Mastering FIPG: Key Considerations for Reliable and Durable Sealing
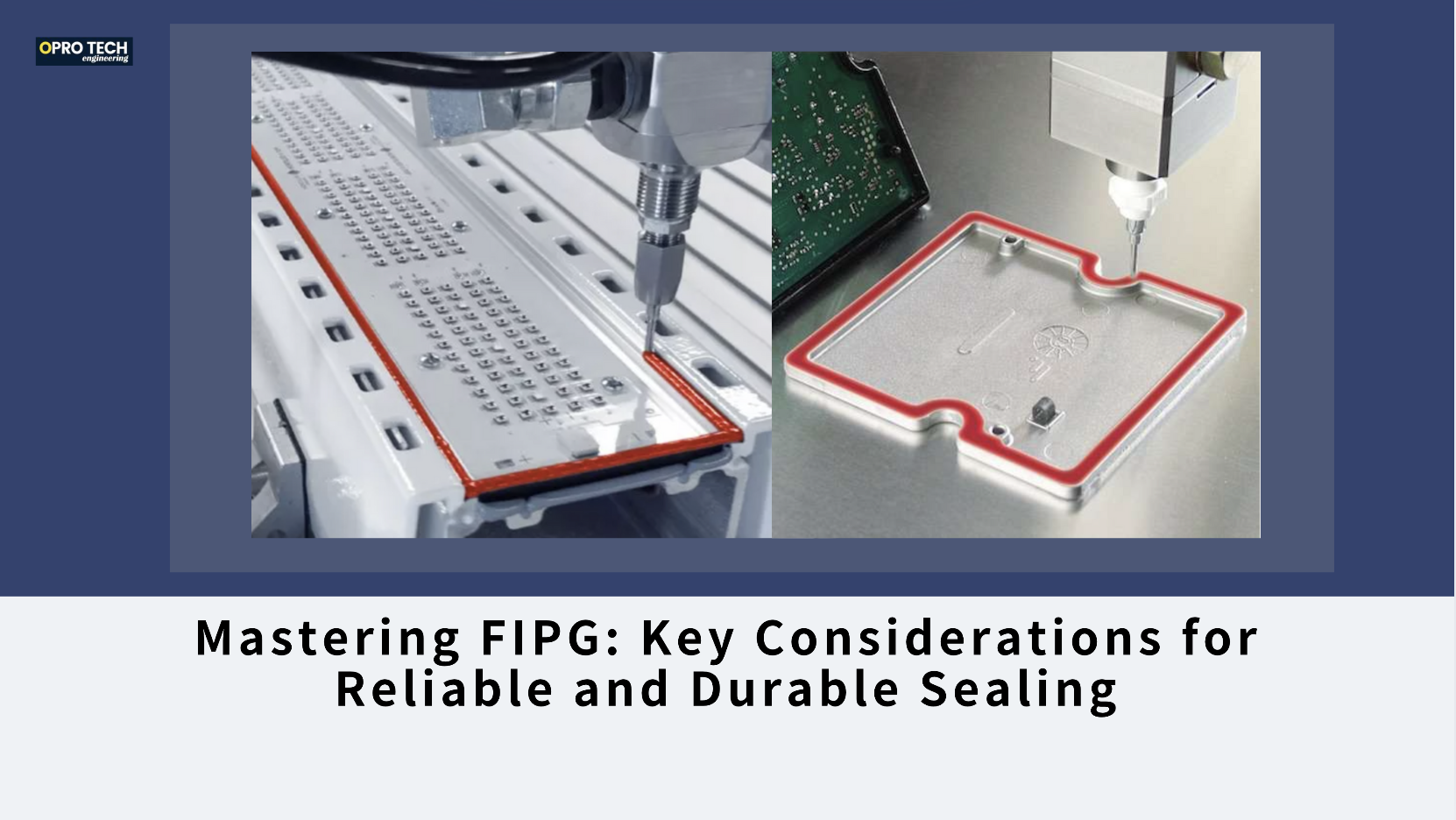
In modern manufacturing and product assembly, Formed-In-Place Gasket (FIPG) technology has become a widely adopted sealing method across industries such as automotive, electronics, and industrial equipment. Its ability to create automated, consistent, and highly reliable seals makes it a compelling alternative to traditional pre-cut gaskets.
In this article, we explore what FIPG is, how it compares to traditional sealing methods, and—most importantly—the critical aspects that must be managed to ensure perfect sealing performance.
✅ What Is FIPG?
FIPG (Formed-In-Place Gasket) is a liquid sealant (often silicone, polyurethane, or epoxy) that is robotically or manually dispensed onto a part surface and then cured in place, forming a flexible and durable gasket. It adheres directly to the mating surface and eliminates the need for separate gasket inventory.
🆚 FIPG vs. Traditional Gaskets
Feature | Traditional Gasket | FIPG |
Installation | Manual | Automated (precise, consistent) |
Sealing Performance | Depends on fit & compression | Conforms perfectly to surface irregularities |
Inventory | Requires different sizes/materials | One material used across many parts |
Design Flexibility | Limited | Highly flexible, design-friendly |
Serviceability | Often replaceable | Typically non-reusable once cured |
In many modern applications, FIPG outperforms traditional gaskets in terms of cost-efficiency, sealing integrity, and production automation.
🔍 FIPG, CIPG, and CIPFG: What’s the Difference?
- FIPG (Formed-In-Place Gasket): The liquid is applied directly and cured in place without any groove. It bonds to the surface and is not reusable.
- CIPG (Cured-In-Place Gasket): Similar to FIPG but typically cured before final assembly and often sits in a groove; allows disassembly and reuse.
- CIPFG (Cured-In-Place Foam Gasket): A variation of CIPG using foamed materials, offering compression and recovery for applications requiring cushioning and sealing.
⚙️ Critical Factors for a Perfect FIPG Seal
To achieve high-performance sealing with FIPG, attention must be paid to several technical and process-related details:
1. Material Selection
Choose the correct gasket compound based on:
- Operating temperature range
- Chemical resistance (e.g., oil, coolant, solvents)
- Flexibility and vibration tolerance
- Curing type (moisture-curing, heat-curing, UV-curing)
💡 Pro Tip: For electronics or automotive, silicone-based FIPG is often preferred due to its high-temperature resistance and elasticity.
2. Surface Preparation
- Surfaces must be clean, dry, and free from oil or dust.
- Improper cleaning can lead to adhesion failure.
- Use a primer if required for specific materials like aluminum or certain plastics.
3. Bead Design & Consistency
- Design the gasket bead size (width, height) precisely to match sealing requirements.
- Typical compression rate: 30%–50% after assembly.
- Uneven beads can create leaks or affect component fitting.
4. Dispensing Accuracy
- Use automated robotic systems for consistent application.
- Poor equipment or manual errors can result in air pockets, uneven flow, or weak seal areas.
5. Curing Process Control
- Respect the curing requirements: time, temperature, humidity.
- Avoid disturbing or compressing the gasket before it’s fully cured.
- If using heat-cured FIPG, ensure proper thermal cycle settings.
6. Assembly Timing
- Some materials require immediate assembly after dispensing.
- Others offer an open time window—know the material’s spec and stick to it.
7. Gap Control Between Parts
- Design the mating surfaces with controlled tolerances.
- Avoid too-tight or overly wide gaps which can compromise compression or bead stability.
8. Environmental Testing
Before full production or critical use, test for:
- Thermal cycling
- Vibration resistance
- Pressure sealing
- Fluid exposure
9. Serviceability Consideration
FIPG creates a permanent bond. If the design requires future disassembly:
- Consider CIPG as an alternative.
- Use a groove design and a reusable material that compresses rather than adheres permanently.
FIPG is a powerful sealing solution—when executed properly. With the right setup, it offers excellent sealing, efficiency, and flexibility for high-volume and automated production. But like many modern manufacturing technologies, the devil is in the details.
By carefully controlling material choice, surface preparation, application precision, and curing processes, manufacturers can deliver outstanding performance with this modern gasket method.
Key Features:
- Material: Usually silicone, polyurethane, epoxy, or RTV (room-temperature vulcanizing) compounds.
- Application: Applied using automated dispensing systems or by hand, depending on the accuracy needed.
- Curing: Cures to form an elastic or semi-rigid seal. Some are moisture-cured, others heat-cured.
- Uses:
- Sealing housings or enclosures
- EMI shielding (for conductive FIPGs)
- Waterproofing electronic assemblies
Advantages:
- Custom fit for irregular surfaces
- Reduces need for mechanical fasteners or traditional gaskets
- Good chemical and temperature resistance
- Can reduce assembly time in mass production
Example Applications:
- Automotive engine control units (ECUs)
- Consumer electronics casings
- Industrial sensors
- LED lighting modules
✔️ Why It’s Widely Adopted:
- Automation-Friendly: Easily integrated into automated assembly lines.
- Highly Reliable: Once cured, it provides consistent sealing performance.
- Design Flexibility: Conforms to complex geometries, ideal where die-cut gaskets would struggle.
- Cost-Efficient: Reduces labor and inventory (no need to stock multiple gasket sizes).
- Environmental Resistance: Withstands chemicals, water, vibration, temperature extremes.
FIPG, CIPG, and CIPFG are all gasket technologies used for sealing components, especially in electronics, automotive, and industrial applications. Here's a clear breakdown of each:
✅ 1. FIPG — Form-In-Place Gasket
- Definition: A liquid or paste-like gasket material is dispensed directly onto the part and cures in place to form a seal.
- Material: Silicone, RTV, polyurethane, epoxy, etc.
- Curing: Can be moisture-cured, heat-cured, or UV-cured.
- Use Case: Permanent sealing; often used in engine parts, ECUs, or sealed electronics.
- Strength: Strong bond to both surfaces — not meant to be disassembled easily.
✅ 2. CIPG — Cured-In-Place Gasket
- Definition: Similar to FIPG in that it's dispensed as a liquid, but the key difference is that it only bonds to one side and allows disassembly.
- Material: Generally silicone-based, sometimes with foaming properties.
- Use Case: Electronics enclosures, LED lighting, where sealing is needed but with future access.
- Strength: Less aggressive adhesion than FIPG — can open and reclose housing.
✅ 3. CIPFG — Cured-In-Place Foam Gasket
- Definition: A foam version of CIPG; the material expands and cures into a compressible, foam-like gasket.
- Material: Two-component polyurethane or silicone foam.
- Use Case: High-end sealing with compression and resilience, such as automotive lighting, appliance doors, electrical cabinets.
- Strength: Offers soft compression, EMI shielding (if conductive), and excellent weather resistance.
🔍 Summary Table:
Term | Stands for | Re-openable? | Material Type | Typical Use |
FIPG | Form-In-Place Gasket | ❌ No | RTV/Silicone/Epoxy | Automotive engine parts, ECUs |
CIPG | Cured-In-Place Gasket | ✅ Yes | Silicone/RTV | Electronics, LED housings |
CIPFG | Cured-In-Place Foam Gasket | ✅ Yes | PU/Silicone Foam | Automotive lamps, electrical panels |
Factory add: No 39, Zhen an west road, Changan town , Dong guan city, China.