Analysis of In-Mold Labeling Technology
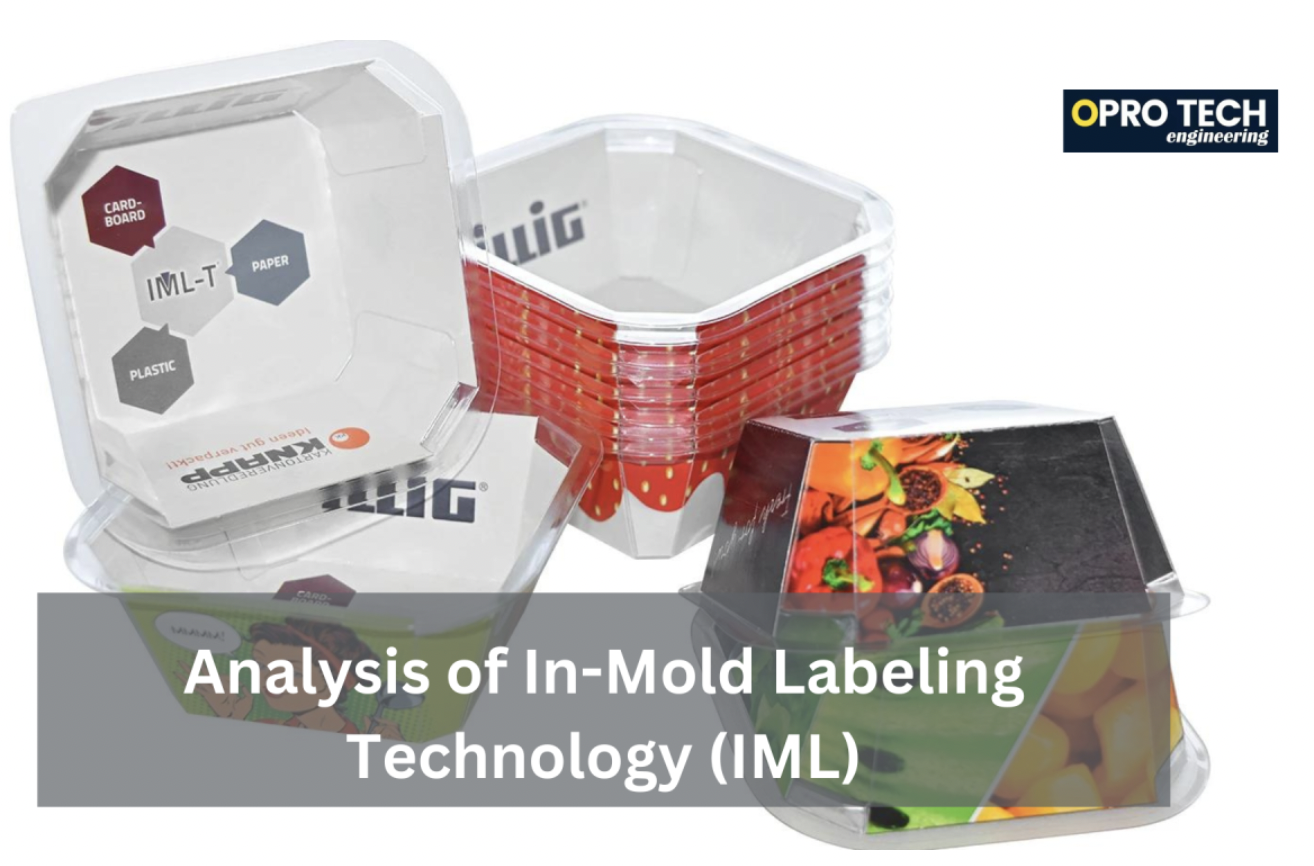
In-mold labeling (IML) has been prevalent in developed countries in Europe and the United States for over 20 years.
In recent years, this innovative labeling technology has started to take root in China, finding applications in industries such as motor oil, daily necessities, food, and pharmaceuticals.
What is In-Mold Labeling?
In-mold labels are special labels made from PP or PE synthetic paper, treated on the surface, and coated with a special hot-melt adhesive on the back. These labels are printed to create trademarks. A mechanical arm picks up the pre-printed labels and places them inside a mold, where vacuum holes on the mold firmly hold the label in place.
When the plastic bottle material is heated and forms a tube, the labeled mold quickly closes, and air is blown into the tube, pressing it tightly against the mold walls. At this point, the temperature inside the mold is still relatively high, causing the adhesive on the label to melt and bond with the plastic bottle inside the mold.
When the mold is reopened, the bottle is formed with the label seamlessly integrated, creating a polished appearance as if the label were directly printed on the bottle's surface.
This seamless labeling effect is increasingly favored by consumers.
This article will introduce the main technical aspects involved in in-mold labeling.
1. Materials
The high technical content of in-mold labels is first reflected in the materials. The earliest entry into the Chinese market was Japan's YUPO in-mold labels, which are considered the world's most successful in-mold labeling material. Now, France's Polyart blow molding in-mold labels have also entered the Chinese market, along with some local companies developing similar materials.
In-mold labels need to have good printability to ensure ink adhesion to the surface, and they must also ensure good processability for post-processing, such as die-cutting and cold stamping. Moreover, these materials must bond with the plastic bottle during blow molding.
In-mold label materials are divided into two main categories: paper and plastic films. The former can deform when exposed to water or moisture, reducing its value, though it has the advantage of no static interference, reducing label loss during blow molding. However, it is not the same material as the plastic bottle, making recycling difficult. Currently, plastic film-type in-mold label materials are commonly used domestically and internationally.
The structure of in-mold label materials includes a printing surface, a middle layer, and an adhesive layer. The printing surface receives the ink, forming colorful images; the middle layer supports the printing surface, providing stiffness and transparency, ensuring accurate registration during printing and high-temperature processes. The adhesive layer melts under high temperature, bonding the label with the plastic container.
There are three types of printing surface materials: PE, BOPP, and PE+PP. Since most plastic containers are made of PE, using PE in-mold labels facilitates recycling. To enhance ink adhesion, surface coating or corona discharge treatment is typically used.
The adhesive layer has two structures: smooth and textured. The former directly contacts the blank, naturally expelling air, suitable for small-area labels. The latter has a textured surface, allowing air to escape through the channels, preventing bubbles. The adhesive layer also has anti-static properties to prevent double-sheet issues during printing and ensure smooth separation for efficient processing.
2. Printing of In-Mold Labels
Different printing companies can choose different printing processes based on their equipment. Offset printing, flexographic printing, letterpress printing, and gravure printing can all be used for in-mold labels, with offset and flexographic printing being the most common.
1. Offset Printing
Offset printing excels in fine dot printing but is less effective for lines, solid printing, and color saturation compared to other methods. It does not allow inline processing, requiring offline processes like die-cutting, cold stamping, and varnishing. However, it is suitable for small-batch label printing with short cycles and high flexibility.
2. Gravure Printing
Gravure printing offers superior solid printing and color saturation but is not ideal for fine dots and detailed trademarks. It has easy color difference control. However, the paper path in gravure printing is longer, increasing the chances of static electricity. High plate-making costs and long cycles make it suitable for long-run in-mold label printing.
3. Letterpress Printing
Letterpress printing is good for solid and line trademarks but not for fine dots, and color difference control is relatively easy, though ink streaks may occur. It is more cost-effective than gravure and flexographic printing.
4. Flexographic Printing
Flexographic printing excels in integrating printing and post-processing, allowing for inline production from feeding to final product. With improvements in flexographic plate-making technology, the quality of dot printing has significantly improved. While environmentally friendly water-based inks are not yet mature, UV inks with good fluidity are popular for in-mold label printing.
3. Post-Processing of In-Mold Labels
After printing, in-mold labels undergo processes like varnishing, stamping, and die-cutting as per customer requirements.
1. Varnishing
Varnishing enhances the gloss and decorative features of in-mold labels and improves abrasion and heat resistance. If using vacuum absorption, anti-static agents and varnish smoothness should be adjusted. For electrostatic absorption, anti-static agents should be avoided. If foil stamping is needed, select varnish compatible with foil stamping. Test varnished labels before mass production to avoid waste.
2. Stamping
In-mold label materials can be stamped either before or after varnishing, using cold or hot stamping techniques. Cold stamping is mainly used in flexographic printing and requires high technical skills for a good visual effect. Hot stamping factors include foil, temperature, pressure, and speed. Use foil with a lower melting point than the label’s adhesive and control pressure and time to avoid deformation. Adjust temperature and pressure based on material and foil characteristics for optimal results.
3. Die-Cutting
Die-cutting of in-mold labels is similar to playing cards, involving cutting through the material. Proper static removal during die-cutting is crucial to ensure neat stacking and accurate labeling. Die-cutting can be done using sheet-fed or roll-fed methods, depending on the equipment and label type. Roll-fed die-cutting can be inline or offline. Roll-fed flat die-cutting offers high precision and can handle intermittent or continuous feeding. Roll-fed rotary die-cutting is highly precise and cost-effective for long runs, commonly used in flexographic inline processing. Sheet-fed flat die-cutting is less precise and uses an automatic feeder for offline processing.
4. In-Mold Labeling Methods
Once die-cut, labels are picked up by a mechanical arm and placed in the mold, where plastic extrusion and air pressure fuse the label with the bottle.
There are two methods: vacuum negative pressure and electrostatic absorption.
1. Vacuum Negative Pressure
This common and widely used method involves adding micro-vacuum holes to existing molds, making it cost-effective and efficient with inconspicuous vacuum marks. This mature technology requires no special equipment modifications.
2. Electrostatic Absorption
This method uses static electricity to adhere labels inside the mold. Though it doesn’t require equipment modifications, successful implementations are yet to be seen domestically. It involves adding a high-voltage static discharge system to charge the labels and a static elimination system to remove residual static, ensuring proper label placement and avoiding label adhesion issues. Suitable label substrates and inks are essential.
5. Advantages of In-Mold Labels
1. Attractive Appearance
In-mold labels integrate seamlessly with plastic containers, providing a sleek look with no visible edges. Their high print quality allows for detailed and vibrant designs, enhancing visual appeal. Unlike adhesive labels, in-mold labels don’t peel or lift in humid conditions.
2. Anti-Counterfeiting
The complex process of in-mold labeling makes it difficult to counterfeit, providing a technical barrier against forgery. Unlike easily replicable adhesive labels, in-mold labels offer better protection against counterfeits.
3. Recycling
In-mold label materials are of the same type as plastic bottles, facilitating efficient and cost-effective recycling. In contrast, adhesive labels require removal and cleaning before recycling, making the process more cumbersome and costly. In-mold labels align with green packaging trends.
6. Applications of In-Mold Labels
In-mold labels are primarily used in the following industries:
- Motor Oil: Including lubricants, gear oil, and antifreeze containers.
- Daily Necessities: Such as body wash, shampoo, cleaners, detergents, and personal care products.
- Food: Including soy sauce, ice cream, coffee, juice, tea beverages, and yogurt containers.
- Pharmaceuticals: For high-end medicine packaging.
Though relatively new, in-mold labeling is attracting more manufacturers.
In Europe and the U.S., it is becoming a stable technology, while in China, it is rapidly growing at a rate of 70%.
Looking ahead, in-mold labeling is set to challenge adhesive labels, favor plastic materials, and attract more end-users.
Thanks for reading, any questions please feel free to contact: xiu@opro-tech.com
WhatsApp: +66 807412390