Can CNC directly process high-gloss mirror surfaces?
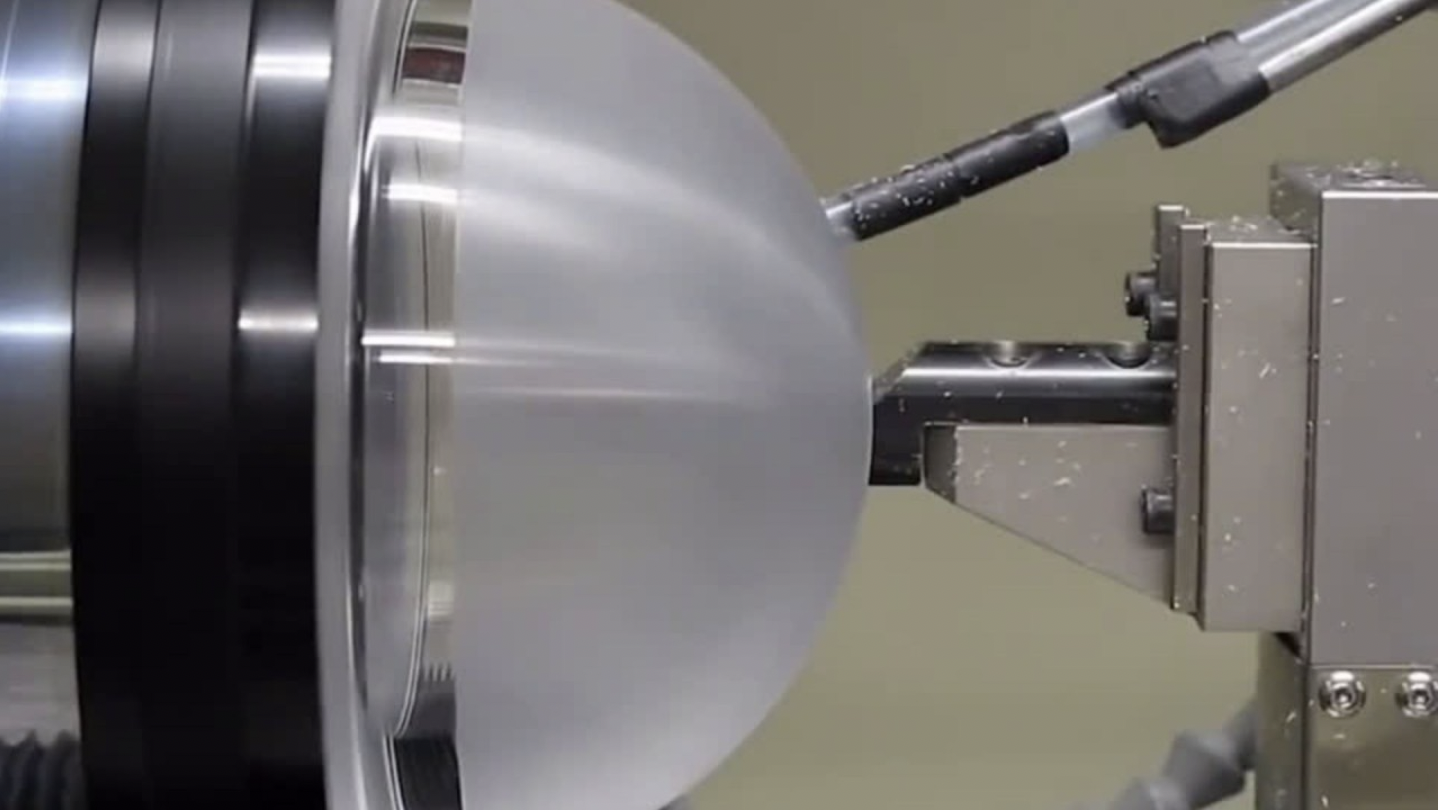
Currently, the CNC high-gloss processing technology (milling, turning) is not well-known among technicians in most industrial sectors.
Practical experience shows that only a few production enterprises truly master this technology.
In recent years, with the development of high-performance, high-precision CNC machines and the emergence of excellent metal cutting tools, there has been a significant breakthrough in CNC high-gloss processing.
Milling (turning) has become possible and has become a goal pursued by successive players in the machining industry.
The principle of CNC high-gloss processing is to use special dedicated tools on precision CNC machining equipment, combined with scientifically reasonable cutting parameters and processes to achieve a sparkling processing surface effect.
Machine Tool:
The use of precision CNC machines is a prerequisite for high-gloss processing. The machine tool needs to have good rigidity and accuracy, such as a precision CNC engraving machine (generally with a speed of 20,000 rpm per minute).
Cutting Tool Selection:
Use high-precision, high-quality tools.
Tool selection has a significant impact on surface quality. Hard alloy and single-crystal diamond tools are usually used for mirror-level processing.
The achievement of high-gloss effects is attributed to the use of diamond tools. Diamond tools are the standard configuration in the CNC high-gloss processing industry.
A good diamond tool edge cannot be seen with any burrs under a high-power microscope. The edge can withstand long-term cutting without changing. Diamond has a very low friction coefficient with non-ferrous metals, and chips are not easy to stick to the blade, avoiding chip lumps.
Therefore, the cutting edge always maintains direct cutting on the workpiece during the processing, ensuring brightness.
The cutting edge of high-gloss milling tools is wide, with a small front angle or negative front angle, and an angle close to zero degrees.
When high-gloss milling, the tool performs high-speed cutting on one hand, and on the other hand, due to the small front angle of the tool, the cutting edge of the tool forms a scraping and squeezing effect on the processed surface, achieving high smoothness of the workpiece surface and producing a hardened layer, improving the surface hardness and wear resistance of the workpiece.
The geometric shape of the tool depends not only on the geometry of the workpiece but also on the physical properties of the workpiece material.
When processing plastic materials such as copper, aluminum, and nickel, the front angle of the tool is 0°, and the rear angle is generally between 5° and 10°.
The radius of the tooltip is usually 0.5 to 5 mm.
When processing brittle materials such as silicon, germanium, CaF2, and ZnS, the front angle of the tool is generally selected between -15° and -45°. The optimal front angle depends not only on the material itself but also on the stiffness of the machine tool and clamping system, and it is best determined through production tests.
High-gloss milling uses disc milling cutters.
The diameter of the cutter disk should be selected as large as possible, with good rigidity and precise blade positioning accuracy. The size of the cutter disk will change the patterns and effects on the milled surface. The number of blades can be single or multiple, but using multiple blades makes it difficult to adjust the consistency of each blade, and it is time-consuming. The use of a single-blade milling cutter achieves better results.
Although diamond tools may seem expensive with a large initial investment, natural diamonds have extremely high hardness and are very wear-resistant.
According to statistics, the lifespan of a diamond-cutting tool is 25 times that of a high-speed steel-cutting tool, and each diamond tool can be around 6 to 15 times.
Therefore, the cost of each part tool is negligible, and stable dimensions and high brightness can be achieved.
Workpiece:
Materials suitable for high-gloss processing include aluminum, copper, stainless steel, etc.
When processing aluminum, it has the highest brightness and minimal wear on the tool.
When processing copper, it has relatively high brightness and moderate tool wear.
When processing stainless steel, the brightness is dull gray, and tool wear is relatively high.
Process Stability:
Ensure the stability of the entire processing process. Avoid vibrations, resonances, and other factors that may lead to processing instability.
The cutting speed of mirror milling is usually around 30 m/s.
To produce perfect workpieces, the spindle must be dynamically balanced after tool change to minimize the ripple effect caused by imbalance on the workpiece surface.
Diamond tools have good heat conduction performance and low cutting volume, so there is no need for coolant.
On the contrary, adding coolant not only increases the cleaning trouble after processing but also, coolant with iron filings can often become the cause of blade chipping.
The defect of high gloss is that it requires high and stable requirements for the outer contour of the product; otherwise, unevenness (such as size edges) may occur after high gloss.
To obtain safety technical data that includes all relevant factors, such as tools, materials, and processing technology, and to make it the best combination, often requires an experienced trial-and-error process.
Application:
High-gloss aluminum sheets are widely used in the outer shells of digital products, and they can also undergo secondary oxidation after high-gloss processing to enhance the wear resistance of the high-gloss area.
High-gloss stainless steel is also beginning to be used in some high-end digital cameras and smartphones.