Electric vs. Hydraulic Injection Molding Machines: A Complete Comparison
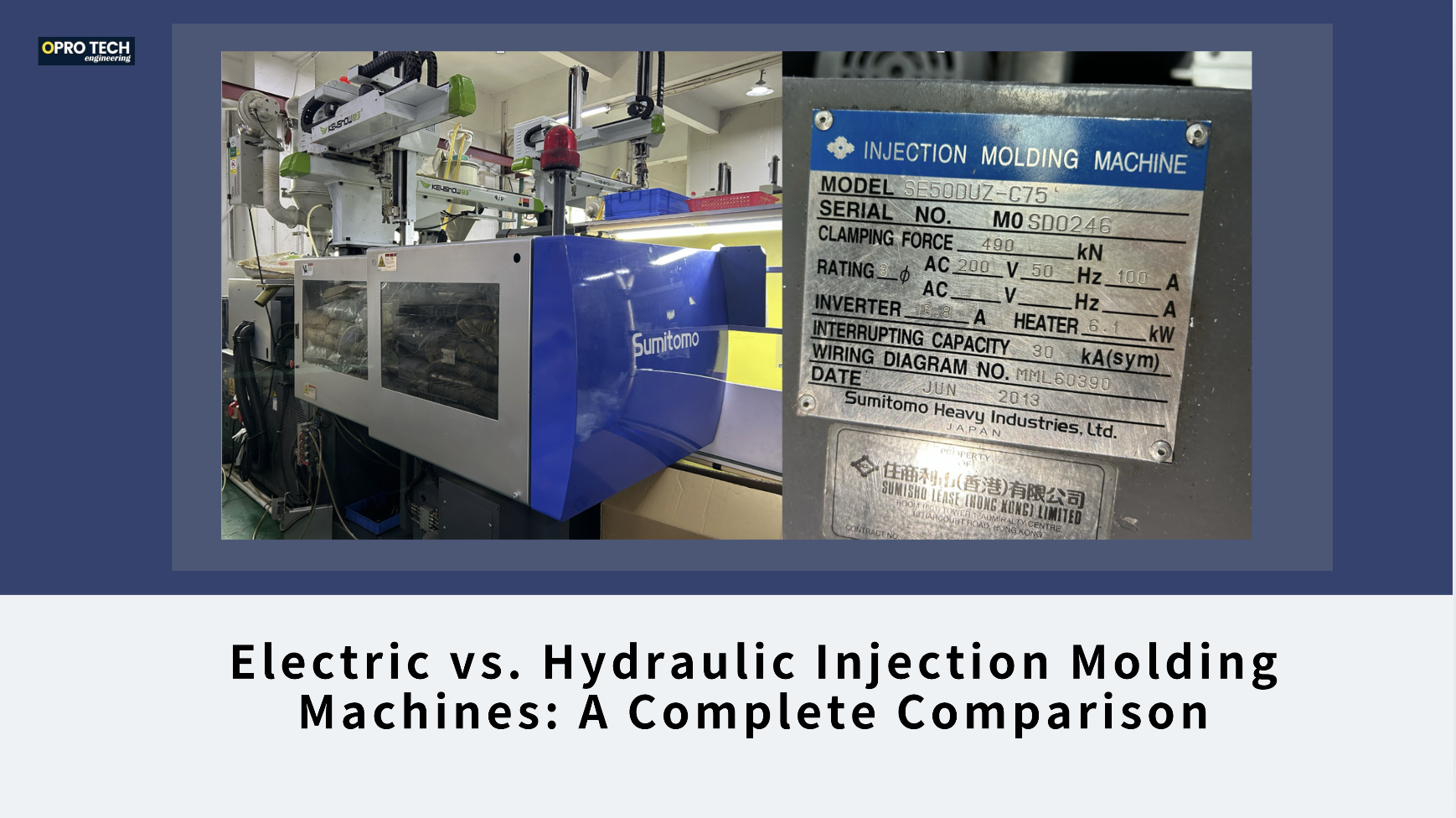
1. Electric Injection Molding Machine (All-Electric)
An Electric Injection Molding Machine is fully driven by servo motors. All main movements, including mold opening/closing, injection, and ejection, are powered by electric motors through ball screws, without using hydraulic oil.
🔑 Key Features:
- High Precision: Excellent for producing high-precision parts with tight tolerances, such as medical, electronic, and optical components.
- Fast Cycle Time: Faster response and injection speed due to precise motor control, leading to shorter production cycles.
- Energy Efficiency: Motors only consume energy when operating, significantly reducing power consumption compared to hydraulic machines.
- Clean Production: No hydraulic oil means a cleaner and environmentally friendly process, ideal for cleanroom production.
- Low Noise: Quiet operation, suitable for environments with noise restrictions.
✅ Best for:
- High-precision and small-sized parts.
- Thin-wall products.
- Medical, electronics, and food packaging industries.
- Cleanroom production.
2. Hydraulic Injection Molding Machine
A Hydraulic Injection Molding Machine is powered by hydraulic pumps and cylinders that drive all the machine’s movements, including mold opening/closing, injection, and ejection. These machines use hydraulic oil to transmit power.
🔑 Key Features:
- Strong Injection Force: High injection pressure, suitable for molding large, complex, and thick-wall products.
- Lower Initial Investment: Generally more affordable to purchase compared to electric machines.
- Durable and Powerful: Suitable for large-scale production of bulky parts that do not require extreme precision.
- Widely Used: Common in automotive, household, and industrial part manufacturing.
⚙️ Considerations:
- Higher Energy Consumption: Hydraulic pumps run continuously, leading to higher power usage.
- Maintenance: Requires regular maintenance of hydraulic oil and components.
- Noise & Cleanliness: More noise and potential oil leakage issues compared to electric machines.
✅ Best for:
- Large and thick-walled parts.
- Automotive and industrial components.
- General-purpose plastic products where ultra-high precision is not necessary.
- Cost-sensitive production.
✅ Conclusion: Which One to Choose?
· Choose Electric Injection Molding Machine if:
- You need high precision and repeatability.
- Producing small, thin-wall, or high-value parts.
- Operating in cleanroom or medical-grade environments.
- Long-term energy savings and low maintenance are priorities.
· Choose Hydraulic Injection Molding Machine if:
- You are producing large, thick-wall parts (e.g., automotive, industrial).
- Budget is limited for initial investment.
- High injection pressure is required for complex molds.
Dan
Business development manager
Phone: +86 134 1699 5669
Skype: danny@opro-tech.com
Factory add: No 39, Zhen an west road, Changan town , Dong guan city, China.
Factory add: No 39, Zhen an west road, Changan town , Dong guan city, China.
Injection Mold / CNC Machining / 3D Printing / Prototyping / Sheet Metal