Hot-Dip Galvanizing vs. Cold Galvanizing
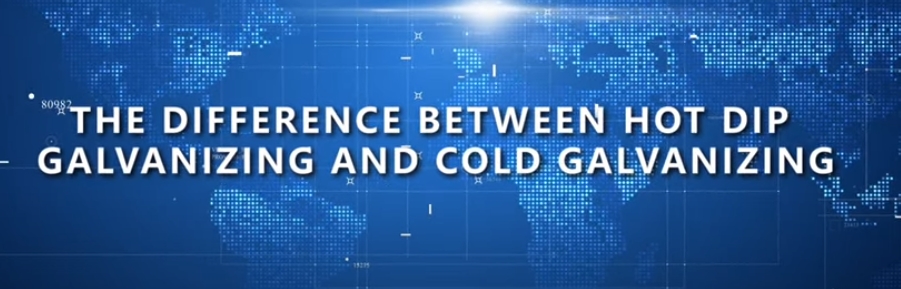
In industrial production, hot-dip galvanizing and cold galvanizing are two common corrosion prevention techniques. They employ different methods to protect the metal surface, each having its own characteristics and suitable applications. Below, we will provide a detailed comparison of these two techniques.
1.Process Principles:
Hot-Dip Galvanizing: Also known as hot-dip immersion galvanizing, it is an effective method of metal corrosion prevention. Zinc ingots are melted at high temperatures, mixed with auxiliary materials, and then metal structural components are immersed in the galvanizing bath, allowing a layer of zinc to adhere to the metal surface, thus achieving corrosion resistance.
Cold Galvanizing: Also known as electro-galvanizing, it utilizes electrolysis to attach a metallic film to the surface of metal or other material components. This process creates a uniform, dense, and well-bonded metal layer, preventing corrosion, enhancing wear resistance, conductivity, reflectivity, and improving aesthetics.
2.Coating Characteristics:
Hot-Dip Galvanizing: The coating applied through hot-dip galvanizing is relatively thick, usually providing robust corrosion resistance. This makes hot-dip galvanizing particularly suitable for large structures such as steel constructions and pipelines.
Cold Galvanizing: The coating applied through cold galvanizing is relatively thin, making it suitable for small components like screws and nuts. Despite its thinner coating, cold galvanizing excels in treating intricate shapes.
3.Application Scenarios:
Hot-Dip Galvanizing: Suitable for outdoor steel components, such as highway guardrails, power transmission towers, and large-sized fasteners, requiring long-term rust prevention. Older iron water pipes are also hot-dip galvanized.
Cold Galvanizing: Used for indoor components, such as machine casings, panels, small-sized fasteners, and metal parts.
4.Process Differences:
Hot-Dip Galvanizing: The workpiece is degreased, acid-pickled, immersed in a zinc solution after being coated with auxiliary materials, and then removed after a certain time.
Cold Galvanizing: The workpiece undergoes degreasing and acid-pickling before being placed in a solution containing zinc salts using electrolytic equipment. The workpiece is connected to the negative pole of the electrolytic equipment, while a zinc plate, connected to the positive pole, is placed opposite the workpiece. When the power is turned on, zinc is deposited on the workpiece.
5.Price Difference:
Generally, the cost of hot-dip galvanizing is lower than applying other protective coatings. This is mainly due to the labor-intensive nature of processes like sandblasting and painting, while hot-dip galvanizing involves highly mechanized and closely controlled in-house construction.
Cold galvanizing can be applied to only one side, while hot-dip galvanizing requires full coverage. Additionally, the zinc layer applied in hot-dip galvanizing is usually thicker, leading to a higher cost compared to cold galvanizing.
6. Differences between galvanized finished products
Differences in galvanized finished products: The surface of hot-dip galvanizing is not as delicate and bright as cold-dip galvanizing, and the coating is uniform. However, the thickness of the zinc layer is dozens of times that of cold-dip galvanizing. The anti-corrosion performance is also dozens of times that of electroplated zinc.
In conclusion, hot-dip galvanizing and cold galvanizing each have their strengths and weaknesses in the field of corrosion prevention. The choice between the two depends on specific application scenarios and requirements. In practical applications, a comprehensive consideration of factors such as material, shape, and environmental conditions is crucial to ensure optimal corrosion prevention effects.