How do you mold internal threads?
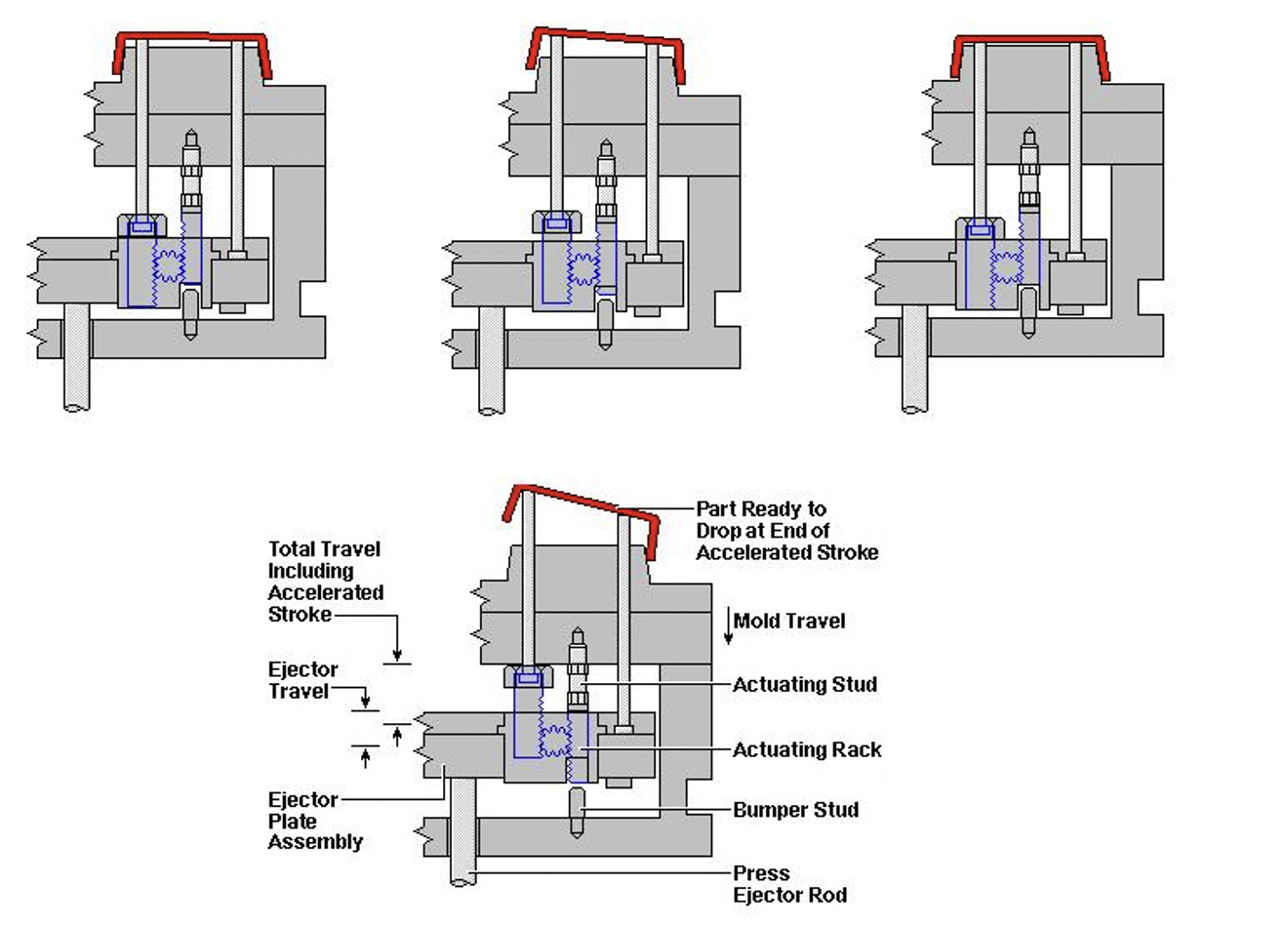
When it comes to molding internal threads in plastic parts, precision and efficiency are paramount. Achieving flawless internal threads requires a carefully orchestrated process that encompasses mold design, material selection, and molding techniques.
From creating intricate features to ensuring optimal part performance, molding internal threads presents both challenges and opportunities in the realm of injection molding.
In this article, we'll delve into the fundamentals of molding internal threads and explore the techniques and considerations that drive successful outcomes in plastic part production.
一,Stripped internal threads
“Stripped internal threads" can refer to a specific technique used to mold internal threads for plastic parts.
The stripped internal threads mechanism in tooling mold manufacturing is typically employed in situations where the design and material properties of the plastic part allow for thread stripping without damaging the part. Here are some common scenarios where this mechanism can be used effectively:
Plastic Material Flexibility: Certain types of plastics, such as thermoplastics with high flexibility and resilience, can accommodate thread stripping without causing damage to the part. These materials can deform slightly during ejection, allowing the threads to release from the mold core without breaking or distorting.
Thread Size and Geometry: Smaller thread sizes and simpler thread geometries are more conducive to thread stripping without causing damage. Larger or more complex threads may require additional reinforcement or support to prevent stripping or deformation.
Thread Depth and Pitch: Shallow threads with a low pitch are less likely to experience stripping during ejection compared to deep threads with a high pitch. Thread depth and pitch should be optimized to minimize the risk of stripping while still meeting the functional requirements of the part.
Part Design and Wall Thickness: The design of the plastic part, including the wall thickness surrounding the threaded area, plays a crucial role in determining whether thread stripping can be employed without damaging the part. Adequate wall thickness and structural reinforcement can help withstand the forces exerted during ejection.
Post-Mold Processing: If thread stripping occurs during ejection, post-mold processing techniques such as re-tapping or inserting threaded inserts can be used to restore or enhance thread integrity without compromising the part's functionality.
Material Selection: Choosing a plastic material with suitable mechanical properties, such as high tensile strength and impact resistance, can enhance the part's ability to withstand thread stripping without damage.
By carefully considering these factors and conducting thorough testing and validation, manufacturers can determine whether the stripped internal threads mechanism is appropriate for a specific application without risking damage to the plastic part.
二,Collapsible core
A collapsible core, also known as a collapsible mold core or collapsible mold insert, is a mechanism used in injection molding to create hollow areas or voids within a plastic part. It consists of two or more segments that can be retracted or collapsed inward after the injection process to facilitate the removal of the molded part with complex internal features.
The collapsible core mechanism is particularly useful for molding parts with intricate internal geometries, such as threads, undercuts, or holes. By collapsing inward, the core allows the molded part to be ejected easily without causing damage to the internal features.
Here's a detailed explanation:
Functionality: The collapsible core is designed to create hollow areas or cavities within a molded part, which would otherwise be impossible or challenging to manufacture using traditional molding techniques. It allows for the production of parts with internal features such as threads, holes, or grooves.
Design: The collapsible core consists of two main components: the core and the sleeve. The core is a movable component located inside the cavity of the mold, while the sleeve surrounds the core. The core is typically split into segments or sections that can collapse inward to facilitate the ejection of the molded part.
Operation: During the injection molding process, the molten plastic material is injected into the cavity of the mold. As the plastic material cools and solidifies, the collapsible core collapses inward, retracting its segments or sections. This action creates space for the molded part's internal features, such as threads or undercuts, to form around the core.
Advantages:
Enables the production of complex parts with internal features without the need for additional secondary operations.
Reduces the risk of part distortion or damage during ejection, as the collapsible core allows for smooth and controlled demolding.
Improves manufacturing efficiency and reduces production costs by eliminating the need for specialized tooling or secondary processes.
Applications: The collapsible core mechanism is commonly used in industries such as automotive, aerospace, medical, and consumer goods, where parts with intricate internal geometries are required. It is particularly useful for manufacturing components such as threaded inserts, gear teeth, internal grooves, and other complex features.
Overall, the collapsible core mechanism is a versatile and efficient solution for producing high-quality plastic parts with internal undercuts or threads, offering manufacturers greater design flexibility and production capabilities.
三,Unscrewing device
An unscrewing device, also known as a thread demolding mechanism, is a specialized feature used in injection molding tooling to produce plastic parts with threaded or helical features. Here's a breakdown of its functionality and operation:
Functionality: The unscrewing device is designed to facilitate the ejection of plastic parts with threaded or helical geometries from the mold cavity. It ensures that these intricate features are accurately reproduced in the molded parts and allows for smooth demolding without damaging the threads.
Design: The unscrewing device typically consists of a rotating mechanism integrated into the mold. It includes components such as cams, gears, racks, or hydraulic cylinders that impart rotary motion to the threaded core or cavity insert during the ejection phase of the molding cycle.
Operation:
Once the plastic material has been injected into the mold cavity and has solidified, the unscrewing device engages to demold the threaded part.
The rotating mechanism of the unscrewing device applies controlled rotational movement to the threaded core or cavity insert, effectively unscrewing it from the molded part.
This rotational motion allows the threaded features of the part to disengage from the mold's threads or inserts, facilitating smooth and precise ejection without causing damage to the threads.
Advantages:
Enables the production of plastic parts with intricate threaded or helical features, such as caps, closures, bottle tops, and threaded connectors.
Ensures accurate reproduction of thread profiles and pitch, maintaining the dimensional integrity of the molded parts.
Reduces the risk of thread damage or distortion during ejection, resulting in high-quality finished parts with precise thread geometry.
Applications: Unscrewing devices are widely used in industries such as automotive, medical, packaging, and consumer goods manufacturing, where threaded plastic components are common. They are essential for producing threaded parts with tight tolerances and complex geometries.
Overall, unscrewing devices play a crucial role in injection molding operations, enabling the efficient production of plastic parts with threaded or helical features while ensuring high quality and dimensional accuracy.
Last we got an enquiry about a cap for gasoline engines which has got threads, then we suggest this unscrewing device. Today I read more about this mechanism, if you are interested in as well. Please check this out.
四,Hand-loaded thread inserts
Hand-loaded thread inserts are components used in tooling molds to create threaded holes or inserts in plastic parts. Unlike automated or mechanical thread inserts, hand-loaded inserts are manually placed into the mold before injection molding.
Here are some key points about hand-loaded thread inserts:
Manual Placement: These inserts are typically made of metal and are manually positioned within the mold cavity before the injection process begins. They are placed in predetermined locations to create threaded features in the molded plastic parts.
Versatility: Hand-loaded thread inserts allow for flexibility in mold design and production. They can be used to add threaded inserts to plastic parts where automated or integrated insert molding processes may not be feasible or cost-effective.
Threaded Hole Creation: During the injection molding process, the molten plastic material flows around the hand-loaded inserts, forming threaded holes or bosses in the final molded part. This allows for the creation of durable and precise threads directly within the plastic component.
Suitable Applications: Hand-loaded thread inserts are commonly used in various industries for products requiring threaded features, such as electronic enclosures, automotive components, consumer goods, and industrial equipment.
Manual Assembly: After the molding process, if necessary, additional manual operations may be required to install fasteners or screws into the threaded holes created by the inserts.
Cost-Effective Solution: Hand-loaded thread inserts can be a cost-effective solution for low to medium volume production runs or for parts with complex geometries where automated insert molding processes may not be practical.
https://www.youtube.com/watch?v=gAMAjWRU_mM
Overall, hand-loaded thread inserts offer a manual yet effective method for incorporating threaded features into plastic parts during the injection molding process, providing versatility and cost-effectiveness in mold design and production.
In conclusion, molding internal threads demands a blend of expertise, innovation, and precision. By understanding the intricacies of mold design, selecting the right materials, and employing advanced molding techniques, manufacturers can achieve exceptional results in producing plastic parts with internal threads.
At Opro Tech Engineering, we specialize in delivering cutting-edge solutions for tooling molds and CNC machining, catering to the diverse needs of our clients worldwide. For further inquiries or assistance, feel free to reach out to me directly at danny@opro-tech.com.
Let's collaborate to bring your projects to fruition with excellence and precision.