What is a sub gate? submarine gate or tunnel gate?
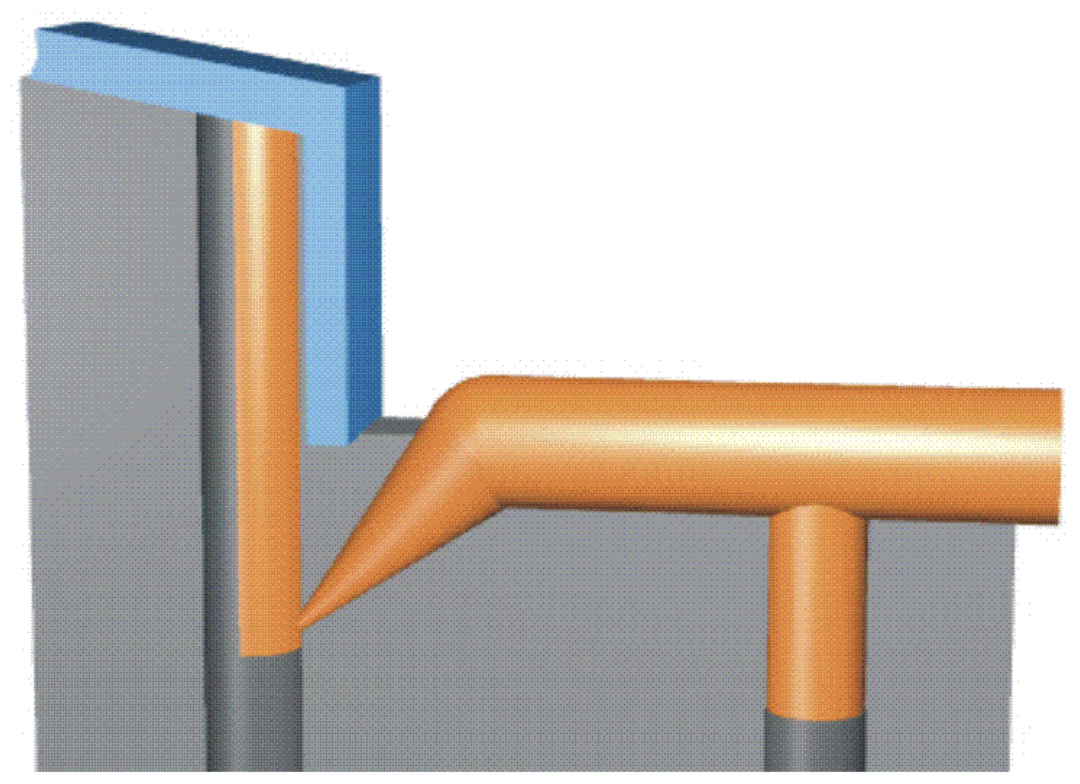
Hello again,
I find the process of creating injection molds and assembling steel pieces to produce intricate plastic parts truly fascinating. Every time I contemplate this journey, it sparks my curiosity. It's amazing how a combination of craftsmanship and technology results in the creation of wonderful products.
Recently, I delved into the intriguing world of injection mold tooling and learned about the types of gate, the sub gate or tunnel gate. Below is my study notes, I know there's still much to learn, but I am committed to enhancing my knowledge, no rush ;) I believe that continuous learning is the key.
A sub gate in tooling mold, also known as a submarine gate, tunnel gate, is a type of gate used in injection molding. It is a small secondary gate that is located below the parting line of the mold. The sub gate is connected to the main runner, which is above the parting line, and it channels the molten plastic directly into the cavity.
Location: Sub gates are positioned beneath the part, often at the bottom of the cavity. This location allows the molten plastic to flow through a tunnel-like structure before entering the mold cavity.
Appearance: The design of sub gates is intended to reduce the visibility of gate marks on the visible surface of the molded part. The gate mark is still present, but it is typically less visible compared to other types of gates.
Advantages:
Aesthetics: Sub gates are chosen when maintaining a high-quality, smooth appearance on the part's surface is crucial. By locating the gate beneath the part, visible gate marks can be minimized.
Use Cases: Sub gates are commonly used in applications where the appearance of the final product is a critical factor, such as in consumer goods or parts with visible surfaces.
The design and selection of the gate type, including sub gates, depend on various factors, including the part's geometry, material properties, and the desired surface finish. The goal is to balance the need for efficient filling of the mold with the requirement for a high-quality appearance in the finished product.
Thank you for being part of this exciting learning experience. If you notice anything that needs correction or have valuable insights to share, please feel free to reach out to me at danny@opro-tech.com. Your input is highly valued.