What is Electrophoretic Deposition(EPD)?
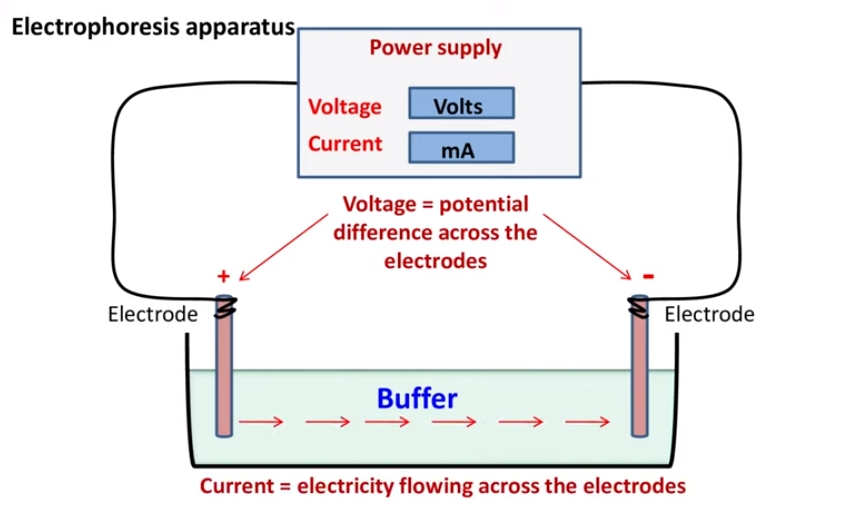
During my studies, I came into contact with a new post-processing method of machining, namely electrophoretic deposition (EPD). This is a technique commonly used to deposit particles or disperse pigments on conductive substrates, and its core principle is to move charged particles in commerce.
While looking up the information, I found that some people mentioned hydrophobicity. In my understanding, hydrophobic is usually a colloid with flowing properties. I would like to understand why hydrophobicity is chosen in certain processes because of the liquid. According to my understanding, short circuit should be processed in liquid. What is the difference between the liquid and colloid?
Here are the basic steps of electrophoretic deposition:
Preparation of particle dispersion: The pigment or particles to be deposited are dispersed in a liquid medium, usually water or an organic solvent. The particles acquire surface charges in this dispersion.
Electrophoretic tank setup: A conductive substrate, often a metal or other highly conductive material, is placed in an electrophoretic tank, and the tank is filled with the particle dispersion.
Application of an electric field: By establishing an electric field in the tank, particles become charged and move under the influence of the electric field. As charged particles migrate toward electrodes of opposite charge, they deposit on the substrate's surface.
Particle deposition: Charged particles deposit onto the substrate's surface, forming a uniform coating. Deposition speed and coating quality can be controlled by adjusting the electric field intensity, processing time, and properties of the particle dispersion. Higher intensity and longer processing times result in thicker coatings on the product surface.
Drying and curing: The deposited particles on the substrate's surface undergo drying and curing processes to form a stable coating.
Electrophoretic coatings offer several advantages, including:
Uniform coating: The electric field ensures a relatively even coating.
Efficiency: Electrophoretic coatings can utilize pigments more efficiently compared to other coating techniques.
Applicability to complex shapes: Due to particle deposition in the electric field, electrophoretic coatings can be applied to various-shaped substrates, including complex three-dimensional structures.
I'm curious about the industries and products that typically require electrophoretic post-processing. Could you provide information on this? Thank you.