What is Pre-Deformation in Tooling Mold Design?

Pre-deformation is a technique used in mold design where specific areas of a part are intentionally distorted or offset during the tooling design phase to compensate for predictable deformations that will occur during injection molding. This method ensures that the final molded part meets the required dimensional and geometric tolerances.
Pre-deformation is commonly applied in projects where materials and processing conditions lead to significant warpage, shrinkage, or stress-induced deformation.
Why is Pre-Deformation Needed?
Several factors influence the need for pre-deformation in mold design:
- Material Shrinkage Compensation
- Thermoplastics like PA66+GF30 (Nylon with 30% Glass Fiber), POM, or PP shrink during cooling.
- Semi-crystalline plastics generally have higher shrinkage rates than amorphous plastics, requiring compensation.
- Fiber-reinforced plastics shrink anisotropically, meaning they shrink differently along and perpendicular to the fiber orientation.
- Warpage and Distortion Prevention
- Uneven cooling, non-uniform wall thickness, and residual stresses can cause the part to warp after ejection.
- Without pre-deformation, parts may twist, bow, or curve, leading to out-of-spec products.
- Part Functionality & Assembly Fit
- Some parts require high precision to fit with other components. If deformations occur post-molding, they won't assemble correctly.
- For example, automotive connectors, electronic enclosures, or optical lenses often require pre-deformation to maintain tight tolerances.
- Eliminating Post-Molding Corrections
- If deformation is not accounted for in the mold, secondary post-processing steps (such as heat treatment, machining, or fixture-based correction) may be needed, increasing cost and cycle time.
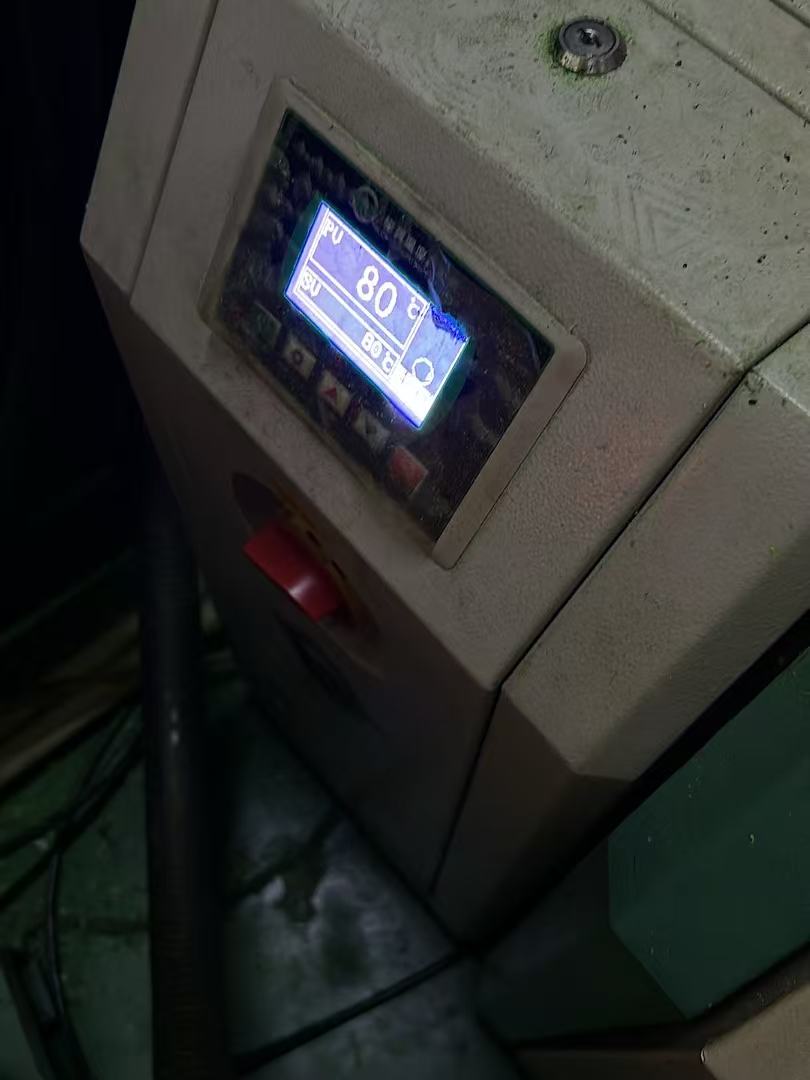
How is Pre-Deformation Applied?
The pre-deformation process involves simulating and adjusting the mold cavity geometry to counteract predicted deformations. This is done using several key methods:
1. CAE Mold Flow Analysis & Warpage Simulation
- Software like Moldflow, Moldex3D, or Simpoe-Mold is used to predict shrinkage and warpage.
- The simulation considers fiber orientation, gate locations, cooling rate, and material properties to determine distortion patterns.
- The mold designer then modifies the CAD model to offset this expected deformation.
2. Pre-Deformation in CAD Modeling
- The mold cavity is intentionally designed with a counter-deformed shape.
- Example: If a flat part is expected to bend upwards, the mold cavity will be designed with a slight downward curvature to compensate.
3. Adjusting Mold Components
- Core and cavity adjustments: In multi-part molds, one side may be pre-deformed to balance the warping effect.
- Gate and runner positioning: Proper placement can minimize asymmetric shrinkage.
- Cooling channel optimization: Uniform cooling prevents uneven contractions.
4. Empirical Testing and Iteration
- After initial production, real-world testing is performed.
- The mold is fine-tuned iteratively based on measured deviations.
Real-World Applications of Pre-Deformation
- Automotive Parts (Bumper, Instrument Panels)
- Large plastic components often suffer from warpage due to differential cooling.
- Pre-deformation ensures final shape accuracy.
- Thin-Walled Enclosures (Consumer Electronics, IoT Devices)
- Small changes in material thickness can cause warping.
- Pre-deformed designs compensate for shrinkage.
- Medical & Optical Components (Lenses, Precision Frames)
- Any warpage can severely affect optical clarity and functionality.
- CAE-based pre-deformation is essential.
- Gears and Mechanical Parts (POM, PA66+GF)
- High precision is needed for gear engagement.
- Pre-deformation ensures proper tooth alignment.
Key Takeaways
- Pre-deformation is a critical mold design strategy to compensate for shrinkage, warpage, and stress deformation.
- It relies heavily on CAE simulation, material science, and iterative mold tuning.
- Used in high-precision industries, including automotive, electronics, medical, and mechanical components.
- Helps in reducing production defects, eliminating post-processing corrections, and improving overall dimensional accuracy.
Dan
Factory add: No 39, Zhen an west road, Changan town , Dong guan city, China.