Threaded Holes: A Console's Way to Connect the World
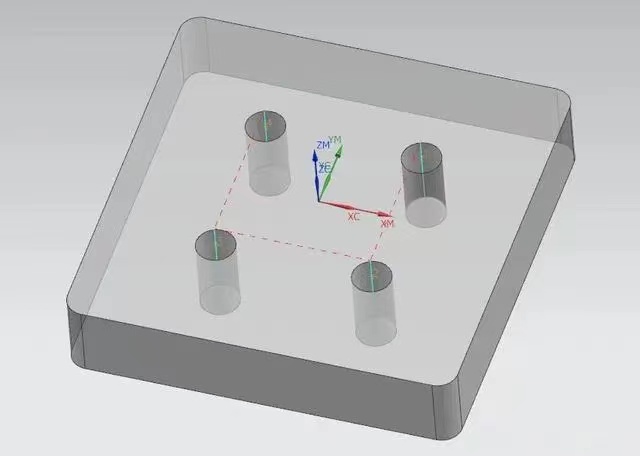
Threaded holes are indispensable components in a variety of engineering applications, providing a universal method of connecting and securing parts in an assembly. This manuscript explores the importance of threaded holes, their design considerations, and their diverse applications across industries. From aerospace to automotive, threaded holes play a vital role in ensuring structural integrity, facilitating efficient assembly processes, and enabling complex system integration.
Types of threaded holes:
Making a successful threaded hole depends on several key parameters, including the characteristics of the material being processed, the properties of the hole, and several other explanatory factors:
1. Material Hardness:The harder the material, the greater the force required for drilling and tapping operations. For example, when drilling holes in hardened steel, you can use taps made of hard alloy because they have high heat resistance and wear resistance.
2. Maintaining Standard Thread Sizes:The thread sizes you use can affect the entire threading process. These standard sizes make it easy to accurately fit threads into parts.
3.Ensuring Optimal Hole Depth:Achieving the desired hole depth can be difficult, especially for blind holes (due to lower accessibility, through holes are easier). Therefore, you need to reduce cutting speed or feed rate to prevent drilling too deep or not deep enough.
4.Choosing the Right Machinery:
Using the correct tools can determine the success of any manufacturing process.
Forming taps: Unlike cutting taps, they roll material to form threads. As a result, no chips are formed, and the process is highly efficient. Additionally, it's suitable for threaded parts made of soft materials such as aluminum and brass.
5.Beveled Surfaces:When working on surfaces with angles, tap tools may slip or break because they cannot withstand bending stress. Therefore, extra care should be taken when dealing with angled surfaces. For example, when dealing with angled surfaces, you should mill grooves to provide the necessary flatness for the tool.
6.Proper Positioning:Threads should appear in the correct position to achieve an efficient and effective process. Threading positions can be anywhere, such as in the middle and near the edge. However, extra caution should be taken when threading near the edge, as errors in the threading process can damage the surface finish of the part and the tap tool.
Applications:
1.Aerospace Industry
2.Automotive Engineering
3 Electronics and Consumer Goods
Threaded holes are indispensable elements in modern engineering, facilitating the assembly, integration, and operation of diverse mechanical systems. By adhering to sound design principles, employing advanced manufacturing techniques, and leveraging innovative materials, engineers can harness the full potential of threaded holes to achieve optimal performance, reliability, and efficiency across a broad spectrum of applications.