Reduce the cost of CNC machining and manufacturing.
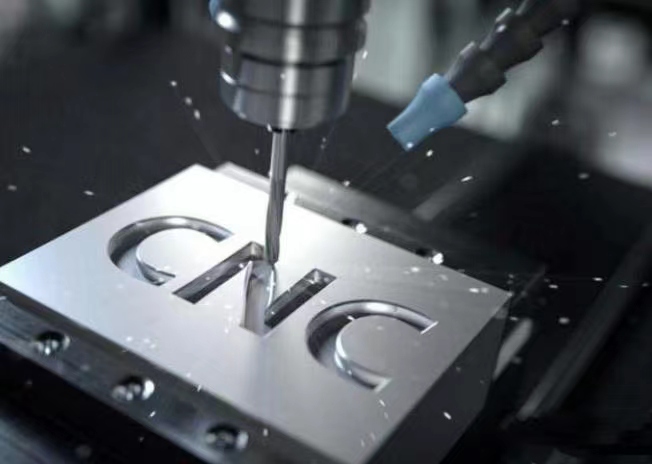
Yesterday I mentioned what factors cause CNC processing costs to be relatively high. Today I will share with you how to save CNC processing costs?
Reducing CNC manufacturing costs is one of the challenges often faced in the manufacturing industry. Because there are many choices now, such as 3D printing. In contrast, CNC processing reduces materials, while 3D printing increases materials. Many people are willing to choose 3D printing technology to produce their own products.
So how can we reduce the cost of CNC machining?
Material optimization: Choosing appropriate materials must not only meet the functional requirements of the product, but also consider cost. Sometimes costs can be reduced by choosing alternative materials that are affordable but perform adequately.
Reduce material waste: Optimize design to reduce scrap and material waste. Maximize raw material utilization by redesigning parts to use smaller raw material sizes or reducing scrap by optimizing cutting paths.
Machining time optimization: Optimize machining paths, cutting speeds and cutting depths to reduce machining time. Efficient cutting paths and process planning can reduce mechanical wear, energy consumption, and improve production efficiency.
Mass production: Increasing production quantity can spread fixed costs, such as equipment maintenance, tool usage, and labor costs, because the CAD design of products in batches is the same, thereby reducing the manufacturing cost of each part.
Outsourcing vs. in-house production
When weighing your options for reducing CNC machining costs, the decision between outsourcing and in-house production is critical. Opting for in-house production requires significant investments in purchasing CNC machine tools and hiring or training skilled operators, resulting in significant upfront and ongoing expenses. In contrast, outsourcing to specialized manufacturers shifts the burden of equipment and labor costs to the service provider. You pay primarily for the services provided, not for the maintenance of the machines or labor. Yes, so the choice is still up to you.
Design optimization: Reduce complexity through reasonable design and simplify part structure to reduce manufacturing difficulty. Reduce parts that require multiple operations or complex equipment.
If you have any projects, please feel free to contact us.We specialize in precision hardware and CNC machining parts for a wide range of materials, including but not limited to tungsten steel, imported materials like SKD11 and SKD61, various stainless steel grades such as SUS303, SUS304, SUS316, SUS316L, as well as A5052, AL6061, AL6063, AL7075, LY12, 65Mn, Cr12, 40CrMo, 45#, Q275, ST12.03, SS2331, SS1994-04, AISI12L14, Y15, bakelite, POM, steel, nylon, teflon, and acrylic, among others.
Additionally, we offer a comprehensive range of surface treatments, including anodizing, chrome plating, nickel plating, zinc plating (black zinc), blackening, electropolishing, passivation, titanium plating, powder coating, and electrophoresis. Our heat treatment capabilities encompass processes such as vacuum quenching, salt bath nitriding, nitriding, carburizing, carbonitriding, high-frequency firing, carbon immersion firing, quenching and tempering, and more.