What is Vacuum quenching?
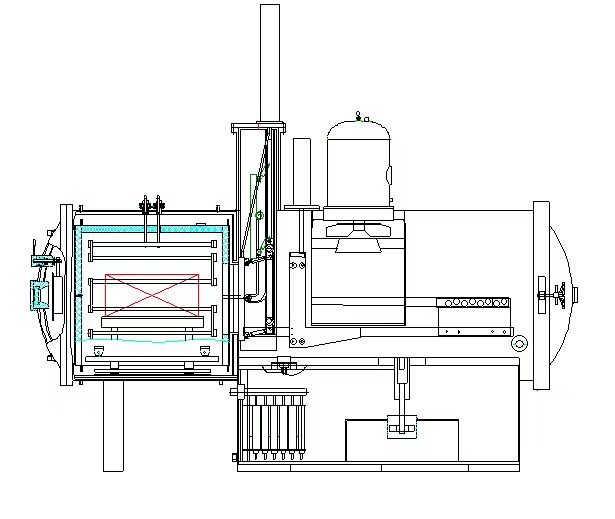
Vacuum quenching is a heat treatment process used in metallurgy to harden and strengthen materials, particularly metals and alloys. The process involves heating the material to a high temperature in a vacuum furnace and then rapidly cooling it by quenching it in a controlled environment with the absence of air or other gases.
The key steps in vacuum quenching include:
Heating: The material is heated to a high temperature in a vacuum furnace. The vacuum environment helps prevent oxidation and contamination of the material's surface.
Soaking: The material is held at the elevated temperature for a specific period, allowing for uniform heating throughout the entire workpiece.
Quenching: After reaching the desired temperature, the material is rapidly cooled by quenching it in a controlled medium, often a high-pressure gas or oil. The rapid cooling is crucial for achieving the desired hardness and strength in the material.
The absence of air in the vacuum furnace during the entire process helps prevent reactions between the material and oxygen, reducing the likelihood of oxidation, scale formation, and surface decarburization. Vacuum quenching is commonly used for hardening various types of steel and other alloys, providing improved mechanical properties and wear resistance.
Advantages:
Oxygen-free Environment: During the vacuum quenching process, the absence of oxygen reduces the risk of oxidation and surface contamination, helping to maintain the surface quality of materials.
Uniform Heating: Through the insulation step, vacuum quenching achieves uniform heating of the entire workpiece, reducing internal stress and deformation.
Precise Control: Vacuum quenching provides more precise temperature control and cooling rates, allowing for highly customized material properties.
Reduced Deformation: Compared to some traditional quenching methods, vacuum quenching often reduces the risk of workpiece deformation, helping to maintain the stability of geometric shapes and dimensions.
Disadvantages:
High Equipment Cost: Vacuum quenching equipment is relatively expensive, which may pose a challenge for businesses looking to adopt this technology.
High Energy Consumption: The heating and insulation steps require a significant amount of energy, resulting in higher energy costs for vacuum quenching.
Limited Applicability: Not all materials are suitable for vacuum quenching, so its application is subject to limitations imposed by certain materials and processes.
Small Processing Capacity: Vacuum quenching is typically suitable for relatively small workpieces, and the processing of large workpieces may be limited.
This process is favored for its ability to produce precise and consistent results, reducing the risk of distortion and maintaining tight tolerances on the treated components. Vacuum quenching is widely employed in industries such as aerospace, automotive, and tool manufacturing where precise control over material properties is essential.