Have you got experiences about switching gate in your mold design?
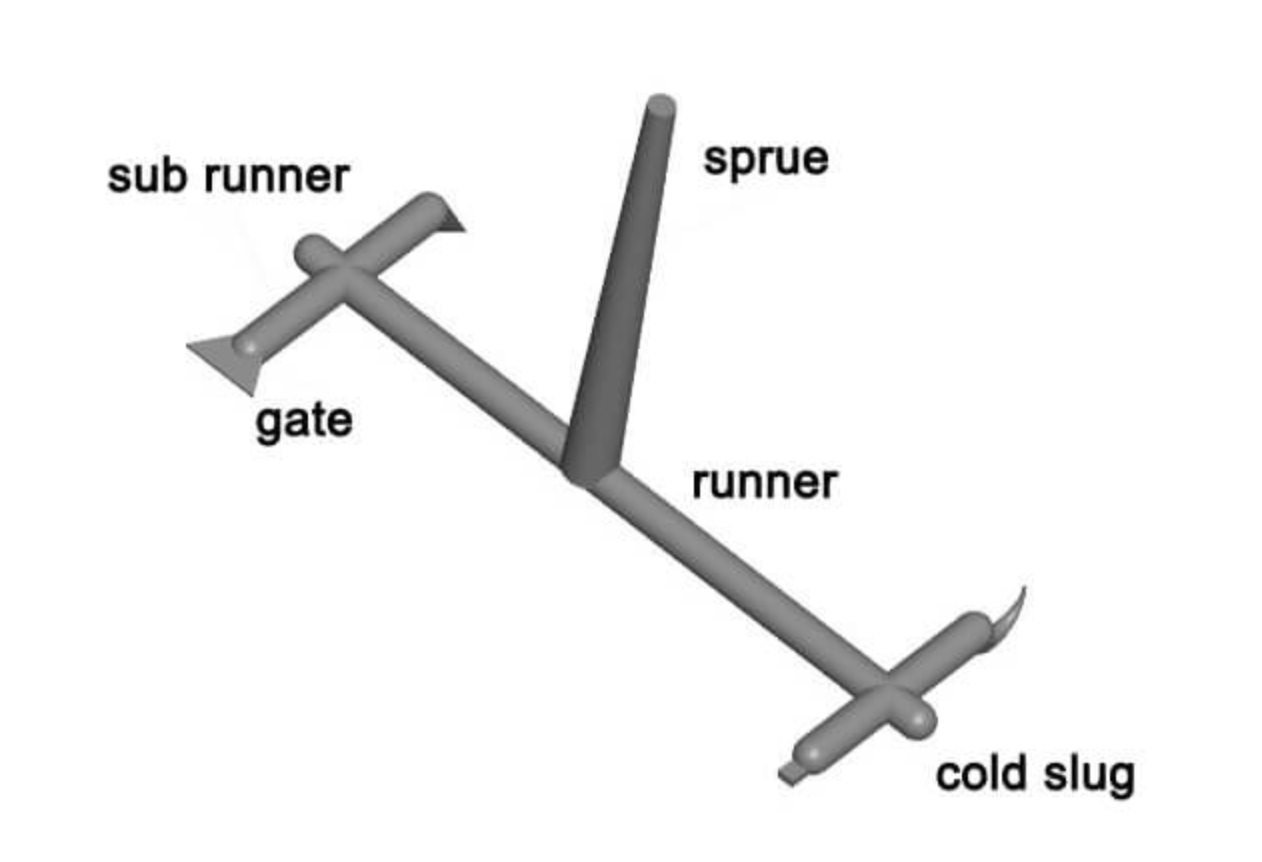
โ โ Have you got experiences about switching gate in your mold design?
๐ค Recently, I conducted some research on switching gates online and discovered limited information available.
Generally, A switching gate in tooling molds, also known as a hot runner switching gate, is a type of gating system used in injection molding. Unlike traditional gating systems, a switching gate allows for the redirection of molten plastic flow between different mold cavities or parts during the injection molding process. This redirection is controlled by a valve mechanism within the hot runner system. ๐ฉโ๐ง
๐ฉโ๐ป If you have hands-on experience or additional knowledge regarding this specific gate design, I would greatly appreciate your insights. Sharing your expertise would be invaluable.
๐ฉโ๐ป Feel free to email me at danny@opro-tech.com with any information or thoughts you'd like to share. Thank you in advance for your time and assistance. ๐โโ๏ธ
๐ Below my study notes for reference.
Advantages of using a switching gate include:
โ โค๏ธ Reduced Scrap: The ability to redirect molten plastic allows for more flexibility in mold cavity filling. If a defect is detected in one cavity, the switching gate can be adjusted to fill other cavities correctly, reducing scrap and improving overall yield.
๐ซ ๐คจ Versatility: Switching gates enable the production of different parts using the same mold. By controlling the flow of plastic, different cavities within the mold can be selectively filled or bypassed, providing versatility in the manufacturing process.
๐ง ๐ Complex Molding: In molds with complex geometries or multiple parts, a switching gate can facilitate the injection of plastic into intricate shapes and configurations. This is particularly useful in applications where different parts require different filling sequences or where sequential filling is necessary.
๐ ๐ Reduced Cycle Time: By optimizing the filling process and reducing the need for cooling time due to scrap reduction, switching gates can contribute to shorter cycle times, enhancing the overall efficiency of the injection molding process.
๐ ๐ Improved Quality: The ability to adjust the flow of plastic in real-time allows for better control over the molding process, resulting in improved part quality and consistency.
๐ ๐ฃ Cost Savings: While the initial setup and implementation of a hot runner switching gate system may involve additional costs, the benefits of reduced scrap, increased efficiency, and improved part quality can contribute to long-term cost savings.
๐ก ๐ก It's important to note that the choice of gating system, including the use of switching gates, depends on the specific requirements of the molding project, part geometry, and desired outcomes in terms of quality and efficiency.
#studynotes #toolingdesign #gatetypes #switchinggate #toolingmolds #toolingsolutions #toolingmoldsolutions #gatevalves #gateway #learnningexperiences