Why We Added Limit Switches to Sliders in Our Tooling Molds: A Real-World Lesson
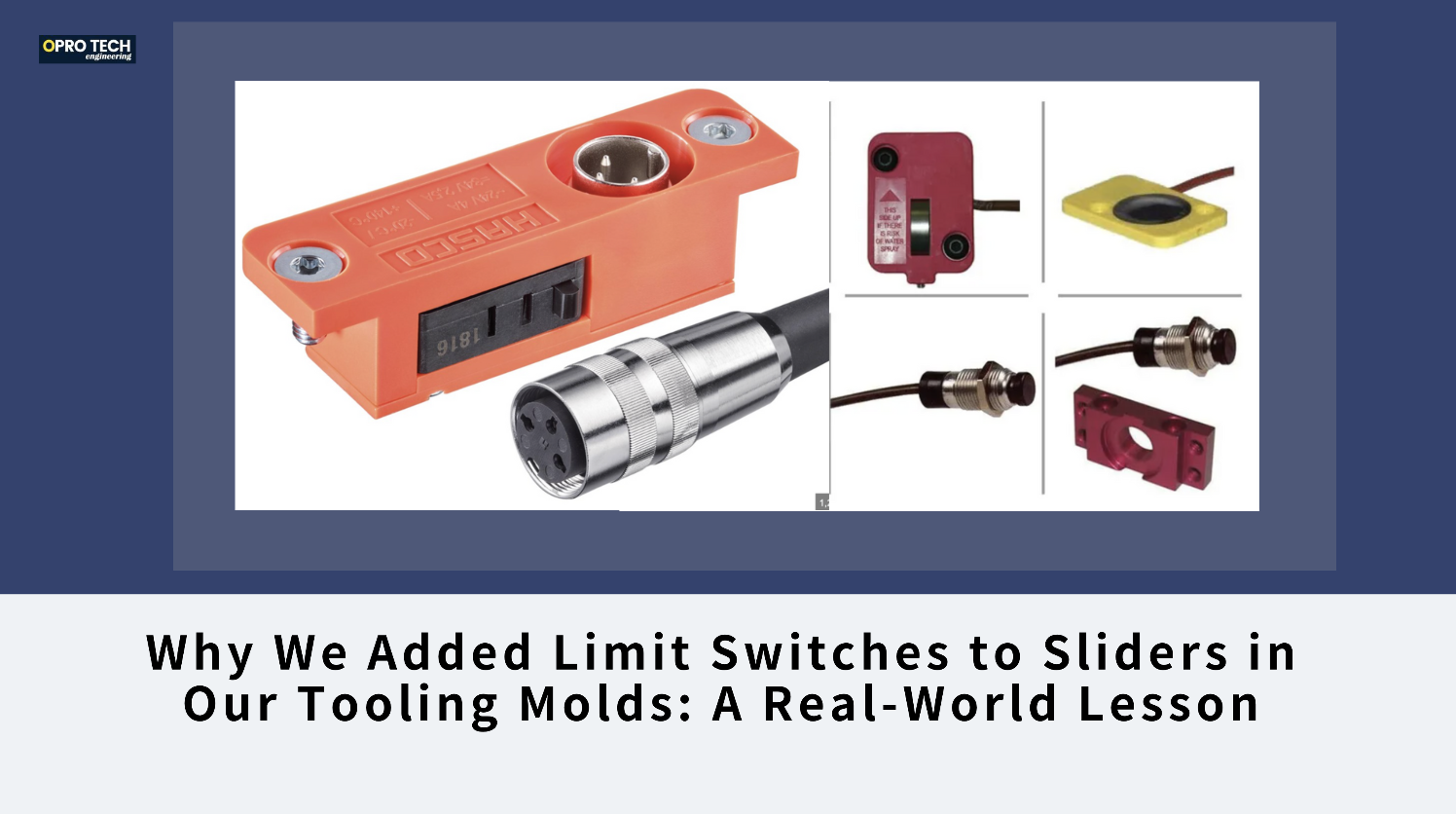
In the tooling and mold manufacturing industry, precision and safety are everything. Even small oversights can lead to costly mistakes — or even permanent damage to the mold. Today, we want to share a real-world experience from our team, and how it taught us an important lesson about the necessity of limit switches on mold sliders.
The Challenge: Relying Only on Manual Control
In one of our recent mold projects, the slider movement was controlled manually by the operator during the molding process. Without an automatic detection system in place, workers had to visually confirm that the slider had fully retracted before closing the mold.
Unfortunately, during production, a human mistake occurred: the slider did not retract completely, but the mold proceeded to close.
This led to serious consequences:
- Damage to the slider and slider guides
- Extended downtime for repairs
- Delays in customer delivery
- Increased maintenance costs
This incident clearly highlighted a vulnerability: relying solely on manual checking leaves room for error, even with skilled and attentive workers.
The Solution: Installing Limit Switches for Automatic Safety
Learning from this experience, we decided to integrate limit switches into our mold design to monitor slider positions.
A limit switch is a simple yet highly effective device:
- It detects the exact position of the slider (whether it is fully retracted or extended).
- It sends a signal to the injection molding machine controller.
- Only when the switch confirms the slider is safely retracted will the machine allow the mold to close.
- If the slider is not fully retracted, the machine stays open and can even trigger an alarm for operator intervention.
With this upgrade, the safety of the process no longer depends solely on human observation. The system itself provides protection, improving both process reliability and tooling life.
Technical Implementation
Depending on the mold requirements, different types of switches can be used:
- Mechanical limit switches with rollers or plungers
- Inductive proximity sensors for non-contact detection
- Reed switches for magnetic sensing
We worked closely with our engineering team and suppliers to select durable, high-precision limit switches suitable for the production environment.
Additionally, we designed the installation points carefully to ensure:
- The switch is triggered after the slider completes its full movement.
- The system is easy to maintain and replace when needed.
The Results: Safer, Smarter Production
Since adding the limit switches:
- No further slider-related damage has occurred.
- Operator workload and stress are reduced.
- Machine cycle times are more stable.
- Customer delivery schedules are better protected.
This experience taught us a valuable lesson:
Preventing mistakes by design is far better than fixing mistakes after they happen.
Our Commitment to Continuous Improvement
At Opro-tech engineering, we believe that every project offers an opportunity to learn and grow.
By sharing this case openly, we hope to:
- Help others in the industry avoid similar risks
- Demonstrate our dedication to safety, quality, and continuous improvement
- Build even stronger trust with our customers
We are committed to applying this standard to future molds, ensuring smarter designs and safer production for all our partners.
Factory add: No 39, Zhen an west road, Changan town , Dong guan city, China.