Cold Slug Wells: Enhancing Mold Performance and Part Quality
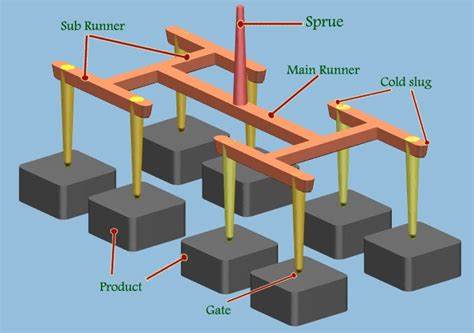
As a business development manager in tooling mold, I've made it a personal mantra to learn something new every day.
Today, my focus turned to understanding the intricacies of cold slug wells in injection molding. If you share my curiosity and are keen to delve into this topic, I invite you to join me as we explore the significance and functionality of cold slug wells in the fascinating world of mold design and manufacturing. :)
In tooling mold design, a Cold Slug Well can be a beneficial feature, especially in certain molding processes. However, its necessity depends on various factors such as the material being molded, the complexity of the part design, and the specific requirements of the manufacturing process.
A cold slug well is a feature integrated into the mold design of an injection molding tool. It is typically located near the gate, which is the point where molten plastic enters the mold cavity. The cold slug well serves as a reservoir for the initial portion of the injected material, which tends to cool and solidify more quickly than the rest of the molten plastic. By capturing this cold slug of material, the well helps prevent it from entering the mold cavity and potentially causing defects in the finished part, such as surface imperfections or flow lines. The cold slug well improves the quality and consistency of the molded parts by ensuring that only properly melted and flowable plastic enters the cavity.
Here are some points to consider regarding the necessity and function of a Cold Slug Well in tooling mold design:
- Necessity:In some molding processes, particularly those involving materials prone to the formation of cold slugs or solidified material residues, a Cold Slug Well can help mitigate potential issues.Cold slugs can form during the injection molding process when molten material cools and solidifies prematurely in the nozzle or runner system. These cold slugs can affect part quality and consistency if not properly managed.While a Cold Slug Well is not always necessary, its inclusion can improve mold performance and reduce the likelihood of defects caused by cold slugs.
- Number of Wells:The number of Cold Slug Wells to be designed into a tooling mold depends on factors such as the size and complexity of the mold, the number of injection points, and the expected frequency of cold slug formation.Typically, molds may feature one or more Cold Slug Wells strategically positioned along the runner system or near injection points where cold slugs are likely to form.
- Function:The primary function of a Cold Slug Well is to trap and contain cold slugs or solidified material residues during the injection molding process. By providing a designated space for cold slugs to accumulate, the Cold Slug Well prevents them from reaching the cavities where they could affect part quality or cause defects.Cold Slug Wells also facilitate the purging of trapped material during mold cycling, helping to maintain consistent part quality and reduce the need for manual intervention or mold maintenance. In summary, while Cold Slug Wells are not universally required in all tooling molds, they can be valuable features in certain molding applications, especially those involving materials prone to cold slug formation. The decision to incorporate Cold Slug Wells into a mold design should be based on a thorough assessment of the specific molding process requirements and potential benefits in terms of part quality and production efficiency.
In general, hot runner molds typically do not require Cold Slug Wells. This is because hot runner systems are designed to maintain the molten state of the plastic material throughout the molding process, from the injection nozzle to the cavity, without allowing it to solidify prematurely.
Here's why Cold Slug Wells are usually not needed in hot runner molds:
- Continuous Heating: Hot runner systems consist of heated manifold and nozzles that keep the plastic material in a molten state as it flows through the runner system. This continuous heating prevents the formation of cold slugs or solidified material residues along the runner channels.
- Direct Injection: In hot runner molds, molten plastic is injected directly into the cavity through the heated nozzles, bypassing the need for long flow paths where cold slugs could form. The material remains molten and fluid throughout the injection process, minimizing the risk of cold slug formation.
- Efficient Material Flow: Hot runner systems are designed to promote efficient material flow and minimize material residence time, reducing the likelihood of material cooling and solidification within the runner system.
While Cold Slug Wells are not typically incorporated into hot runner molds, there may be exceptions depending on specific molding requirements or material characteristics. However, in most cases, the continuous heating and direct injection provided by hot runner systems effectively eliminate the need for Cold Slug Wells, contributing to smoother molding processes and improved part quality.
When we talk about cold slug wells, you may also interested in Sprue Puller Pin.
A sprue puller pin is a component used in injection molding processes. It is designed to help remove the sprue, which is the excess material that solidifies in the channel leading from the nozzle of the injection molding machine to the mold cavity. The sprue puller pin aids in cleanly separating the sprue from the molded part, ensuring smooth ejection from the mold. This helps prevent defects such as flash or burrs on the finished part.
Sprue Puller Pin:
- Definition: The sprue puller pin is a component used in injection molding molds. It is typically a cylindrical pin with a specialized shape at the tip.
- Usage:The sprue puller pin is inserted into the mold to extract the sprue, which is the excess material that solidifies in the runner system of the mold during the injection molding process. It helps in separating the sprue from the molded parts, ensuring that the sprue remains attached to the B plate of the mold while the molded parts are ejected.
- Functionality:By pulling the sprue away from the molded parts, the sprue puller pin prevents contamination of the final product and facilitates efficient production by clearing the mold for the next cycle.
Here's a brief overview of the three common types of sprue pullers:
Annular Ring Sprue Puller:
- Shape: An annular ring sprue puller features a circular or ring-shaped tip at the end of the pin.
- Usage:The annular ring shape provides a wider contact area with the sprue, allowing for more efficient extraction. It is particularly useful for pulling large or irregularly shaped sprues from the mold.
- Advantages:Enhanced gripping capability due to the circular shape.Suitable for a wide range of sprue sizes and shapes.
- Applications: Commonly used in molds with larger sprues or when dealing with complex part geometries.
Reverse Taper Sprue Puller:
- Shape: A reverse taper sprue puller features a tapered or conical tip that narrows towards the end of the pin.
- Usage:The tapering shape allows for gradual engagement with the sprue, providing controlled pulling action. It is effective for extracting sprues with minimal force, reducing the risk of damage to the mold or parts.
- Advantages:Gentle extraction process, minimizing stress on the mold components.Ideal for delicate or intricate molds where precision is crucial.
- Applications: Suitable for molds with smaller or more intricate sprues, particularly in high-precision molding applications.
Z Pin Sprue Puller:
- Shape: A Z pin sprue puller features a zigzag or Z-shaped configuration at the end of the pin.
- Usage:The Z shape provides multiple contact points along the sprue, offering increased gripping power.It facilitates efficient extraction of sprues with irregular shapes or undercuts.
- Advantages:Enhanced stability and grip due to the multiple engagement points.Effective for pulling sprues with complex geometries or difficult-to-reach areas.
- Applications: Commonly used in molds with intricate part designs or when dealing with challenging sprue configurations.
In summary, while all three types of sprue pullers serve the same basic function of extracting sprues from injection molds, they differ in their shape and design, with each type offering unique advantages suited to specific molding requirements and part geometries.
Thanks for taking the time to explore the world of cold slug wells with me. I hope this article has shed some light on their importance in injection molding processes.
If you have any questions, feedback, or if you've spotted any inaccuracies, please don't hesitate to reach out to me at danny@opro-tech.com or leave your comments below. Your insights and contributions are greatly appreciated as we continue to learn and grow together in the realm of mold design and manufacturing.
Dan
Business development manager
Phone: +86 134 1699 5669
Skype: danny@opro-tech.com Factory add: No 39, Zhen an west road, Changan town , Dong guan city, China.
Injection Mold / CNC Machining / 3D Printing / Prototyping