What are stripper plates, stripper bars and stripper rings?
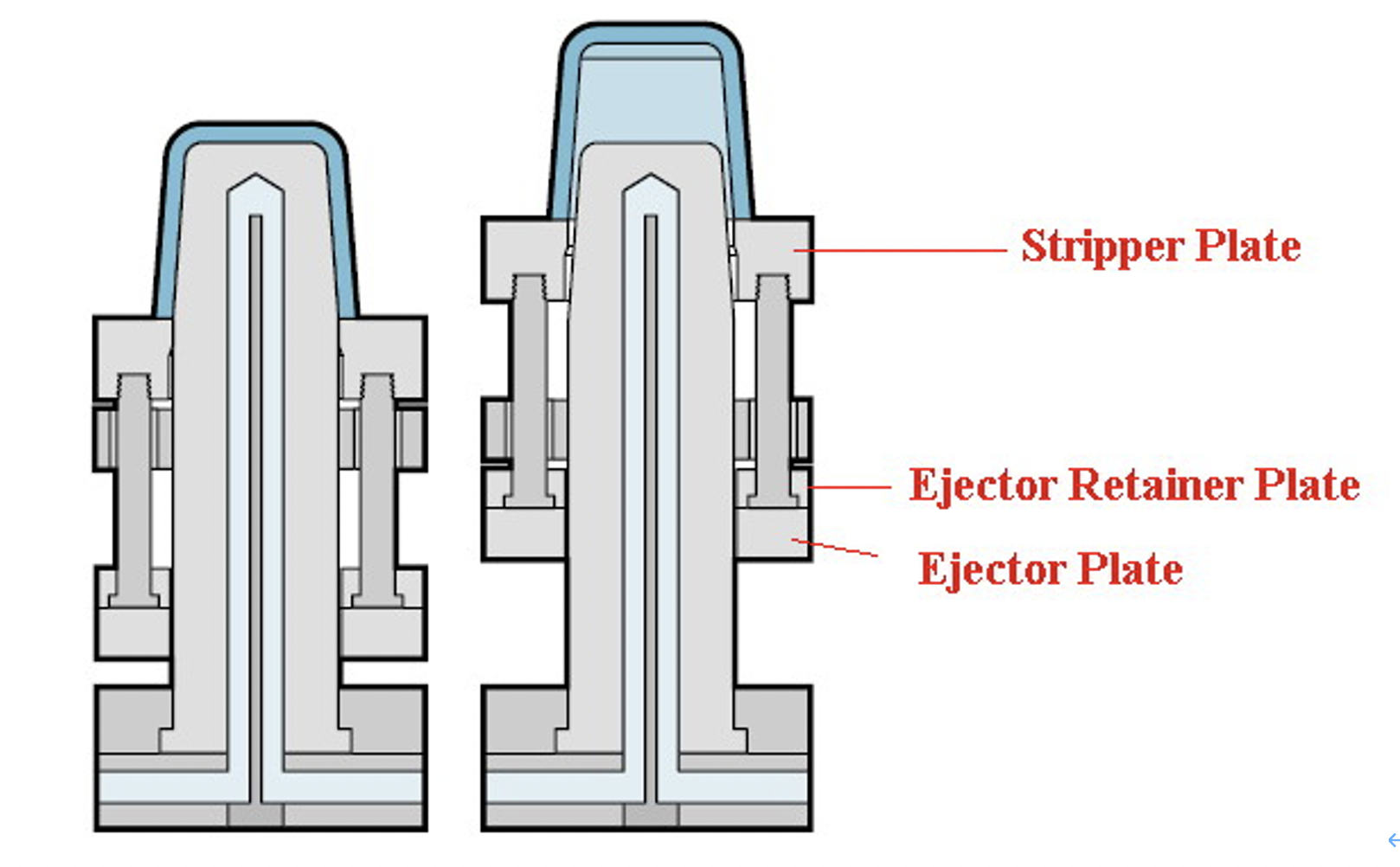
๐งโโ๏ธ ๐งโโ๏ธ Diving into the fascinating world of tooling molds, today's learning spotlight is on stripper platesโa critical component shaping the precision of mold ejection.
๐ In a tooling mold, the terms "Stripper Plate," "Stripper Ring," and "Stripper Bar" refer to components designed to assist in the ejection of molded parts from the mold cavity. ๐ Here's an explanation of each:
๐ฃ #StripperPlate:
A Stripper Plate is a flat plate that is mounted parallel to the mold opening and closing direction.
๐ก It is located above the mold cavity and is designed to push the molded part off the core pins during the ejection phase.
The Stripper Plate typically moves vertically or horizontally, aiding in the release of the molded part.
๐ฃ #StripperRing:
A Stripper Ring is a circular component that surrounds the core pins in the mold.
๐ Similar to the Stripper Plate, its purpose is to help eject the molded part by pushing it off the core pins.
The Stripper Ring can have a slightly tapered or beveled edge to facilitate part ejection.
๐ฃ #StripperBar:
A Stripper Bar is a bar-shaped component used in mold design to assist in part ejection.
๐ It may be mounted horizontally or vertically within the mold and is positioned to contact the molded part during ejection.
The Stripper Bar moves to push the part out of the mold cavity, working in conjunction with other ejection components.
The primary difference lies in their shapes and configurations: the Stripper Plate is a flat plate, the Stripper Ring is circular, and the Stripper Bar is bar-shaped.
The Stripper Plate and Stripper Ring are often used in molds with complex geometries or multiple core pins, while the Stripper Bar is a simpler component that can be effective in certain mold designs.
Each component contributes to the ejection process, but the choice of which to use depends on the mold design, part geometry, and specific ejection requirements.
In summary, Stripper Plate, Stripper Ring, and Stripper Bar are components integrated into tooling molds to facilitate the efficient and reliable ejection of molded parts from the mold cavity. They play a crucial role in the overall mold design and manufacturing process.
1. Unraveling Complexity:
- Stripper plates are the unsung heroes in molds with intricate part geometries or challenging undercuts. Their flat surfaces seamlessly navigate through complexities that might stump conventional ejector pins.
2. Tackling Undercuts and Side Actions:
- When undercuts or side actions come into play, stripper plates step up to the plate. Their versatile design, often mirroring the part geometry, makes them the go-to choice for pushing out those complex shapes.
3. Part Preservation:
- Delicate parts with thin walls? Fear not! Stripper plates gracefully glide into action, minimizing the risk of distortion or damage during ejection, ensuring your creations emerge unscathed.
4. The Flatter, the Better:
- Large, flat surfaces pose no challenge. Stripper plates provide uniform support, reducing the likelihood of warping or bending, ensuring your parts maintain their pristine form.
5. Smoothing the Way:
- Looking for that impeccable surface finish? Stripper plates contribute to a smoother ejection process, adding that final touch to your molded masterpiece.
In the intricate dance of mold design, stripper plates play a key role in ensuring flawless demolding. Stay tuned for more insights into the fascinating realm of tooling molds! ๐ก๐
#ToolingMolds #ManufacturingMagic #StrippingInsights