Understanding 3.3547 (AA5083) Aluminum Alloy: Properties, Applications, and Machining Considerations
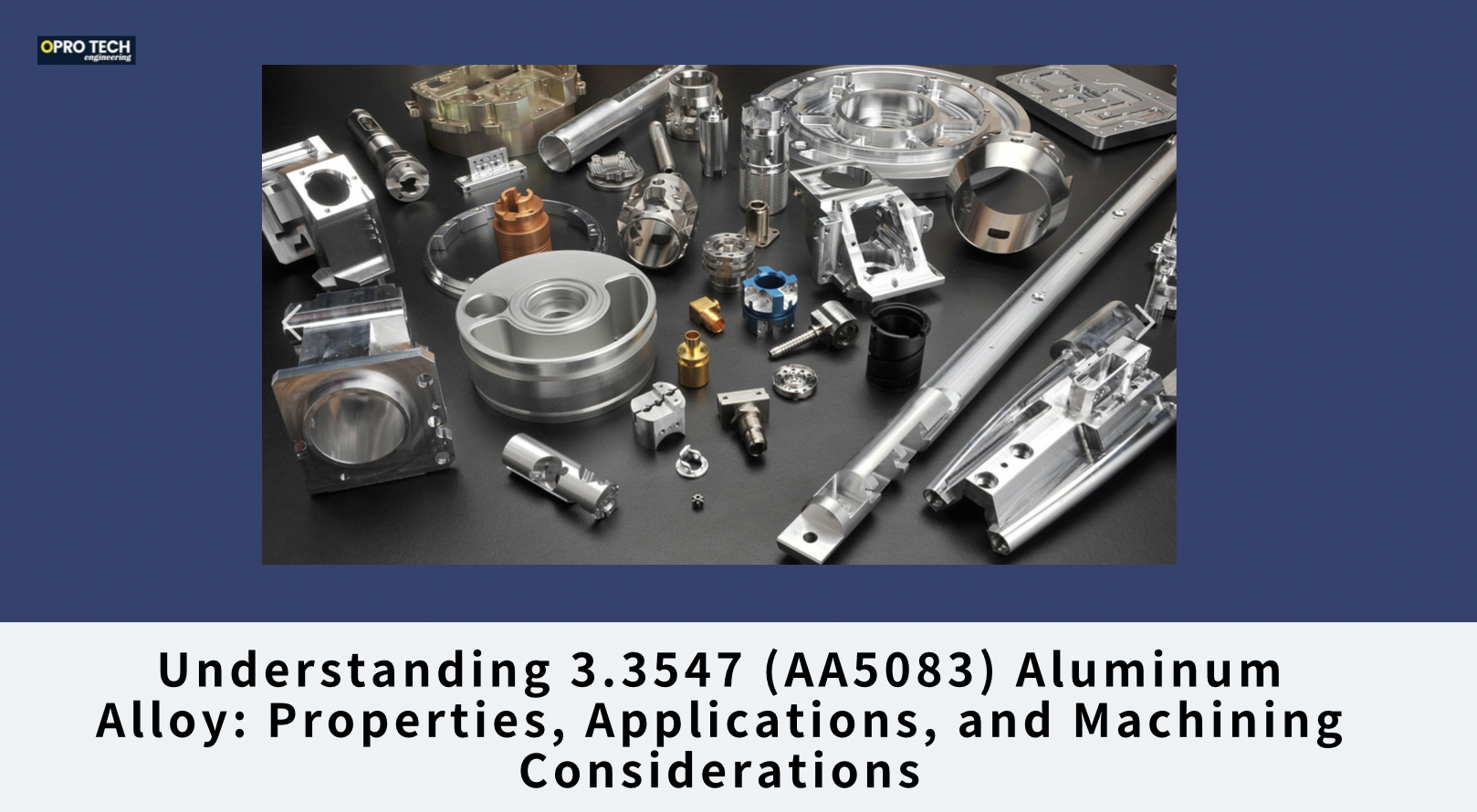
3.3547 (AA5083) is a widely used aluminum alloy recognized for its exceptional strength, corrosion resistance, and durability in harsh environments. With a high magnesium content of around 4.5%, this alloy is particularly favored in industries like marine engineering, automotive manufacturing, and aerospace, where lightweight materials must also withstand extreme conditions.
However, the high magnesium content also introduces unique challenges during machining, particularly due to the flammability of magnesium chips. In this article, we will explore the key properties, common applications, and crucial safety considerations when machining 3.3547, ensuring you maximize its potential while mitigating risks.
the material 3.3547 refers to an aluminum alloy known as AlMg4.5Mn0.7 or AA5083 in international standards. It is commonly used in industries where high strength, corrosion resistance, and good weldability are important, such as shipbuilding, automotive, and CNC machining industries.
Key properties of 3.3547 / AA5083:
- High corrosion resistance, especially in marine environments.
- Good strength-to-weight ratio.
- Excellent weldability, making it ideal for applications where welding is required.
- Good machinability, though it may not be as easy to machine as some other aluminum alloys like 6061.
In CNC machining, 3.3547 is frequently used for components that require both high strength and resistance to harsh environments, such as:
- Marine parts
- Pressure vessels
- Structural applications
- Automotive panels and parts
Here are some key points regarding machining aluminum alloys with high magnesium content:
- Magnesium Content and Flammability Risk:
- While 3.3547 is primarily aluminum, it contains 4.5-5% magnesium. Magnesium is highly flammable, especially when it forms fine chips or dust during machining. However, aluminum alloys like AA5083 do not pose as high a risk as pure magnesium due to the lower percentage of magnesium.
- Fire Risk During Machining:
- The fire hazard occurs when magnesium chips are very fine or accumulate in large quantities. These can ignite due to the heat generated during high-speed machining.
- Pure magnesium is more likely to catch fire, but alloys like 3.3547 can also present a fire risk if not handled carefully.
- Safety Measures During CNC Machining:
- Coolant Use: Use flood coolant or a mist to keep the material and tools cool. This helps to prevent the build-up of heat that could lead to ignition.
- Chip Management: Ensure that chips are removed quickly and efficiently to avoid any risk of ignition due to friction or heat build-up. Vacuum systems or continuous air blowing can help.
- Tool Speed and Feed: Moderate cutting speeds and feed rates are important to prevent the heat from reaching a point where chips could ignite.
- Fire Extinguishers: Keep Class D fire extinguishers (for metal fires) nearby, as water-based or regular extinguishers will not be effective for magnesium fires.
- Avoid Dry Machining: Dry machining of high-magnesium aluminum alloys increases the fire risk significantly, so using coolant is critical.
- Machining Characteristics:
- 3.3547 can be machined relatively well with proper cooling and chip management.
- The magnesium content contributes to better machinability compared to some other aluminum alloys, but care must be taken to avoid overheating, which could cause tool wear or fire hazards.
In summary, while AA5083 (3.3547) is not as dangerous to machine as pure magnesium, the magnesium content still requires careful attention to cooling and chip management to avoid potential fire hazards. Proper precautions in CNC machining can mitigate most of these risks.
3.3547 (AA5083) remains a versatile and high-performing material across numerous industries, thanks to its excellent strength-to-weight ratio and corrosion resistance. However, understanding the intricacies of machining this aluminum alloy, especially the fire risks associated with its magnesium content, is vital for safe and efficient processing.
By implementing proper cooling, chip management, and adhering to safety protocols, manufacturers can unlock the full benefits of this alloy while maintaining a safe working environment. Whether for marine applications or high-performance automotive parts, 3.3547 continues to be a reliable choice in demanding environments.
Factory add: No 39, Zhen an west road, Changan town , Dong guan city, China.