Overcoming Challenges with PA66 + GF30 Material in Injection Molding with Manual Metal Inserts
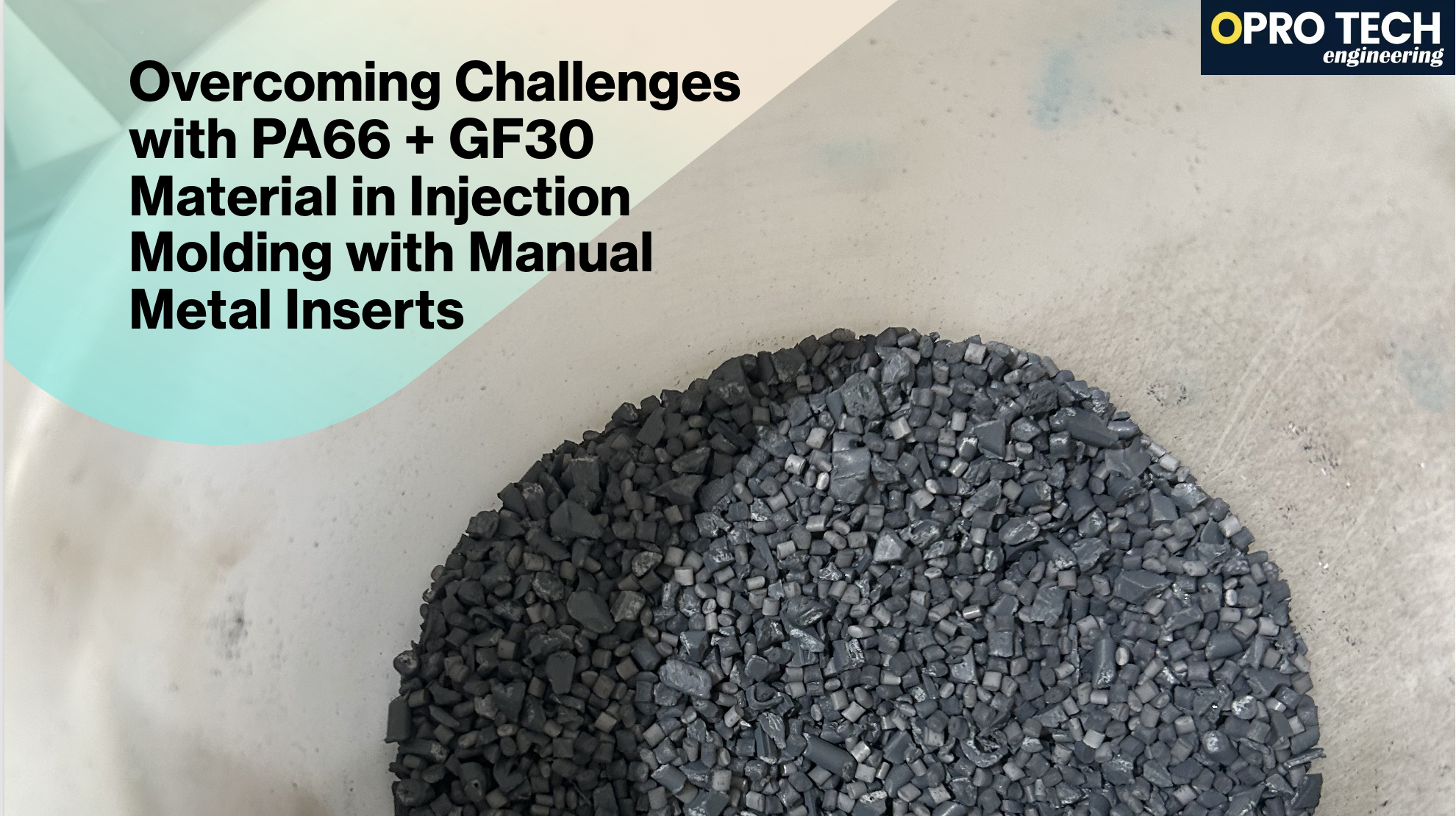
Overcoming Challenges with PA66 + GF30 Material in Injection Molding with Manual Metal Inserts
At Opro tech engineering, we specialize in precision injection molding and have extensive experience working with advanced materials like Nylon PA66 + GF30. This material, reinforced with 30% glass fiber, is well-known for its high strength, rigidity, and excellent thermal properties, making it a popular choice in automotive, electrical, and industrial applications. However, when it comes to the injection molding process, PA66 + GF30 can present some unique challenges, especially when metal inserts are involved.
The Challenge: Quick Cooling and Extended Cycle Time
One of the primary issues we encountered with Nylon PA66 + GF30 is its tendency to cool down rapidly during the injection process. Normally, the cycle time for this material needs to be tightly controlled within 5 to 10 seconds. However, for a recent project, the tooling mold required the manual insertion of metal components before the plastic was injected.
This manual process took between 20 and 30 seconds, which created a significant delay. As a result, the PA66 + GF30 material in the nozzle cooled down too quickly, leading to issues like:
- Incomplete filling of the mold (short shot)
- Material solidification in the nozzle, causing blockages
- Increased waste of raw material
Our Solution: Optimizing the Process for Mass Production
While manual insertion and the use of a heater to keep the nozzle warm worked for small sample runs (e.g., 50 pcs), we quickly realized that this method was inefficient and unsustainable for mass production. To address this, we implemented several solutions:
- Switching to a Different Material: For large-scale production, we switched to ABS+PC+15 GF, a material that did not have the same quick-cooling issues. This allowed us to maintain a more consistent cycle time without worrying about the material solidifying prematurely.
- Pre-heating Metal Inserts: In cases where PA66 + GF30 is still required, we’ve started pre-heating the metal inserts before placing them in the mold. This step helps ensure that the plastic material does not cool down too rapidly upon contact with the cooler metal.
- Automating the Process: To minimize human error and reduce delays, we are exploring robotic automation for metal insert placement. This will allow us to drastically reduce the cycle time while maintaining quality and precision.
- Hot Runner System: For certain projects, utilizing a hot runner system can keep the material hot and ready for injection without the risk of cooling down in the nozzle.
Addressing Rust Issues with Metal Inserts
Another challenge we faced involved the rusting of metal inserts. After cleaning the anti-rust oil off the inserts, we observed that some began to show signs of rust before the injection process was completed. Our solution to this problem has been to:
- Remove rust with a soft cloth before use
- Apply a protective layer of oil to the finished items post-molding to ensure long-term protection against rust
Conclusion: Adapting and Innovating
At Opro tech engineering, we are committed to continuously improving our processes to meet the unique demands of each project. Working with materials like PA66 + GF30, especially in conjunction with metal inserts, requires a deep understanding of material behavior and cycle time management. Through a combination of material optimization, pre-heating techniques, and automation, we have successfully overcome these challenges to deliver high-quality results for our clients.
If you’re facing similar challenges or would like to learn more about how we can support your injection molding needs, feel free to contact us!
Factory add: No 39, Zhen an west road, Changan town , Dong guan city, China.