Ejecting Parts from Inverted Molds: A Guide to the Challenges and Solutions
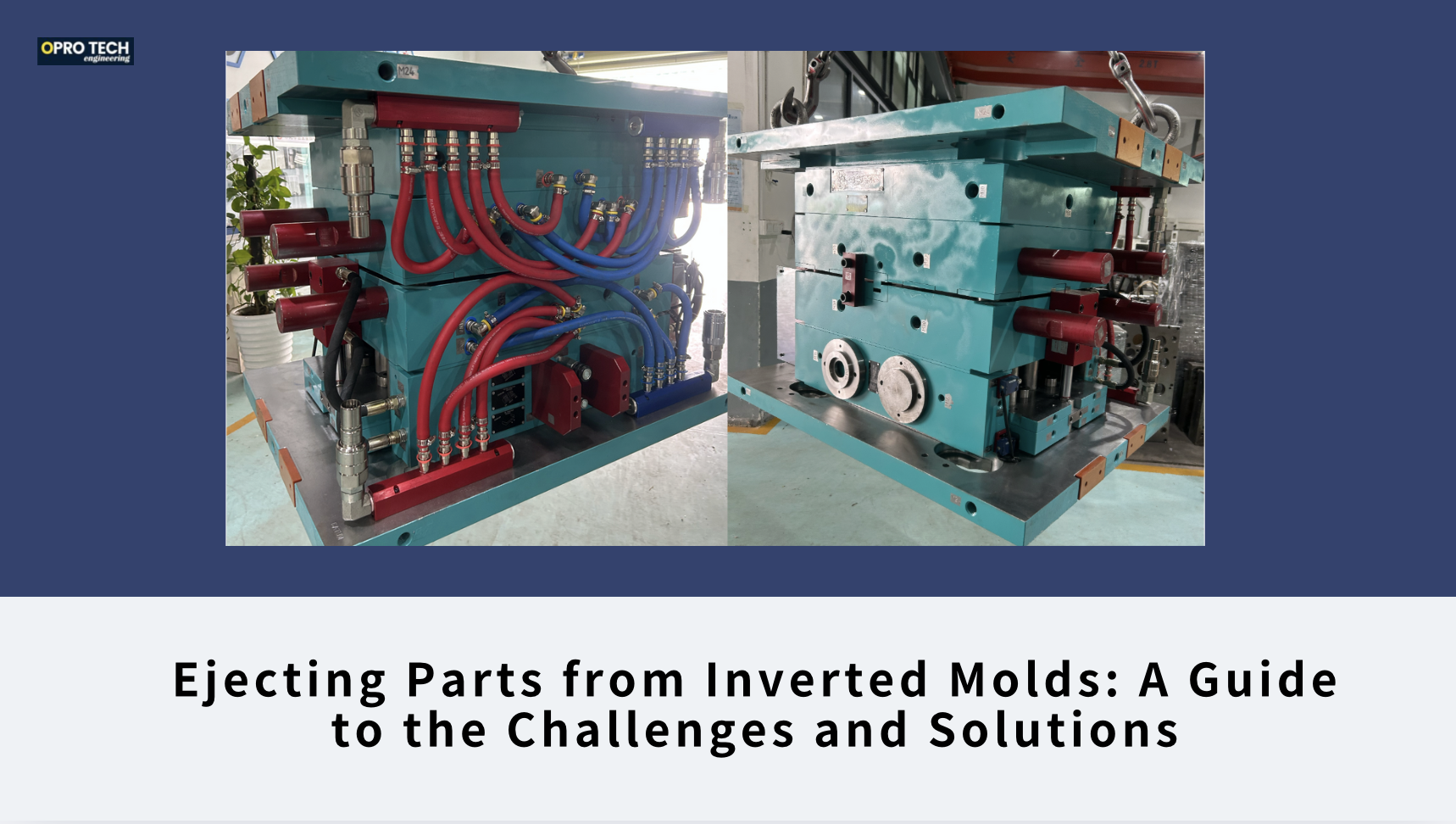
Hi, Please kindly noted the information shared in this article was gathered from various online resources and websites to provide an overview of reverse molding techniques and part ejection mechanisms. While I have made every effort to ensure accuracy, I am always eager to improve and learn. If any professionals in the field find discrepancies or have additional insights, please feel free to reach out to me directly at danny@opro-tech.com.
Your feedback is highly appreciated as I continue to expand my knowledge and understanding of this topic. Thank you!
In the world of injection molding, achieving complex geometries and intricate internal features often requires advanced tooling techniques. One such method is the use of reverse molds or inverted molds, where the roles of the core and cavity are flipped. While this approach opens up new possibilities for molding hollow parts, undercuts, and detailed internal features, it also presents unique challenges, especially when it comes to ejection.
In a traditional mold, ejector pins are typically placed on the cavity side, pushing the part out of the mold with ease. However, in an inverted mold, this conventional ejection mechanism must be rethought. In this article, we’ll explore the methods and techniques used to eject parts from inverted molds, ensuring that delicate features are preserved and the production process runs smoothly.
What is a Reverse Mold or Inverted Mold?
In a standard mold, the mold cavity is the negative space where the material is injected and forms the shape of the part. The mold consists of two halves: the core (inside part) and the cavity (outside part). The material is injected into the cavity, and after cooling, the mold is opened to eject the part.
In a reverse mold or inverted mold, the structure is flipped:
- The cavity and core are switched, meaning the core becomes the external surface of the part, and the cavity becomes the inner surface.
- This is often used for parts with internal geometries that need to be formed from the outside, such as hollow parts or parts with specific undercuts that are challenging to mold using traditional methods.
Key Differences from a Standard Mold:
- Cavity and Core Orientation: In a reverse mold, the traditional roles of the cavity and core are inverted. The external features are formed from the core, and the internal features are formed from the cavity. This inversion is often used to create specific features that would be difficult to achieve with a standard mold.
- Tooling Complexity: A reverse mold can be more complex to design and manufacture, as it may require special techniques for ejecting parts (e.g., using collapsible cores or side actions) to remove parts without damaging delicate features.
- Application: Reverse molds are often used for molding hollow parts, deep undercuts, or parts with intricate internal geometries. This technique can help achieve geometries that might otherwise require multiple molding steps or secondary operations.
- Ejection Mechanism: In some cases, reverse molds can also require different ejection mechanisms, such as the use of specialized ejector pins or slide mechanisms, to remove the part without interfering with the complex design.
Why Use Reverse Molding?
- Hollow Parts: To create hollow features or internal channels in a part without the need for additional machining or inserts.
- Undercuts: To create undercuts that would otherwise be difficult to achieve in a standard mold.
- Part Integrity: Some parts with complex geometry require reverse molds to avoid damaging delicate features during the ejection process.
In summary, a reverse mold or inverted mold is used when the design requires creating an internal cavity or features that would otherwise be difficult or impossible to form with traditional molding techniques. The fundamental difference lies in the swapping of the core and cavity roles.
Here are several ways that inverted molds can eject parts:
1. Core Ejector Pins
- Placement of Ejector Pins: In a reverse mold, ejector pins can be placed on the core side, which is typically the external surface of the molded part. These ejector pins would push directly against the external surface, allowing the part to be pushed out of the cavity without damaging the interior features.
- Design Considerations: The core ejector pins may need to be positioned at strategic locations on the external part surface to avoid interfering with any delicate or detailed features on the part. For example, the ejector pins might be positioned at areas of the part where cosmetic appearance is less critical, such as along flat or hidden sections of the part.
2. Collapsible Cores
- What Is a Collapsible Core?: A collapsible core is a specialized molding component that is used to form internal geometries or undercuts. These cores are designed to collapse or retract when the mold opens, which allows the part to be ejected without damaging internal features or requiring complex ejection mechanisms.
- How It Works: In the case of an inverted mold, a collapsible core can be used to form the internal part features (such as holes or cavities). After the molding process is complete and the part has cooled, the collapsible core retracts, creating a path for the part to be ejected from the mold cavity.
- Applications: This is particularly useful for hollow or thin-walled parts with intricate internal features, like medical devices, automotive parts, or packaging components.
3. Side Actions
- What Are Side Actions?: Side actions are additional mold components that move laterally (perpendicular to the main direction of mold opening) to allow for the formation of features like undercuts, grooves, or other difficult-to-mold features. In an inverted mold, side actions can be used to release the part from the core side.
- How It Works: Side actions may move in or out of the mold to help separate the part from the core after it has been molded. After the mold opens, the side action may move away from the part, creating clearance between the core and the molded part, allowing it to be ejected.
- Design Considerations: Side actions are often used in combination with other ejection methods, such as ejector pins or collapsible cores, to ensure that the part can be released without damaging complex internal geometries.
4. Air Ejection (Blowout)
- What Is Air Ejection?: In some cases, air pressure can be used to help eject the part from the mold. This is typically used in molds where the part is tightly fitted and difficult to eject using traditional mechanical means.
- How It Works: Air is blown into the mold cavity, which helps to push the part out of the mold by creating pressure behind the part. This can be especially useful for hollow parts or those with delicate features, where conventional ejection pins or mechanisms might cause damage.
- Challenges: Air ejection may not be as commonly used in inverted molds, but in some specialized applications, it may be employed for parts with complex internal features.
5. Ejector Plates or Sleeve Mechanism
- Ejector Plate: The ejector plate can be used in an inverted mold configuration, but instead of ejecting the part from the cavity side, it can push from the core side. The ejector plate or sleeve is attached to the core part of the mold, which pushes the part out after the mold opens.
- Sleeve Mechanism: A sleeve or moving cylinder can be placed around the core to help pull or push the part out after it is molded. This can be useful when the part is delicate, or there are complex features that would be difficult to eject with traditional ejector pins.
6. Use of a Second Core (Secondary Core Ejection)
- What Is Secondary Core Ejection?: In some cases, a second mold core may be used specifically for ejection purposes. The primary core forms the main features of the part, while a secondary core, which is positioned on the core side, can be used to push or pull the part out after the mold opens.
- How It Works: This secondary core could work by sliding or moving laterally to push the part from the core side. Afterward, the part is released without the need for ejector pins on the core side. This mechanism can be quite useful when the part is complex and delicate.
7. Mold Movement Mechanism (Rotary Molds)
- Rotary or Multi-Part Molds: Sometimes, inverted molds can incorporate a rotary mechanism where the mold is divided into several parts, and the core side rotates to release the part.
- How It Works: The core may rotate or shift in multiple stages, allowing the part to be released from the core side in stages. This mechanism requires careful alignment and precision, but it can work well for parts with complex geometries.
Conclusion
In an inverted mold, the ejection process is more complicated because the part interface (the external surface) is formed on the core side. To address this, several techniques are used:
- Core ejector pins can push the part out from the core side.
- Collapsible cores can retract to allow the part to be ejected.
- Side actions can be used to release the part from the core side.
- Air ejection or secondary core ejection systems may be applied for more delicate parts.
The key to successful ejection in an inverted mold is ensuring that all features, especially delicate ones formed on the core side, are not damaged during the ejection process, which may require specialized components and techniques.