TIG Welding: The Art of Precision Welding
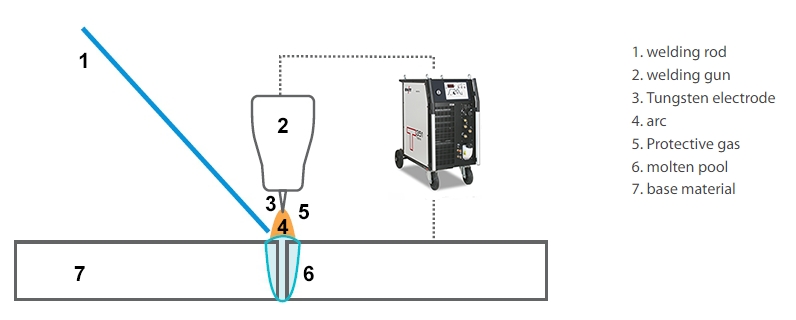
TIG welding(Tungsten Inert Gas welding) is renowned for its high-precision welding technology, delivering high-quality welds on various metal materials. This script explores the fundamental principles of TIG welding, its applications, and its significance in contemporary manufacturing.
Working Principles: TIG welding involves a non-consumable tungsten electrode that melts the workpiece and filler material through a high-temperature arc. Argon gas acts as a shielding gas, protecting the molten metal from air contamination. This process requires skilled expertise and meticulous control to ensure excellent welding results.
Equipment and Materials:
Shielding Gas: Inert gases such as argon envelop the welding area, preventing oxygen and impurities from entering.
Filler Materials: The choice of filler material depends on the type of metal and specific welding requirements.
Welding Steps:
Preparation: Thoroughly clean and prepare the metal surface, ensuring it is free from oil and dirt.
Equipment Setup: Adjust current, voltage, and gas flow to meet welding specifications.
Arc Initiation: Trigger the arc through high-frequency arc initiation or contact start to begin welding.
Metal Fusion: Melt the metal through the high-temperature arc, introducing filler material.
Control Weld Seam: Precisely control welding speed and torch movement to achieve a uniform weld seam.
Applications: TIG welding finds widespread use in industries demanding exceptionally high welding quality, including:
Aerospace Industry: Manufacturing and repairing components for aircraft and spacecraft.
Stainless Steel Welding: Creating high-quality, visually appealing stainless steel welds.
Precision Instrument Manufacturing: Industries with strict requirements for welding precision and quality.
Advantages and Challenges:
Advantages: High welding quality, strong metal versatility, precise control of weld area.
Challenges: High technical requirements, relatively slower speed.
TIG welding plays a pivotal role in contemporary manufacturing, offering a high-precision welding process and outstanding welding quality. It is suitable for various metals, providing a reliable solution for manufacturing precision components and achieving top-notch welding effects.