Unlocking the Science Behind Reaction Injection Molding: Why Two Liquids Make the Difference
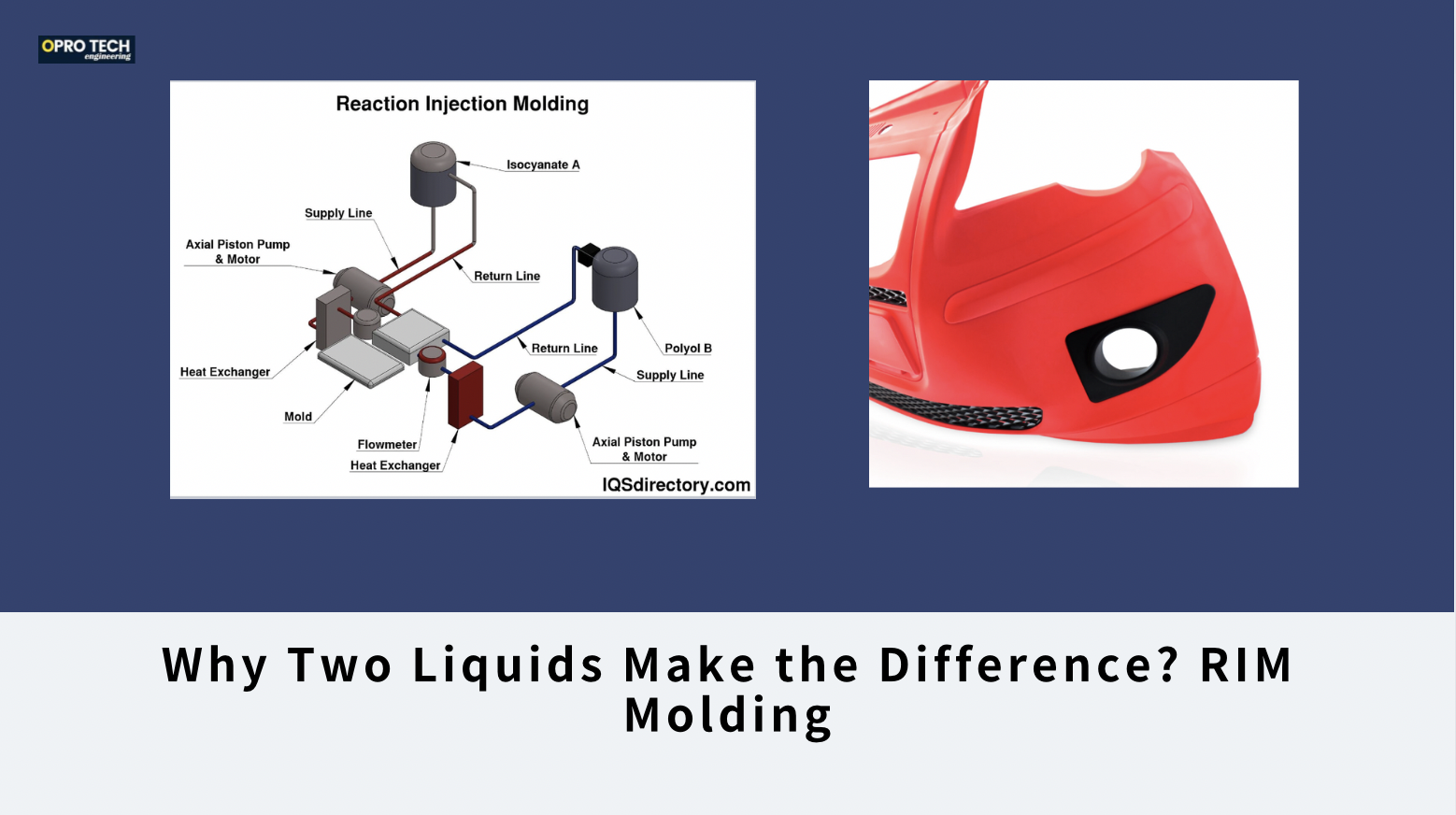
"Unlocking the Science Behind Reaction Injection Molding: Why Two Liquids Make the Difference"
In the world of advanced manufacturing, Reaction Injection Molding (RIM) stands out as a unique process capable of producing strong, lightweight, and complex parts. Unlike traditional molding methods, RIM involves the mixing of two liquid components—usually polyol and isocyanate—that chemically react to form durable polymers such as polyurethane.
This specialized process not only allows for greater design flexibility but also enables manufacturers to create large parts with varying wall thicknesses, all while maintaining a balance between strength and weight. In this article, we'll explore why RIM relies on these two components, how the process works, and the benefits it offers over conventional molding techniques.
Reaction Injection Molding (RIM) is a manufacturing process used to produce lightweight and durable parts, often from polyurethane or similar polymers. It's commonly used in industries like automotive, appliances, and medical equipment to make parts like bumpers, dashboards, and enclosures.
Here’s how it works:
- Mixing the Components: The RIM process involves two liquid components—typically a polyol and an isocyanate—that are mixed together at high pressure in a mixing head. These components react chemically to form a polymer (often a polyurethane or other thermosetting material).
- Injection into Mold: Once mixed, the reacting material is injected into a mold. The reaction between the chemicals generates heat, causing the material to expand and fill the mold.
- Chemical Reaction and Curing: Inside the mold, the mixture undergoes a rapid chemical reaction, solidifying into a finished part. This curing process takes place directly in the mold, creating a durable, lightweight product.
- Ejection of the Part: After the material has fully cured and solidified, the mold is opened, and the part is ejected. Since the materials used in RIM are often thermosetting, the resulting part is highly durable and resistant to impact.
Benefits of RIM:
- Lightweight parts with high strength
- Good for complex shapes and large components
- Lower pressure requirements than traditional injection molding
- Allows for flexible designs with varying wall thicknesses
- Can incorporate foam cores for additional strength and insulation
RIM is often chosen over traditional plastic injection molding when large parts need to be made with strong, lightweight properties.
Reaction Injection Molding (RIM) typically requires two liquid components—usually a polyol and an isocyanate—because these two components chemically react to form the final polymer, such as polyurethane. Here's why two components are necessary:
1. Chemical Reaction (Polymerization):
- RIM is based on a chemical reaction known as polymerization, where the two liquid components undergo a chemical transformation when mixed together. The polyol (a type of alcohol) reacts with the isocyanate to form long polymer chains, which solidify into a thermosetting plastic.
- This process is not possible with just one component because both reactants are needed to trigger the chemical process that creates the final polymer.
2. Customization and Control:
- The two-component system allows for precise control over the final properties of the material, such as hardness, flexibility, or durability. By adjusting the ratio or type of polyol and isocyanate, manufacturers can tailor the mechanical properties of the molded part to meet specific requirements.
- A single liquid wouldn't provide the same level of flexibility in the final product's characteristics.
3. Curing and Solidification:
- The chemical reaction between the two components generates heat, which aids in curing (hardening) the material inside the mold. Without this reaction, the material wouldn’t solidify properly. One liquid on its own would likely not have the necessary reactive properties to undergo such a transformation.
Why One Liquid Won't Work:
Using a single liquid in the RIM process would result in no chemical reaction or curing. The unique property of RIM comes from combining two reactive liquids, which then solidify into a durable, strong part. A single liquid could, in theory, be used in traditional thermoplastic injection molding where no chemical reaction is required, but it wouldn’t work in RIM because the essential reaction wouldn’t happen.
So, the two-component system is fundamental to the chemical nature of the process and the properties it imparts to the final product.
At its core, Reaction Injection Molding (RIM) owes its success to the precise combination of two reactive liquids that come together to form a polymer with remarkable properties. By harnessing the power of chemical reactions, manufacturers can produce parts that are lightweight yet durable, adaptable to complex shapes, and suited to various applications across industries.
Understanding the science behind RIM highlights why this method continues to be a preferred choice for producing high-performance, large-scale components. As technology advances, RIM will likely remain a cornerstone of innovative manufacturing solutions.
Factory add: No 39, Zhen an west road, Changan town , Dong guan city, China.