Do you wanna use RSP technology RSA material for your CNC machining parts?
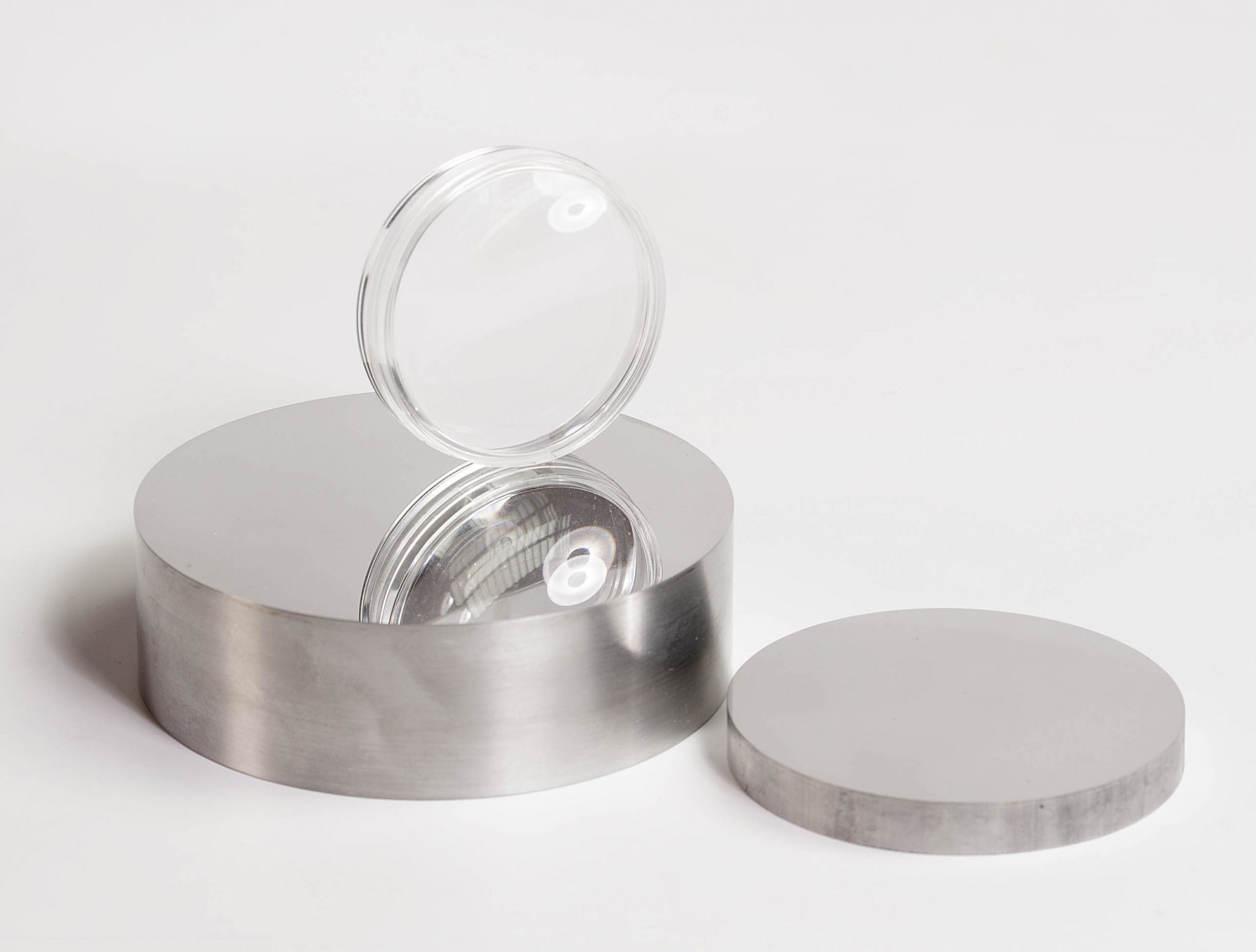
Have you ever thought using RSP technology RSA material for your CNC machining parts?
Netherlands-based RSP Company specializes in the production of high-performance nano-structured aluminum alloys. They offer three primary product grades: RSA-6061, RSA-443, and RSA-905, all widely used in the optical industry.
The advantages like bellow :
Reflective Mirrors: Using the RSA series of microcrystalline aluminum instead of regular 6061 can result in superior surface finish quality. It can increase surface smoothness by a factor of four. RSA-443 can be used as a nickel-plated mirror base, eliminating bimetallic effects. RSA-905, when polished, can achieve an RMS of less than 1nm.
Applications in Molds and Dies: RSA-905 can be directly used as a die without the need for nickel plating or subsequent processing, resulting in a 100% increase in lifespan compared to nickel-plated molds."
RSP aluminum alloys are widely used in aerospace equipment. The distinguishing feature of RSP aluminum alloys is that they can achieve the required precision of reflective surfaces through processing and maintain that precision during use.
In optical systems, reflective mirrors require highly smooth reflecting surfaces. RSP aluminum alloys inherently possess high flatness due to their process characteristics, uniform surface grain structure, and excellent machinability and polishability, making them well-suited to meet the requirements for high smoothness. In space environments, temperature variations can disrupt the thermal balance of mirror bodies, adversely affecting mirror surface shape. RSP aluminum alloys have a low coefficient of thermal expansion, excellent mirror stability, high thermal conductivity, and rapid heat conduction, which help minimize temperature gradients within the mirror body, facilitating quick temperature balance and reducing deformation caused by thermal stress.
Microcrystalline aluminum alloy molds exhibit superior surface quality. They have good machinability, allowing for high-speed cutting, which is 40% faster than that of P20 mold steel and effectively shortens the mold manufacturing cycle. The surface of aluminum alloy molds produced using high-speed machining is smoother than that of steel molds, aiding in demolding. The fine machining capability of aluminum alloy molds simplifies the production of intricate molds. Microcrystalline aluminum alloy has a thermal conductivity four to five times that of steel, resulting in faster heating and cooling, shorter demolding times, lower energy consumption, and significantly increased mold production efficiency. Improved machinability of microcrystalline aluminum alloy also reduces wear on machinery and tools, extending equipment lifespan while reducing labor intensity and improving the working environment for employees.
Mold polishing is time-consuming and costly, with approximately 30% of the total mold manufacturing cost allocated to polishing. High-strength and stable microcrystalline aluminum alloy simplifies the polishing process, achieving mirror-like results quickly. Microcrystalline aluminum alloys are suitable for shielding equipment.
Compared to traditional aluminum alloys, RSP materials offer several advantages. Some microcrystalline aluminum alloys can reach the strength level of titanium, which is heavier, costlier, and more difficult to process. Some alloys are specially designed for components in the sports and racing industries.
The surface roughness of microcrystalline RSP alloys is extremely low, reaching the nanometer level. This remarkably smooth surface allows RSP aluminum to produce optical components (mirrors) and serve as a material for synthetic precision component (lens) molds."
So how about trying this material for your next CNC machining project? For more information please contact danny@opro-tech.com