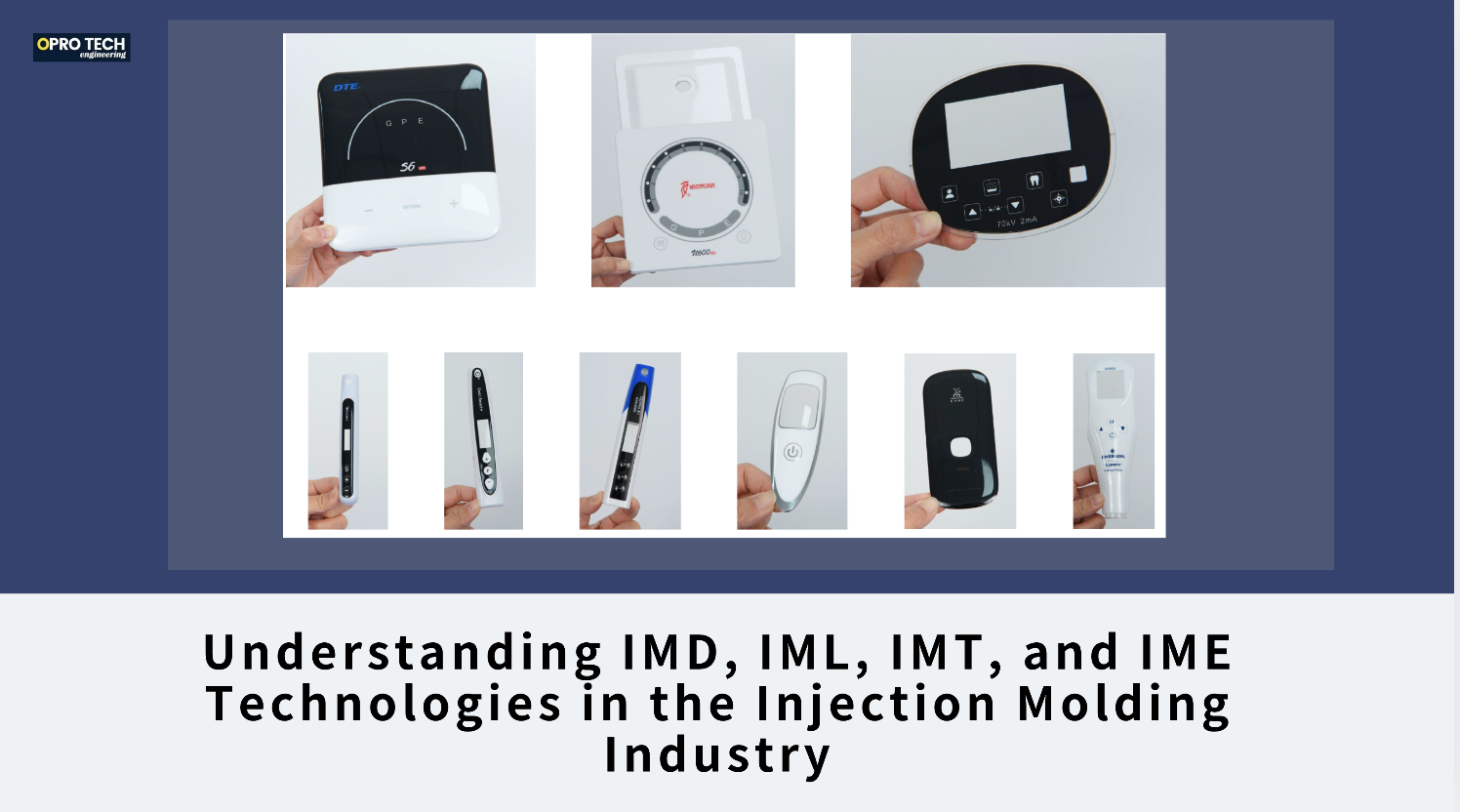
In the field of injection molding and tooling, several advanced technologies have emerged to meet the growing demand for aesthetic design, functionality, and product integration. Among them, IMD, IML, IMT, and IME are widely discussed and applied. This article explains what each technology means and how they are related.
IMD (In-Mold Decoration)
Definition:
IMD is a process where a decorative film is inserted into the injection mold, and during molding, the plastic material bonds with the film to form a finished part with an integrated decoration.
Key Features:
- Offers rich, high-end surface appearances (metallic effects, gloss, brushed textures, etc.).
- Decoration is highly durable and resistant to abrasion.
- No need for secondary surface treatments after molding.
Typical Applications:
Mobile phone covers, automotive interior panels, home appliance surfaces.
IML (In-Mold Labeling)
Definition:
IML involves placing a pre-printed label or film (usually PP or PET) into the mold before injection. The label bonds with the molten plastic, becoming an integral part of the final product.
Key Features:
- Label and plastic form a unified piece—high durability.
- Enables vivid colors, complex graphics, and even anti-counterfeiting features.
- Highly efficient and suitable for mass production.
Typical Applications:
Food containers, beverage bottles, cosmetic packaging, electronic product casings.
IMT (In-Mold Transfer)
Definition:
IMT is a process where a transfer film with patterns is placed inside the mold, and during molding, only the pattern is transferred onto the surface of the part. The film itself is removed after the process.
Key Features:
- Enables complex 3D surface decorations.
- Results in a fine, durable, and clean surface without leaving the film.
- Often offers scratch resistance, fingerprint resistance, and other surface protections.
Typical Applications:
High-end electronics, automotive interiors, premium home appliances.
IME (In-Mold Electronics)
Definition:
IME is an advanced technology that integrates functional electronics directly into plastic parts during the injection molding process. Conductive inks, circuits, sensors, and even LEDs are printed onto a flexible film, which is then molded into a final product.
Key Features:
- Creates smart plastic parts that are lightweight and highly functional.
- Eliminates the need for traditional PCBs and complex assemblies.
- Provides waterproof, dustproof, and more durable solutions.
- Enables thinner, more flexible, and more innovative product designs.
Typical Applications:
Automotive control panels, wearable devices, smart home panels, medical equipment.
Relationship Between IMD, IML, IMT, and IME
Technology | Main Purpose | Film Status | Functional Level | Typical Use |
IMD | Surface decoration | Film remains on product | Aesthetic | High-end consumer products |
IML | Label integration | Film/label becomes part of product | Branding & information | Packaging, mass-market products |
IMT | Pattern transfer | Only pattern remains, no film | Aesthetic | 3D-shaped electronics, automotive interiors |
IME | Functional integration | Film with circuits integrated into product | Smart functionality | Automotive electronics, medical devices |
Summary:
- IMD, IML, and IMT are all based on inserting a film or label into the mold during injection molding.
- IMD and IML leave the film/label in the final product, while IMT only transfers the pattern.
- IME takes the concept to the next level by embedding electronic functionalities into molded parts.
In short, IME can be seen as the evolution of IMD, moving from pure decoration to intelligent integration.
Understanding these technologies not only helps in selecting the right manufacturing method for your products but also opens up new design and innovation possibilities. As manufacturing continues to advance, these in-mold technologies are set to play a critical role in next-generation product development.
Factory add: No 39, Zhen an west road, Changan town , Dong guan city, China.