Causes and Solutions for Difficult Mold Release in Injection Molding
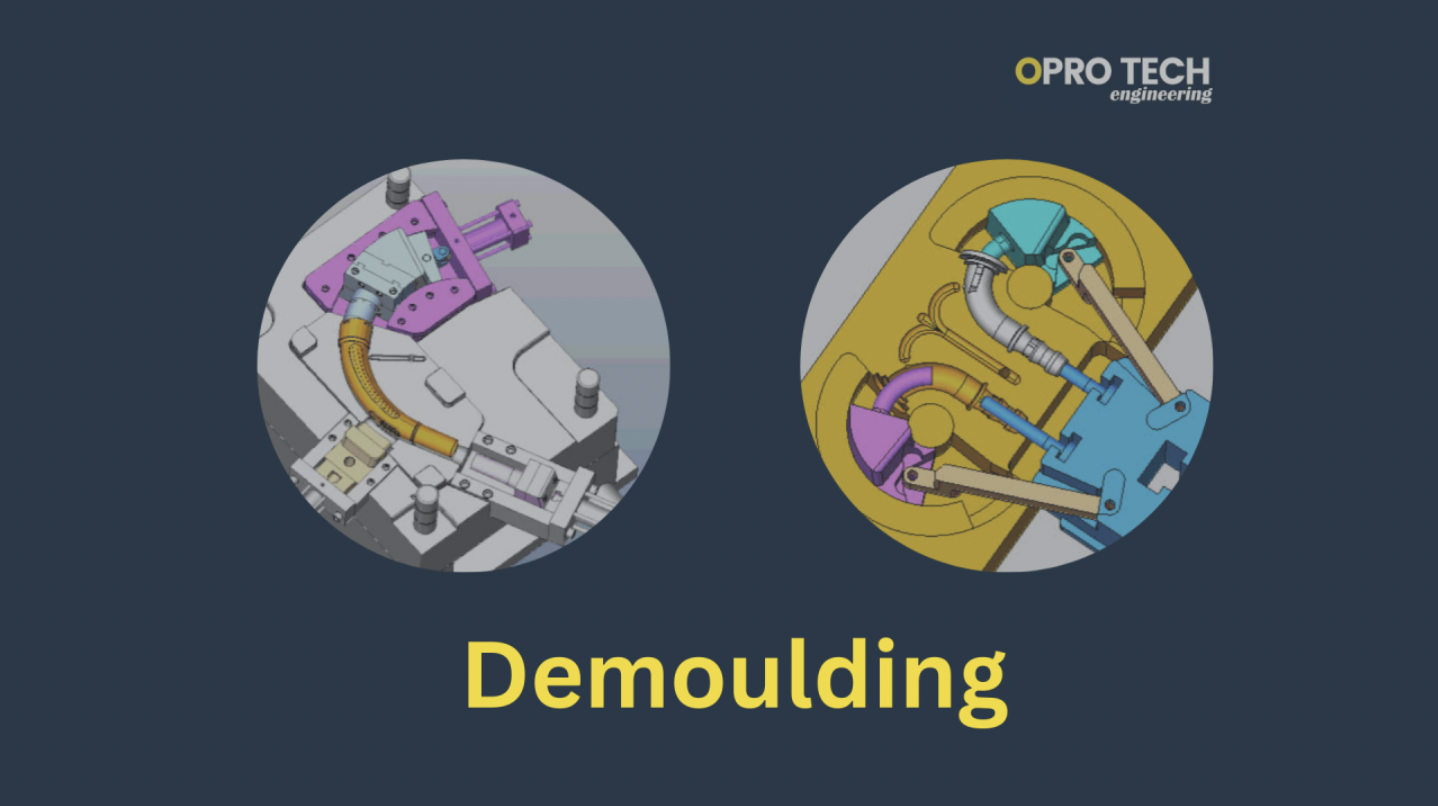
During the trial of injection molds, difficulties in mold release often occur.
There are many reasons for the difficult mold release of injection molds:
- Design of waterways;
- Grooves inside the mold;
- Mold release of the front and rear molds;
- Low mold smoothness;
- Insufficient mold release slope;
- Consistency of the ejection of the slider and the ejector pin.
Insufficient mold release slope is one of the important reasons for difficult mold release.
Therefore, when designing products, the slope should be indicated on the drawing, usually between 1-2 degrees, and in special cases, it can be allowed to be above 0.5.
During operation, in order to smoothly release the product from the mold, a mold release agent containing silicone oil will be used, but only a small amount should be used. It is very difficult to remove if sprayed too thick.
At the same time, it will also affect the second processing of printed marks. Once the mold release agent is applied to the mold, it will adhere to the product, making it very difficult to remove.
Pay attention to not applying too much injection pressure, as excessive tightness between the product and the injection mold will make mold release very difficult.
The difficulty of mold release of injection molded parts is often encountered in our injection molding production process.
Poor mold release has a significant impact on the quality of injection-molded products.
Mild mold-release defects may cause scratches or patterns on the surface of the product; severe mold-release defects may cause product warping, deformation, or even breakage.
Therefore, solving the problem of injection mold release defects affects the final quality of injection molded products.
After the plastic parts are injection molded, whether using a single or multi-component ejection mechanism, the demolding process is generally completed in one step.
However, sometimes, due to the special shape of the plastic part or the need for production automation, after the demolding process is completed once, the plastic part is still difficult to remove from the cavity or cannot be automatically detached.
In this case, an additional demolding action is required to release the plastic part.
The difficulty of mold release is mainly due to the gate or the plastic part being stuck in the mold.
The solutions are considered from the following aspects:
I. Equipment:
- Insufficient ejection force or stroke. Ejection force is the force control used by injection molding equipment for mold release. For injection molding machines of different importance levels, the maximum ejection force varies. In an ideal injection molding process, the preset ejection force of the machine is basically sufficient. However, in cases where the size of the injected part exceeds the maximum injection range or the structure of the injected part is too complex, resulting in excessive internal mold gripping force, considering these issues comprehensively is conducive to analyzing the appropriate situation for ejection force.
II. Mold:
- Unreasonable or improper position of the demolding structure;
- Insufficient demolding slope;
- High mold temperature or poor ventilation;
- Rough surface of the runner or cavity;
- Poor fit between the nozzle and the mold feed port, or the nozzle diameter is larger than the feed port diameter.
III. Process:
- The barrel temperature is too high or the injection volume is too large. When the mold temperature is too high, the melt in the cavity has not cooled to the preset size, resulting in a situation where the mold cannot be released;
- The injection pressure is too high or the holding pressure and cooling time are long. Injection molding temperature includes barrel temperature, nozzle temperature, etc. Excessive temperature will cause the melt to enter the cavity unable to cool and form within the preset time, which also affects the demolding effect;
- Excessive injection volume. If the injection volume exceeds the cavity capacity, it will cause what we often call over-molding. Injecting too much melt will expand during pressure release, thereby tightly adhering to the mold and unable to be removed. Adjusting the injection volume can solve this problem;
- Improper injection molding cycle. When the injection pressure is too high or the holding time or cooling time is too long, it may also cause difficulties in demolding. Completely cooled products are also not conducive to demolding, so the injection molding cycle must be appropriate.
IV. Raw materials:
Insufficient lubricant.
The traditional demolding methods of plastic molds are roughly divided into four types: top, push, pull, and rotate.
Thanks for taking the time, for more infomation, feel free to contact: