Over-Molding Technology
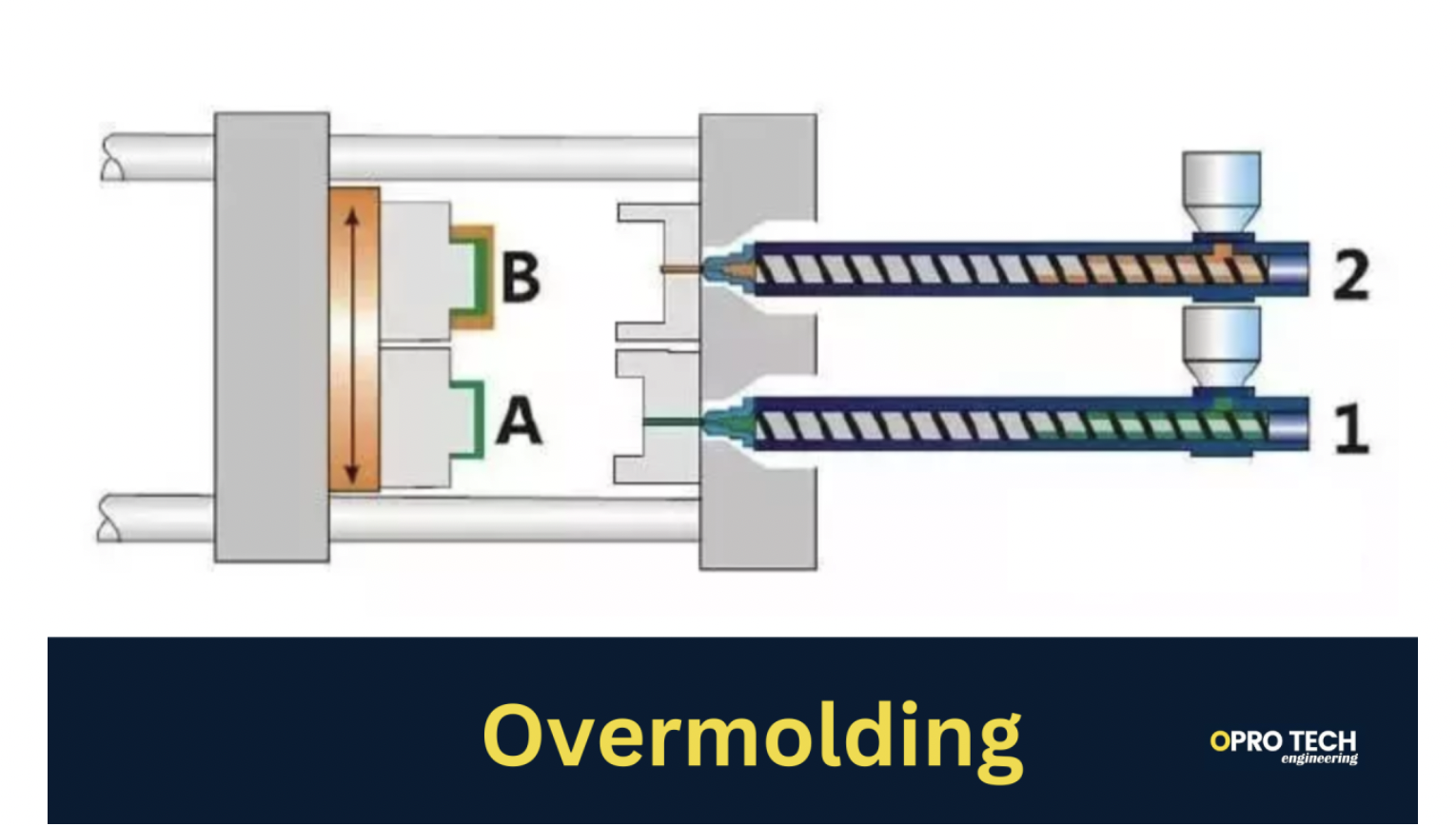
Dual-color injection molding typically refers to the molding of two colors that are different or of different types of plastics.
Due to the separate injection units and nozzles of dual-color machines, the resulting products often have distinct dual colors, without being mixed.
Over-molding can reduce assembly and post-processing work for molded parts, saving costs, enhancing the aesthetic visual effects of products, and increasing their added value.
The biggest difference between dual-color injection molding machines and general injection molding machines lies in the design of the injection unit's movable template.
Generally, dual-color machines have two sets of independently separated injection units, while typical injection machines have only one set.
The configuration of the two sets of injection units varies according to the design of each manufacturer.
As for the design of the movable template, it must provide a rotating mechanism.
Common designs include adding a turntable or a rotating shaft mechanism to provide a 180-degree reciprocating rotation function, enabling the mold to produce cyclic alternating movements. Some special dual-color molds do not require a turntable or rotating shaft mechanism but instead, use sliding alternation or horizontal rotation by the mold itself.
Characteristics of Dual-color Production Process
- Dual-color injection molding machines consist of two sets of structurally and speculatively identical plasticizing injection devices. The nozzles should have a special structure according to the production requirements or be equipped with a structure that can rotate and switch positions. During plasticization and injection, it is required that the process parameters such as melt temperature, injection pressure, and melt volume of the two sets of plasticizing injection devices are the same, and the fluctuations in process parameters between the two sets of devices should be minimized.
- Compared with ordinary injection-molded plastic products, dual-color injection-molded plastic products require higher parameters for melt temperature and injection pressure during injection. The main reason is that in dual-color injection molding, the mold runner is longer, the structure is more complex, and there is greater resistance to the flow of injection melt.
- Dual-color injection-molded plastic products should use materials with good thermal stability and low melt viscosity to avoid decomposition due to high melt temperatures and long residence times in the runner. The most commonly used plastics are polyolefin resins, polystyrene, ABS materials, etc.
- During the injection molding of dual-color plastic products, to ensure that the melts of two different colors can be well fused in the mold and ensure the molding quality of the injection molded products, higher melt temperatures, higher mold temperatures, higher injection pressures, and injection rates should be used.
Over-molding Structure
- Traditional over-molding has two forms: "core shift" and "core rotation."
- Insert molding: Two plastic materials may not be injected on the same injection molding machine. They are molded in two stages. After the product is demolded from one set of molds, it is then placed into another set of molds for the second injection molding. Therefore, this molding process is usually completed by two sets of molds, and there is no need for a special dual-color injection molding machine. The mold structure is the same as that of single-color injection molding molds, mainly relying on adjusting the flow rate of injection parameters to control the fusion points of the two materials.
Processing of Over-Molds
- Mold cavity processing: To ensure the accuracy of the center positioning after the male and female molds rotate 180 degrees and the accuracy of the size of the inserts and the slope of the mating broken surfaces, the opening of the mold cavity should be corrected parallel to the GP hole of the reference edge, and the data should be taken from the GP hole of the reference angle.
- Core precision: To ensure the interchangeability of the male and female molds alternately, the dimensional tolerance of the core should be within ±0.01mm, especially the slope of the inserts and the mating broken surfaces.
- Mold structure: To ensure the smooth operation of the mold structure during trial molding or production, the assembled mold must be tested for the smoothness of the structure's action to avoid damage during trial molding or production.
- Mold assembly:1) Remove all mold locking screws before assembling the mold.2) First, assemble one set of side molds on side B without adjusting the mold to avoid uneven force on the fixed side and the rotating disk, which may damage the machine.3) After installing all the locking screws manually, tighten the screws.4) After the mold opens, assemble the second set of side molds on side A. Tighten all the locking screws by hand, but do not tighten them.5) Rotate the male and female molds 180 degrees.6) Use the tightened screws on side B to align the male mold on side A. Tighten the screws of the male mold on side B and the female mold on side A.7) After both sets of molds are assembled, proceed with mold adjustment.
Applications of Overmolding
The injection over-molding process is compatible with a wide variety of materials, ranging from plastics to metals.
This process helps produce custom prototypes and production parts for various applications depending on your requirements.
Several industries find valuable uses for over-molding services.
Surgical Instruments
Overmolding meets the precision and safety requirements of the medical industry. The ability to combine plastics and metal materials ensures the efficient creation of surgical devices, equipment housing, catheters, syringes, and more.
Electrical Applications
Using thermoplastic elastomer as an overmold material makes the process useful for electrical components. Custom-made over-molded parts, like electrical outlet covers, gaskets, etc., are made to withstand harsh conditions, making them last longer.
Hardware Tools
The functional advantages of over-molding make it an outstanding process for making pliers, screwdrivers, hammers, wrenches, pocket knives, and more. The process improves the grip of these tools, making their application more efficient.
Household Items
The over-molding technique generally improves functional performance like grip, cleanliness, and ease of use. It also enhances vibration dampening, chemical resistance, and more. This makes them useful for household items like kitchen utensils, toothbrushes, pens, shampoo bottles, etc.