A Complete Guide to Ultrasonic Welding: How It Works, Sonotrode Design, and Technical Best Practices
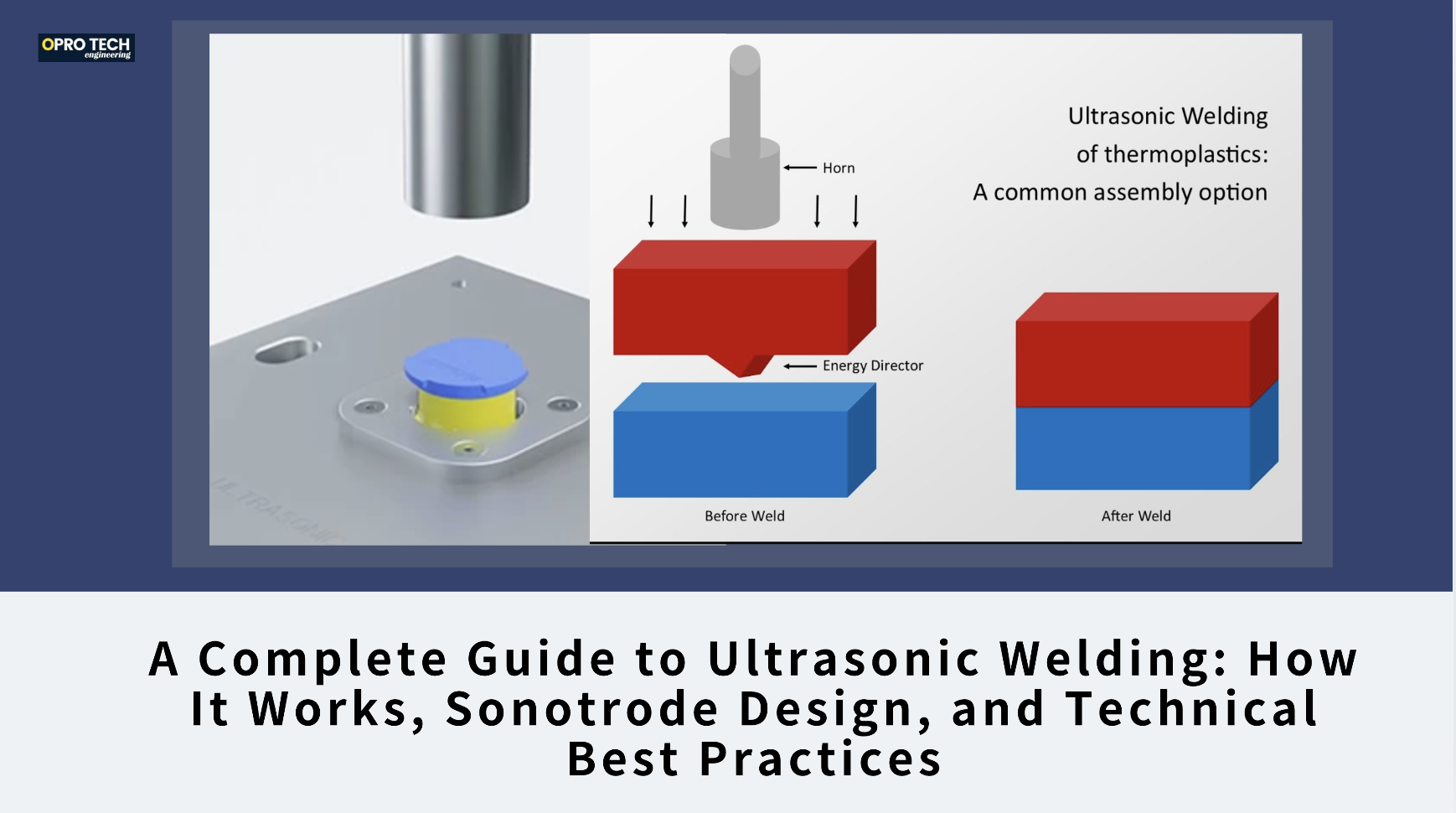
Ultrasonic welding is a widely used and highly efficient method for joining plastic components—particularly in automotive, electronics, and consumer products industries. But to truly take advantage of this technology, it's important to understand not just how it works, but also the critical technical knowledge behind it.
In this guide, we’ll walk through everything from the basic principles to advanced tips on sonotrode design, plastic compatibility, and weld quality.
🔍 What is Ultrasonic Welding?
Ultrasonic welding joins two plastic parts by applying high-frequency acoustic vibrations (usually between 20–40 kHz) under pressure. These vibrations cause frictional heat at the joint line, which melts the plastic. Once the vibration stops, the material solidifies, forming a strong bond.
💡 Key Advantages:
- No need for adhesives, screws, or solvents
- Fast cycle times
- Clean and repeatable
- Suitable for automation
🔧 The Role of the Sonotrode
The sonotrode is the critical component in an ultrasonic welding system—it’s the tool that transmits ultrasonic vibrations directly into the plastic part.
📐 What is a Sonotrode?
A sonotrode (also called a horn) is a specially designed tool made from titanium, aluminum, or steel. It must be:
- Precisely tuned to the target frequency (e.g. 20, 30, or 40 kHz)
- Designed to vibrate in harmony with the ultrasonic system
- Shaped to match the weld area and part geometry
🎯 Designing a Sonotrode: What to Know
Designing an effective sonotrode is a mix of science, engineering, and experience. Here are the key considerations:
1. Frequency Tuning
- The sonotrode must resonate perfectly at the machine’s operating frequency (e.g., 20,000 Hz).
- Finite Element Analysis (FEA) is used to simulate and validate vibration behavior before manufacturing.
2. Geometry
- The contact surface must match the part's shape to ensure even energy distribution.
- Common shapes include flat, contoured, ring-type, or multi-point.
- The total length of the sonotrode typically equals half the acoustic wavelength in the material (½λ).
3. Material
- Titanium: Durable, high-performance, expensive
- Aluminum: Lightweight, low-cost, wears faster
- Steel: Durable, lower cost, lower acoustic efficiency
📊 Choosing the Right Frequency (kHz)
The frequency you choose depends on part size, material type, and precision needs.
Frequency | Best for |
20 kHz | Large parts, high-energy plastics like PP, PE |
30 kHz | Medium-sized parts, general applications |
40 kHz | Small, delicate, or brittle parts like PC, PMMA, ABS |
🔧 Higher frequencies = smaller amplitude and better control, ideal for thin or fragile parts.
🧪 Plastic Types & Frequency Guidelines
Some plastics respond better to higher frequencies due to their physical properties. Here's a quick overview:
Plastic | Suggested Frequency | Notes |
ABS | 35–40 kHz | Brittle, benefits from precision |
Polycarbonate (PC) | 40 kHz | Requires delicate energy application |
PMMA (Acrylic) | 40 kHz | Transparent, needs precise control |
Polypropylene (PP) | 20 kHz | Needs high energy to weld |
Polyethylene (PE) | 20 kHz | Similar to PP, thick sections need more energy |
Nylon (PA) | 20–30 kHz | High melting point, works at lower frequency |
🛠️ Critical Technical Knowledge & Tips
Here are some deeper insights professionals use to improve ultrasonic welding quality:
1. Joint Design Matters
Parts must be designed for ultrasonic welding from the start. Common joint designs include:
- Energy Directors (ED) – for fast melt concentration
- Shear Joints – for hermetic seals
- Tongue-and-Groove / Step Joints – for alignment and appearance
2. Welding Modes
Machines can be set to:
- Time Mode (welds for set time)
- Energy Mode (welds until energy is consumed)
- Collapse Mode (welds until parts compress by set distance)
✨ Energy or collapse mode provides more consistency for high-quality applications.
3. Fixturing is Key
A stable, well-designed fixture is essential:
- Rigid support prevents energy loss
- Proper alignment ensures even welds
- Reduces part movement during welding
4. Plastic Compatibility
Always verify if the materials are weld-compatible:
- Same or chemically similar plastics weld best
- Avoid pairing dissimilar materials unless testing confirms weld strength
5. Preventing Weld Issues
Common problems like voids or weak welds can be avoided by:
- Keeping part surfaces clean (no mold release)
- Using tight part tolerances
- Ensuring the sonotrode is undamaged and well-tuned
6. Sonotrode Wear & Fatigue
Sonotrodes can develop cracks over time from stress. Regular checks and vibration monitoring are recommended—especially in high-volume production.
Ultrasonic welding is a powerful and reliable process—when applied with the right knowledge. From understanding frequency and plastic behavior to designing custom sonotrodes and weld joints, mastering these elements leads to cleaner, stronger, and more efficient assemblies.
If you’re designing a part, troubleshooting welds, or exploring whether ultrasonic welding is the right fit—these insights can guide your decisions and improve your results.
You may want to know more?
“If Sonotrode, it’s just aluminum or titanium... why can’t we just CNC it ourselves?”
Let’s break it down so it makes 100% sense from an engineering and tooling perspective 👇
🎤 Why Can a Sonotrode Deliver Ultrasonic Vibrations?
A sonotrode is not just a machined shape — it’s a tuned acoustic component. Think of it like a guitar string or a tuning fork: it has to vibrate at a specific natural frequency (resonance), and in the correct way (vibration mode).
🔍 The Science Behind It:
- Ultrasonic energy = high-frequency mechanical vibrations (e.g., 20,000 times per second)
- The sonotrode must vibrate in harmony with that frequency (called resonance).
- If the sonotrode is the wrong shape, length, or not balanced correctly, it:
- Won’t vibrate properly
- Will not deliver energy efficiently
- Might crack or damage the parts
⚙️ So Why Not Just CNC It?
You can CNC it — but CNC is only the first step.
Here’s what’s needed for a true ultrasonic sonotrode:
✅ 1. Accurate Resonance Tuning
- The sonotrode must be exactly tuned to match the machine frequency (e.g. 20.000 Hz ± 50 Hz).
- This is done by:
- Designing it to a specific half-wavelength (½λ) length based on sound speed in that metal.
- Using FEA simulation to predict and validate vibration mode shapes.
- Post-machining tuning (material is removed in small amounts to fine-tune the frequency).
📐 Think of this like balancing a crankshaft or camshaft — precision makes or breaks the function.
✅ 2. Correct Vibration Mode
- Sonotrodes must vibrate in longitudinal mode — they stretch and compress like a slinky.
- The nodes and anti-nodes (points of no movement and maximum movement) must be in the right place.
- This ensures that maximum vibration reaches the part without damaging the tool.
If the node is in the wrong place, it can snap or deform from stress.
✅ 3. Surface Matching & Acoustic Behavior
- The contact surface has to:
- Match the part’s weld area perfectly
- Distribute vibration evenly
- Avoid “dead spots” where energy is lost
This involves both mechanical and acoustic design.
✅ 4. Material Properties Matter
Even though it’s aluminum, titanium, or steel—those materials must have:
- Uniform grain structure (no inclusions or voids)
- Proper hardness and fatigue resistance
- Stable acoustic transmission (e.g. titanium resonates better than steel)
Industrial sonotrodes often use ultrasonic-grade titanium for long lifespan and stable vibration.
🛠️ Can You Make One as a Tooling Shop?
Yes, you actually can — especially since you have CNC machines and mold-making knowledge.
BUT — you’ll need:
- Accurate 3D model tuned to the correct frequency
- Vibration testing equipment (or partner with someone who has it)
- Possibly collaborate with ultrasonic machine providers to get tuning specs and validation support
Many shops do end up making their own sonotrodes, especially if:
- They do repeat welding jobs
- Want to customize geometry for special parts
- Or want to reduce costs from buying OEM sonotrodes
✅ Conclusion
So yes — it’s not magic. It’s just physics + precision.
A sonotrode is a piece of aluminum or titanium, but it becomes special because:
- It’s tuned like a musical instrument
- It resonates at ultrasonic frequencies
- It delivers energy efficiently without breaking
Factory add: No 39, Zhen an west road, Changan town , Dong guan city, China.