Why is the plastic products more difficult to process in machining?
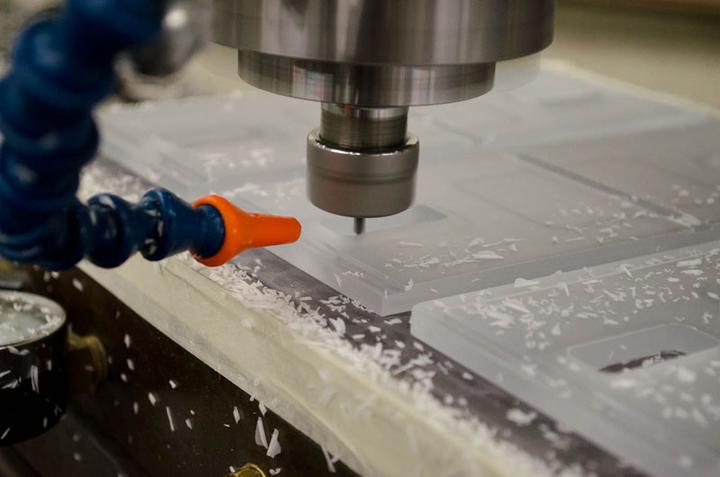
Today I was browsing LinkedIn and found such a topic. A buyer sent an inquiry to a supplier about a plastic product, but the supplier said: We cannot quote. Using our usual production methods, it may cause Burnt plastic. So I was wondering if all plastic materials are challenging to machine. Based on our company's past production, the plastic materials I know are: PA, PEEK, POM, PVC, ABS. And they come in different colors.
Then I started searching on the Internet about the difficulty of plastic machining, and then I learned that plastic machining is full of challenges. Judging from one of the properties of plastic itself: thermal sensitivity, hardness, and stickiness. Adhesion, wear resistance, etc.
Thermal sensitivity: High-performance plastics such as PEEK are temperature-sensitive and are easily affected by high temperatures and deformed. Temperature needs to be controlled during machining to avoid material performance degradation caused by overheating.
Hardness: PEEK is relatively hard, which can make chipping and cutting more challenging. Proper selection of tool materials and cutting parameters is crucial to obtain high-quality machined surfaces.
Adhesion: Some plastics may produce chips during machining, and these chips may adhere to the processing surface, affecting the processing quality. Appropriate treatment methods such as cooling, chip removal, etc. need to be taken.
Wear Resistance: These high-performance plastics often have high wear resistance, which can cause the tool to wear out more quickly. Regular tool replacement and maintenance is key to ensuring stable processing.
But products made from plastic are very common in our daily lives, so how do they overcome these difficulties?Maybe it would be better to use 3D printing technology for production?