Conformal Cooling Channels: The Future of Efficient Injection Molding
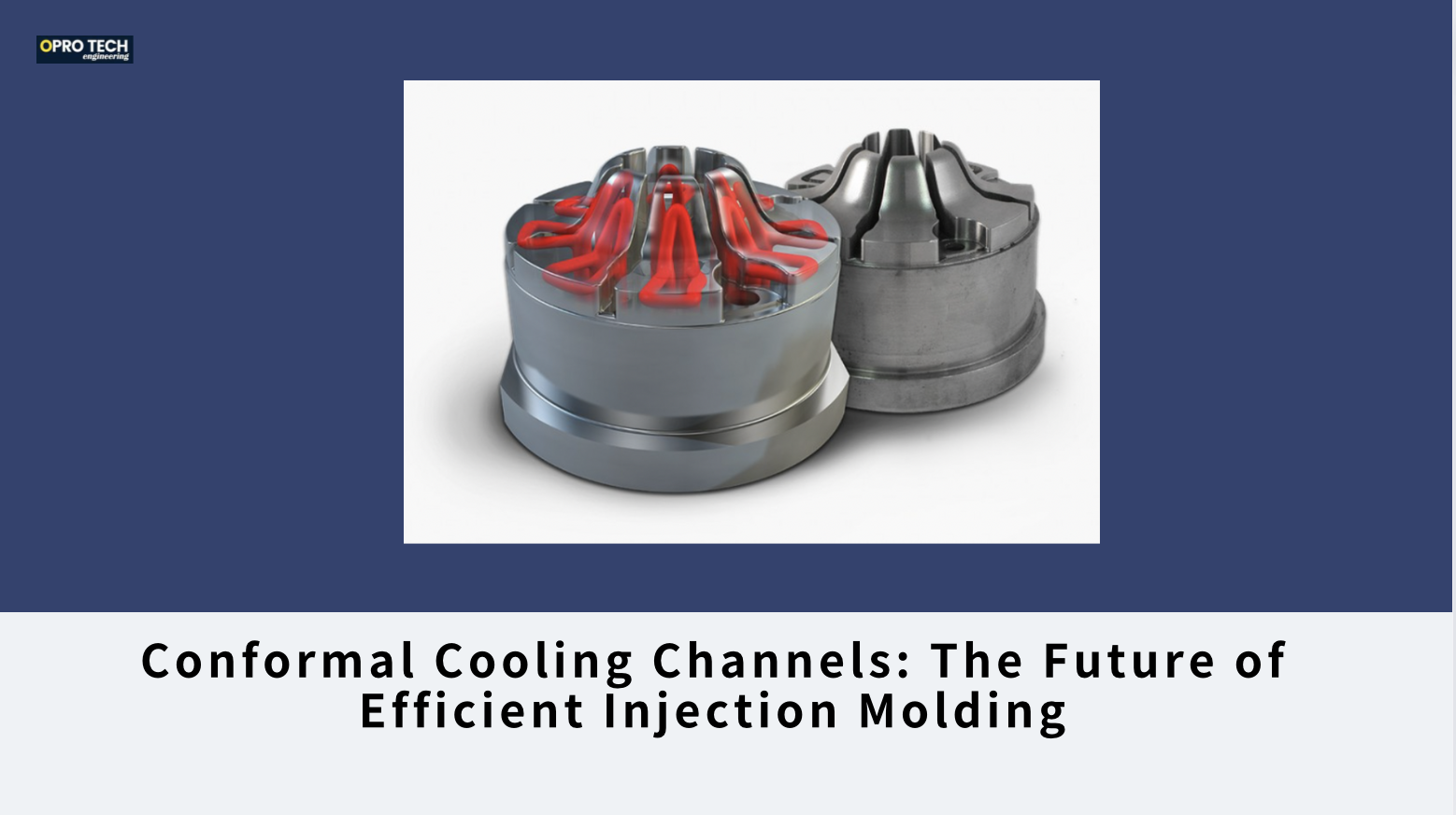
In the world of injection molding, efficient cooling is paramount to producing high-quality parts while minimizing cycle times. Enter Conformal Cooling Channels (CCC)—a revolutionary approach that optimizes the cooling process by allowing cooling channels to closely follow the contours of the mold. Unlike traditional straight-line cooling systems, conformal cooling channels are designed using advanced technologies like 3D printing, enabling more uniform heat distribution and reduced cooling times. This article will explore the principles behind CCC, its benefits in enhancing production efficiency, and how it is transforming the landscape of modern manufacturing.
Conformal Cooling Channels (CCC) are specially designed cooling channels within an injection mold that closely follow the contours of the part being molded. Unlike traditional straight-line cooling channels, which are limited by conventional drilling methods, conformal cooling channels are custom-shaped and often created using advanced manufacturing techniques like 3D printing or additive manufacturing.
What is Conformal Cooling and How Does it Work?
• Traditional Cooling Channels: In a conventional injection mold, cooling channels are drilled in straight lines, which can lead to uneven cooling, especially in complex or irregularly shaped parts. This uneven cooling can result in defects like warping, shrinkage, or longer cooling times.
• Conformal Cooling Channels (CCC): These channels are designed to "conform" or follow the surface geometry of the mold cavity as closely as possible. This design maximizes the surface area contact between the cooling fluid (typically water or other coolants) and the mold, resulting in more efficient and uniform cooling.
What Do We Use with Conformal Cooling Channels?
1. Advanced Manufacturing Techniques:
o 3D Printing / Additive Manufacturing: The complex geometries of CCC are often created using 3D printing techniques like Direct Metal Laser Sintering (DMLS), Selective Laser Melting (SLM), or other metal additive processes. These methods allow the production of intricate cooling channel designs that are impossible to achieve with conventional machining.
2. Cooling Fluids:
o Water: Water is the most commonly used coolant in CCC due to its high heat transfer efficiency.
o Glycol or Specialized Coolants: In some cases, alternative coolants may be used for higher heat transfer needs or in special circumstances (e.g., when corrosion resistance is required).
3. Temperature Control Systems:
o Chillers: These are used to maintain precise temperature control over the cooling fluid. A chiller continuously circulates the coolant through the mold’s cooling channels to remove heat from the molded part efficiently.
How Do We Use Conformal Cooling Channels?
1. Design Phase:
o In the mold design stage, the cooling channels are designed to match the contours of the mold cavity. This is done using 3D CAD software, where the channels are strategically placed to ensure optimal cooling across the entire surface area of the molded part.
2. Manufacturing the Mold:
o Since CCC designs are complex, traditional machining techniques (like drilling) are not sufficient. Instead, metal 3D printing (such as DMLS) is used to create the cooling channels within the mold. This process enables the intricate and non-linear paths required for CCC.
3. Molding Process:
o During the injection molding process, the conformal cooling channels enable faster and more uniform cooling of the part. The coolant flows through the channels, removing heat more efficiently and reducing cycle time.
4. Optimizing Cooling:
o After the mold is produced and the cooling system is in place, the temperature of the cooling fluid is precisely controlled to achieve the desired cooling rate. The efficiency of CCC means that cycle times can be significantly reduced, leading to higher production rates and improved part quality.
Advantages of Conformal Cooling Channels (CCC)
1. Faster Cooling and Shorter Cycle Times:
o Conformal cooling ensures that parts cool more evenly and quickly, reducing the overall cycle time by up to 20-40%, depending on the part complexity.
2. Improved Part Quality:
o More uniform cooling leads to less warping, shrinkage, or internal stresses in the molded parts. This means fewer defects and higher-quality parts.
3. Reduced Warping and Dimensional Variability:
o Parts with complex geometries are less likely to experience uneven cooling, which reduces the likelihood of warping or dimensional inconsistencies.
4. Increased Tool Life:
o Efficient cooling reduces thermal stresses on the mold, increasing its lifespan and reducing maintenance costs.
5. Energy Savings:
o Reduced cooling time means lower energy consumption during the injection molding process, leading to energy savings over time.
Applications of Conformal Cooling Channels
Conformal cooling is particularly beneficial in industries and applications where precision, quality, and efficiency are critical, such as:
1. Automotive:
o For producing complex parts like dashboard components or bumpers, where uniform cooling reduces the risk of defects and improves dimensional accuracy.
2. Medical Devices:
o Used for producing high-precision components such as surgical tools or diagnostic equipment, where part consistency and quality are crucial.
3. Consumer Electronics:
o In the production of cases, housings, and other components that require tight tolerances and high-quality surface finishes.
4. Aerospace:
o Where complex, high-strength parts are needed with minimal warping or dimensional change.
5. Packaging:
o High-volume production of packaging parts, such as bottle caps or containers, where speed and consistency are vital.
Summary of How Conformal Cooling Channels Work and Their Benefits
• Design: Cooling channels are designed to follow the contour of the mold cavity using advanced software.
• Manufacturing: Metal 3D printing or hybrid manufacturing is used to create the mold with CCC.
• Process: The coolant flows through the channels during molding, ensuring faster and more even cooling.
Benefits:
• Faster cycle times
• Reduced part defects
• Lower energy consumption
• Enhanced tool life
Applications: Automotive, medical devices, electronics, aerospace, packaging, and other high-precision industries.
Incorporating Conformal Cooling Channels into molds can lead to major improvements in efficiency, cost reduction, and product quality, especially for complex, high-volume injection molding projects.
As the manufacturing industry continues to evolve, the implementation of Conformal Cooling Channels is proving to be a game-changer for achieving faster, more efficient production cycles and higher-quality outputs. By embracing this innovative cooling technology, manufacturers can significantly improve their processes and outcomes.
I encourage you to share your thoughts and experiences with conformal cooling channels or reach out with any questions you may have. Let’s continue the conversation—feel free to email me at danny@opro-tech.com!