CASE STUDY: learning curves in CNC Production-quality issues and experiences
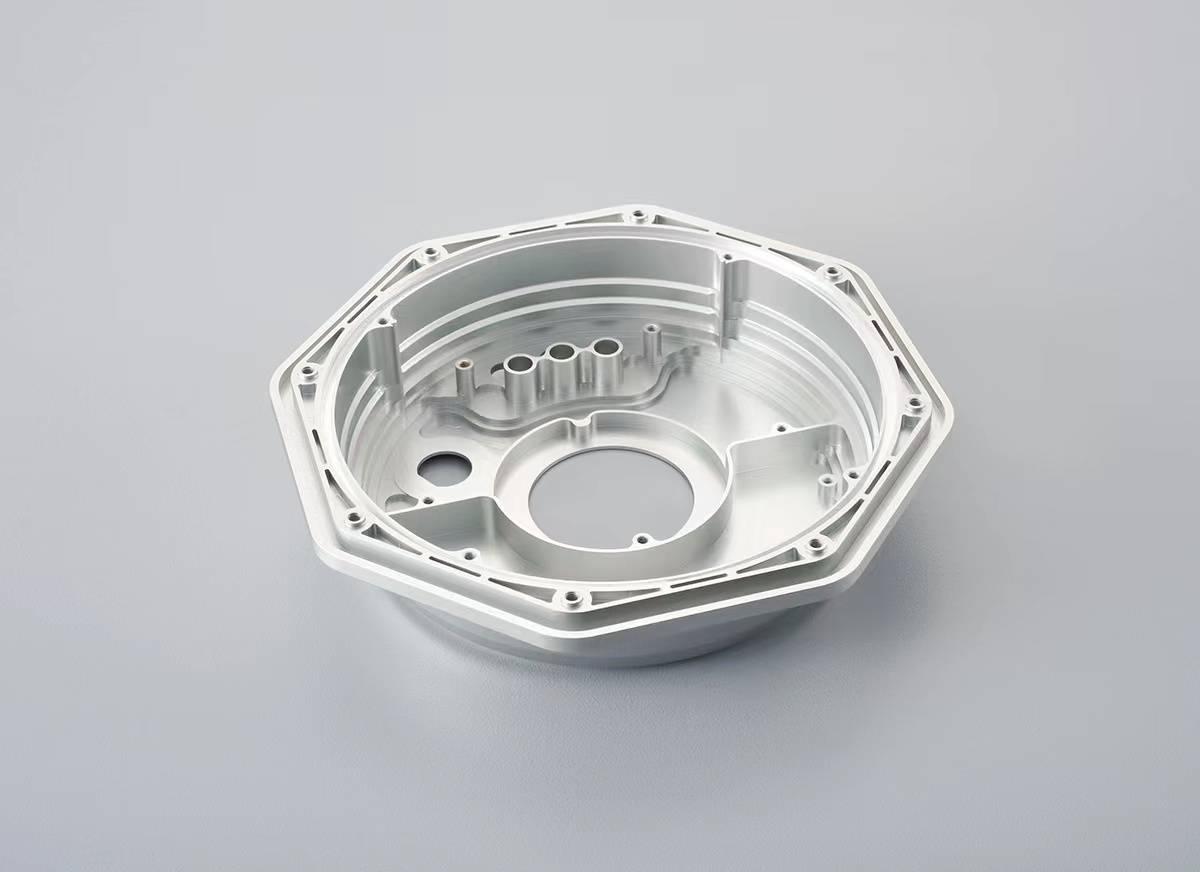
"Dear Danny,
Just wanted to extend a big thank you for your professional and kind cooperation.
Fingers crossed everything goes smoothly this time, closing the case for both of us on a positive note.
Best Regards."
As a supplier, we are always grateful for the slight encouragement from our customers and use it to motivate our team to work even harder and continuously improve the work we are doing.
We, Opro-tech, established a partnership with this German customer in July 2023.
Up until the end of last year, a total of 140 different products have been produced, with a combined quantity of 10,853 pieces.
The main materials for these products include stainless steel, brass, and plastic, with surface treatments such as electroplating and polishing.
These products are utilized in industries such as automotive, electronics, robotics, etc.
Currently, our cooperation is very smooth.
However, at the beginning, we received two or three quality complaints from the customer.
The main quality issues were as follows:
- Dimensional tolerances did not meet the specified requirements.
- The surface finish did not meet the specified standards.
For CNC metal products, some common issues include dimensional deviations, surface quality, angular errors, threading problems, foreign objects and residues, hardness, processes, materials, etc.
When we talk about German quality, it is essential to mention the German industrial standard DIN.
In terms of product specifications, testing methods, safety requirements, design guidelines, and usage scenarios, detailed and professional communication with customers is necessary to match the requirements of both customers and end-users.
As a supplier, here is how we address the aforementioned two issues:
1, For dimensional issues, we have implemented a training program to enhance the quality awareness of our staff.
We had comprehensive training across various stages, including production, quality control, and shipping.
Before production, we hold meetings to discuss the manufacturing process, meticulously confirm customer requirements, and fully leverage a craftsmanship approach:
- Take it slow: Carefully review the technical requirements in the drawings, prepare the necessary tools, knives, and measuring instruments, and verify the raw material dimensions.
- Stay steady: Maintain stability during the machining process by understanding the key elements of the components, securely and correctly clamping the parts, and adhering to standardized and cautious operations.
- Precision matters: Exercise precise control over the production process, carefully observe the manufacturing flow, conduct self-checks and rechecks on component dimensions, and perform multiple iterations until precision is achieved.
- Be accurate: Ensure accuracy in every step of the process, strictly adhere to standard procedures, and guarantee zero product defects.
2, We realized that when it comes to measuring the dimensions of cylindrical objects with higher precision, using calipers may not be the best approach.
We've purchased 4 sets of micrometers without hesitation.
On the other hand, for more stringent dimensional requirements, we use CMM (Coordinate Measuring Machine) for inspection.
CMM inspection refers to the process of using a three-coordinate measuring machine (CMM) for measurement and testing.
CMM is a high-precision measuring device typically used to measure the three-dimensional geometry and position of objects, ensuring their compliance with design specifications.
3. Additionally, we have acquired a surface finish testing instrument, which offers a more precise assessment of surface smoothness compared to the previous method of visual inspection.
So we promptly took action and procured a German-made Mahr portable roughness tester, aiming to align with the customer's preferred measurement methods and techniques.
Features of the Pocket Surf portable roughness gauge:
- Optional selection of one parameter from any of the four: Ra, Rmax/Ry, Rz, accomplished by toggling the switch.
- Choice of measuring parameters 1, 3, or 5, with an assessment length of 0.8mm/.030in.
- Operational in any position - horizontal, vertical, or inverted.
- The measuring head can be switched to four positions - axial (closed), 90°, 180°, or 270°.
- Capable of easily measuring even hard-to-reach areas such as inner and outer diameters.
- Complete data output, suitable for connection to various SPC (Statistical Process Control) data processing systems.
At Opro-tech, we have a long-standing commitment to delivering highly precise products to our clients, with product accuracy tolerances ranging from 0.01mm to 0.001mm.
Our product portfolio spans various industries, including Aerospace, Robotics, Automotive, IoT (Internet of Things), Medical Technology, Special Mechanical Engineering, Energy, Agricultural Equipment, etc.
Our manufacturing capabilities cover a wide range of processes, including Turning, Milling, Sheet Metal Fabrication, Laser Cutting, Bending, Injection Molding, Die-Casting, and 3D Printing.
As a sales team, how can we effectively coordinate and facilitate precise communication between customers and the factory workshop?
As a sales team, our role is to effectively coordinate and communicate information between customers and the factory workshop to ensure precise conveyance.
Being at the forefront of sales, we must establish clear communication with the technical personnel in the factory workshop.
This is because we have a better understanding of our customers' needs compared to them.
For instance, sometimes the details required by a customer can be up to 80% more intricate than those of other clients, occasionally even delving into specifics such as the lifespan of a screw.
When conveying customer order information and quality standards to the factory workshop personnel, it is crucial to explicitly inform them about the customer's specified quality grade range.
We aim to accurately transmit all details, requirements, and feedback obtained from customer communication to the factory workshop.
This approach is intended to reduce the adjustment period with customers, enabling us to respond quickly and make necessary revisions.
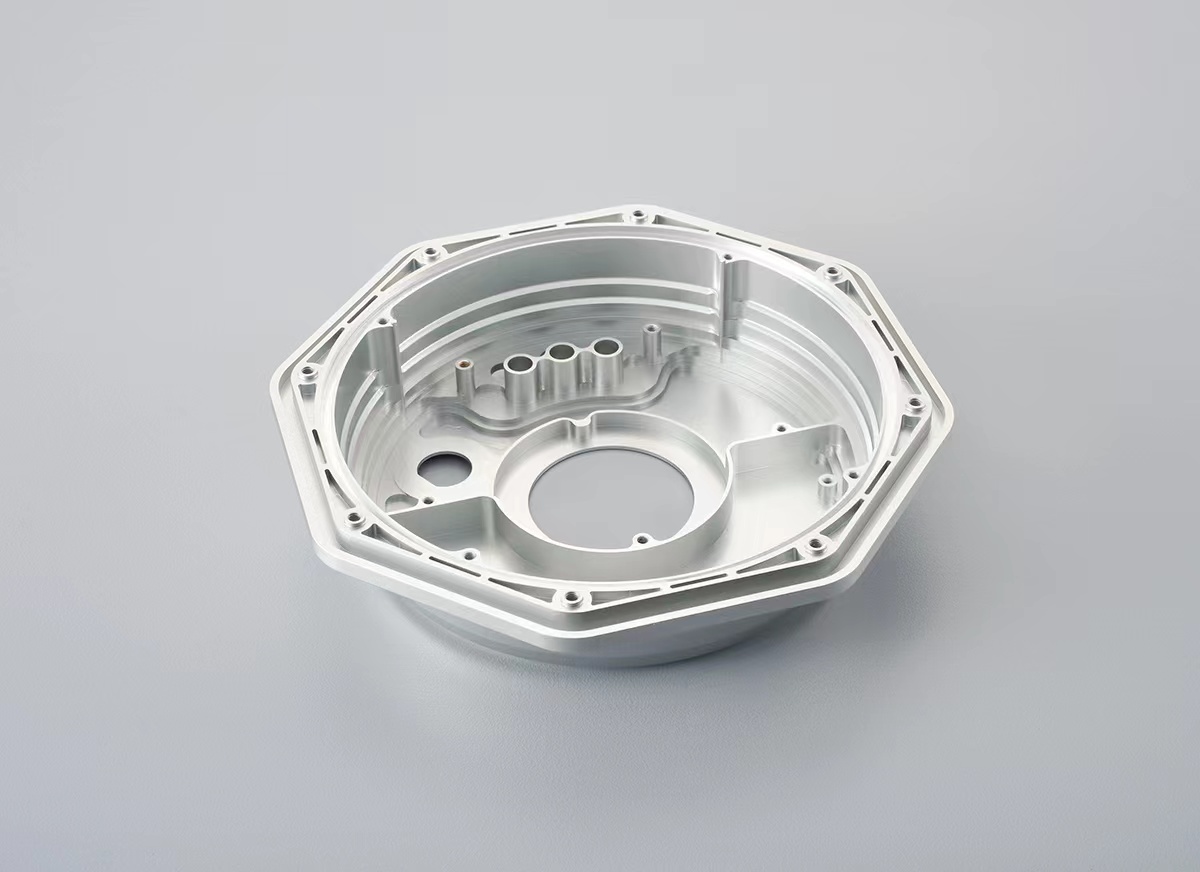
Through this case, we have achieved the following objectives:
- On the factory side:
- The product quality has been improved to 98%, and we are currently striving to reach 100%.
- The overall quality awareness among all employees is stronger than ever, with the team promptly cooperating to take measures whenever a quality issue arises.
- We have enhanced the professionalism of the sales team, focusing on precise and expert communication to provide reliable services, earning positive feedback from customers, and establishing long-term cooperative relationships.
- As a professional manufacturer, we integrate production, research and development, quality control, and after-sales service to ensure control at every stage.
2. On the customer side:
- Through communication with this customer, we have provided highly competitive prices, saving the customer 20% in costs.
- We have assisted the customer in expanding into more product categories, helping them gain a larger market share.
We take pride in offering competitive pricing without compromising on quality.
What sets us apart is not just our state-of-the-art machining capabilities but also our commitment to clear and professional communication.
Thanks for taking the time and read through this case study.