What are guide pins and guide bushings?
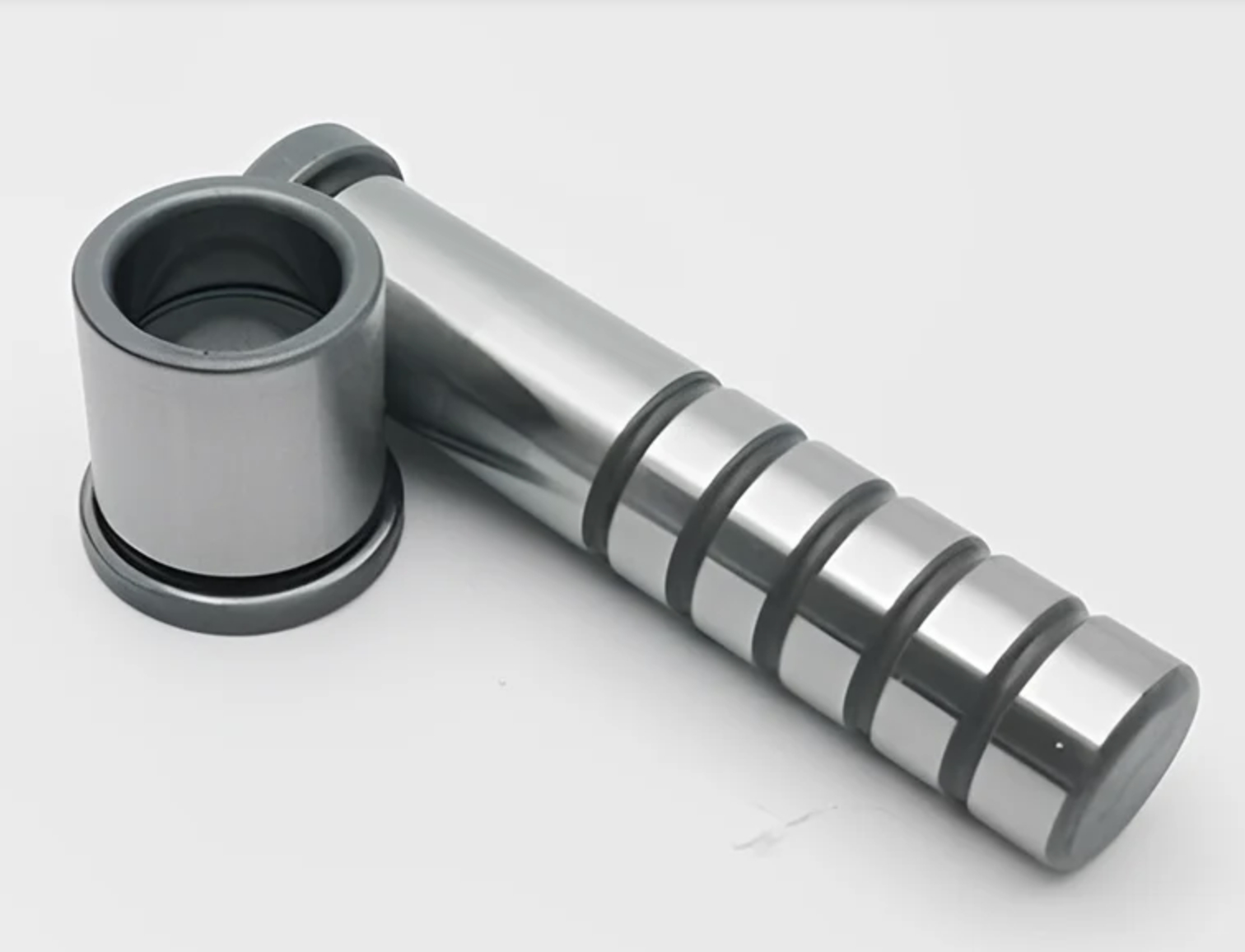
Understanding the intricate world of tooling molds can be both fascinating and challenging, especially for newcomers like me. Today, my exploration led me to the intriguing realm of guide pins and guide bushings.
In the vast landscape of engineering, each term, each component, carries its unique significance. Initially, it might seem like an unfamiliar language, but the more you delve into it, the clearer the picture becomes. Today's focus: guide pins and guide bushings.
Guide pins and guide bushings, seemingly modest in name, play pivotal roles in the intricate dance of a tooling mold. They are not just parts; they are purposeful components with specific functions. The fascinating journey of discovering their significance has opened my eyes to the meticulous design and engineering that goes into creating molds.
In the past, engineering felt like an enigma, a distant realm. But now, with each piece of the puzzle I uncover, the world of molds becomes more tangible and relatable. Guide pins ensure precise alignment, while guide bushings provide essential support, contributing to the flawless operation of the mold.
As I share my learning journey on the internet, my goal is twofold. Firstly, to inspire fellow enthusiasts who, like me, may have found the world of tooling molds initially daunting. Secondly, I hope to connect with individuals who share this passion or who might see potential business opportunities in my newfound knowledge.
Remember, every part in a tooling mold tells a story, has a purpose, and contributes to the intricate dance of manufacturing. The more we understand, the more we appreciate the beauty and precision in the world of engineering. Let's keep learning and sharing the wonders of tooling molds! 🛠️💡#ToolingMoldJourney #EngineeringDiscovery
Below some detailed information about guide pins and guide bushings for references.
In a tooling mold, guide pins and guide bushes play crucial roles in ensuring proper alignment and guiding of the mold components. Here's an overview of each:
Guide Pin:
Function: Guide pins, also known as leader pins or alignment pins, provide precise alignment between the two halves of the mold (core and cavity). They ensure that the mold components come together accurately during the closing phase.
Design: Typically cylindrical in shape, guide pins are installed in one half of the mold and fit into corresponding bushings or holes in the other half. They guide the movement of the mold halves and maintain proper alignment.
Guide Bush:
Function: Guide bushes, or bushings, are installed in the opposite mold half to the guide pins. They receive and guide the guide pins during the mold closing and opening processes, ensuring accurate alignment.
Design: Guide bushes are typically cylindrical sleeves with a hole through which the guide pin passes. They are often made of wear-resistant materials to withstand the repetitive movement and maintain accuracy over multiple molding cycles.
Working Together:
The guide pins and guide bushes work in tandem to ensure the precise mating of mold components. When the mold closes, the guide pins enter the guide bushes, providing alignment for the core and cavity. This alignment is crucial for maintaining the accuracy of the molded part's dimensions and preventing damage to the mold.
Proper maintenance and lubrication of guide pins and guide bushes are essential to ensure smooth operation and prolong the life of the mold. Regular inspection helps identify any wear or damage, allowing for timely replacement and preventing production issues.
The number of guide pins and guide bushes needed in a tooling mold can vary depending on the design and complexity of the mold. Here are some general considerations:
Single Cavity Mold:
For a simple single-cavity mold, a minimum of two guide pins and two guide bushes is common—one set for each mold half. This ensures proper alignment and stability during the molding process.
Multiple Cavity Mold:
In molds with multiple cavities, the number of guide pins and guide bushes may increase. Each cavity may require its own set of guide pins and guide bushes to ensure independent alignment for each part.
Complex Molds:
For complex molds with intricate shapes or side actions, additional guide pins and guide bushes may be necessary to control various movable components within the mold.
Size and Configuration:
The size and configuration of the mold also influence the number of guide pins and guide bushes. Larger molds or those with unconventional shapes may require more guide pin sets to maintain stability.
Application-Specific Requirements:
Certain molding applications may have specific requirements for guide pin and bushing placement based on the part geometry, tolerances, and production considerations.
It's essential to refer to the mold design specifications and consult with mold designers or engineers to determine the exact number and placement of guide pins and guide bushes for a particular mold. The goal is to achieve optimal alignment and stability to ensure accurate and consistent molding results.
Both the material and dimensions of guide pins and guide bushings play crucial roles in the performance and properties of these components within a tooling mold.
Material Selection:
Wear Resistance:
The material must exhibit high wear resistance since guide pins and guide bushings are subject to repetitive sliding and contact during the opening and closing of the mold. Materials like hardened steel or materials with coatings to enhance wear resistance are common choices.
Heat Resistance:
In applications involving high temperatures, such as injection molding of certain plastics, the guide pin and guide bushing materials must have good heat resistance to maintain their mechanical properties.
Corrosion Resistance:
For molds used in environments where corrosion is a concern (e.g., when molding corrosive plastics), corrosion-resistant materials or coatings may be selected to ensure longevity.
Dimensional Accuracy:
Tolerance and Fit:
The dimensions of guide pins and guide bushings must be precisely controlled to achieve the desired tolerance and fit. A tight tolerance ensures accurate alignment, reducing the risk of misalignment or premature wear.
Clearance and Lubrication:
The dimensional specifications also consider the clearance between the guide pin and guide bushing. Proper clearance, along with the use of lubrication, helps reduce friction, wear, and heat generation during the molding process.
Other Considerations:
Load-Bearing Capacity:
The material's strength and hardness are crucial for withstanding the loads and pressures exerted on guide pins and guide bushings during mold operation.
Surface Finish:
A smooth surface finish is desirable to minimize friction and prevent galling. Proper surface treatments or coatings may be applied to enhance the surface quality.
Compatibility with Mold Material:
The material compatibility with other mold components, such as the mold base or core, is essential to prevent galvanic corrosion or material interaction issues.
In summary, selecting the right materials and ensuring precise dimensional control are critical for the effective functioning of guide pins and guide bushings.
These considerations contribute to the longevity, reliability, and overall performance of the tooling mold.
Thanks for your reading, for any subjects you’d like to discuss please send email to danny@opro-tech.com.