Turning Raw Prints into Polished Products: The Art of 3D Printing
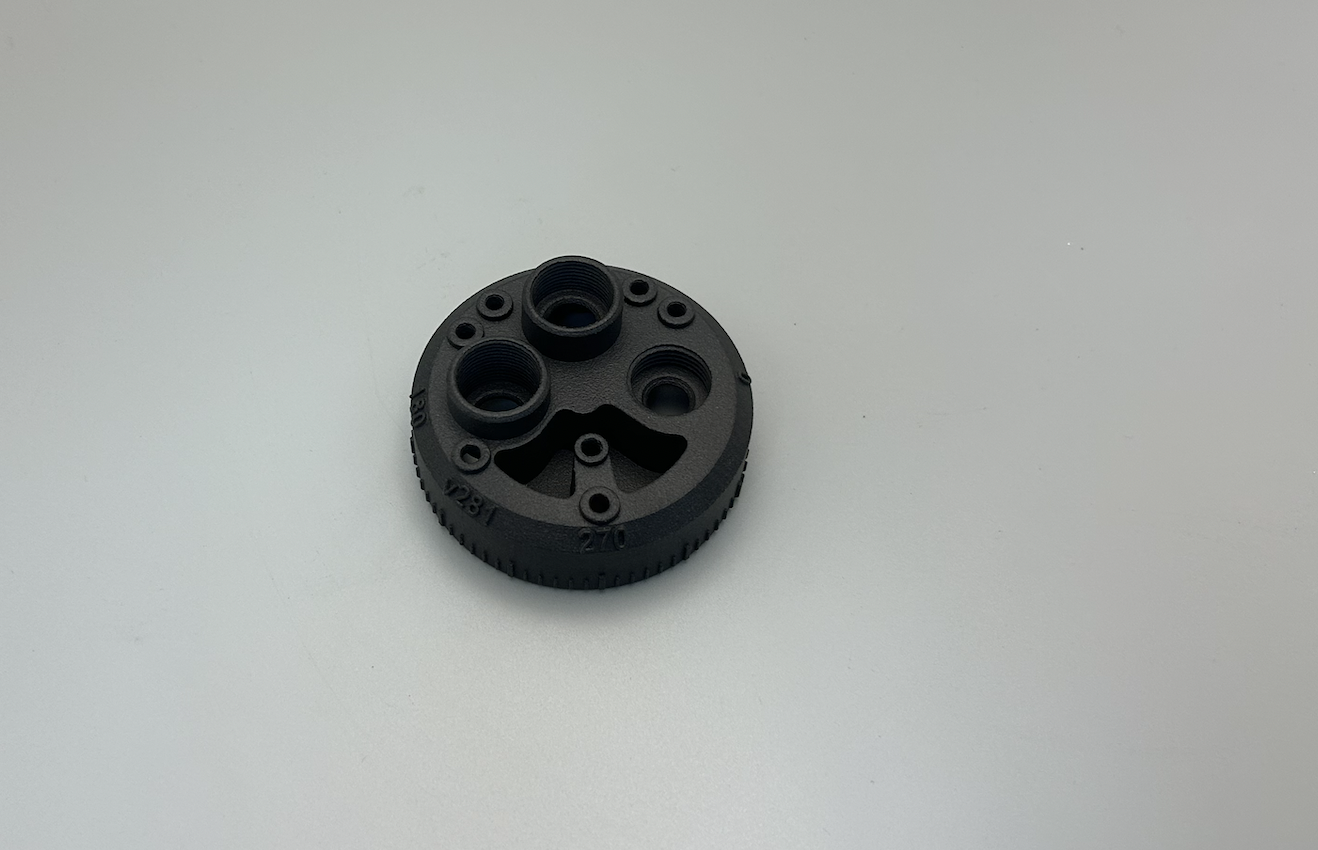
Discover the future of manufacturing with cutting-edge 3D printing technologies. From intricate designs to rapid prototyping, these methods revolutionize the way we bring ideas to life, offering precision and versatility like never before.
Hello, I'm Dan, Market Development Manager at Opro-tech engineering. In our role, we believe in not only being sales professionals but also continually enhancing our technical expertise. We strive to learn and share insights gained through our experiences, aiming to provide valuable information that you may find helpful in your endeavors.
Today we are going to share something about 3D printing. First let’s look at the advantages of 3D printing.
Advantages of 3D Printing Over Plastic Injection Molding
1. Speed and Turnaround Time
- Rapid Prototyping: 3D printing allows for the rapid creation of prototypes directly from digital models, significantly reducing the time from design to physical part. This is particularly beneficial in the early stages of product development.
- Quick Iterations: Design changes can be implemented and produced almost immediately without the need for costly and time-consuming mold alterations.
2. Cost-Effectiveness for Low Volumes
- No Mold Costs: Unlike injection molding, which requires expensive molds, 3D printing doesn’t need any tooling. This makes it highly cost-effective for low-volume production runs or one-off custom parts.
- Lower Initial Investment: The initial setup cost for 3D printing is generally much lower than that for injection molding, making it accessible for smaller projects or startups.
3. Design Flexibility and Complexity
- Complex Geometries: 3D printing can produce intricate and complex geometries that might be impossible or too costly to achieve with injection molding. This includes internal structures, undercuts, and hollow sections.
- Customization: Each part can be easily customized without additional costs, which is ideal for personalized products or custom-fit components.
4. Material Versatility
- Wide Range of Materials: 3D printing supports a diverse range of materials, including plastics, metals, ceramics, and composites. This allows for a broader selection of material properties to suit specific applications.
- Advanced Materials: New materials with unique properties, such as biocompatibility, high strength, or flexibility, are continually being developed for 3D printing.
5. Reduced Waste
- Additive Process: 3D printing is an additive manufacturing process, which means material is only used where needed. This results in less waste compared to the subtractive nature of machining or the excess material from injection molding runners and sprues.
6. On-Demand Production
- Inventory Reduction: Parts can be printed on demand, reducing the need for large inventories and associated storage costs. This can be particularly beneficial for spare parts or components with unpredictable demand.
- Localized Manufacturing: 3D printing enables localized production, reducing the need for long supply chains and lowering shipping costs and lead times.
7. Sustainability
- Eco-Friendly: By reducing material waste and enabling the use of eco-friendly materials, 3D printing can contribute to more sustainable manufacturing practices.
- Energy Efficiency: Some 3D printing processes consume less energy compared to traditional manufacturing methods.
While plastic injection molding is highly efficient for large-scale production and offers excellent repeatability and material properties, 3D printing excels in flexibility, speed, and cost-effectiveness for low-volume, complex, and customized parts. The choice between the two methods depends on the specific requirements of the project, including volume, design complexity, and production timelines.
Now we are going to share you the top 5 main types of 3D printing technologies that we can do .
SLA (Stereolithography):
Imagine a 3D printer creating objects layer by layer using a liquid resin that hardens when exposed to ultraviolet light. That's SLA for you! It's perfect for intricate, detailed models and prototypes, making it a go-to for industries like jewelry design and dentistry.
SLM (Selective Laser Melting):
Now, picture a laser melting and fusing metal powder to build up a solid 3D structure. That's the magic of SLM, a powerhouse in the world of metal 3D printing. Its applications extend to aerospace, healthcare, and automotive industries, crafting parts with precision.
SLS (Selective Laser Sintering):
SLS takes powdered materials, like nylon or polyamide, and uses a laser to selectively fuse them, layer by layer. This versatile technique is a go-to for creating functional prototypes, end-use parts, and even intricate geometries that would challenge traditional manufacturing.
MJF (Multi Jet Fusion):
Imagine a 3D printer jetting liquid binding agents and fine powders layer by layer, followed by a heating and fusing process. That's Multi Jet Fusion, known for its speed and precision. It's a game-changer for producing functional prototypes and end-use parts with exceptional detail.
DLP (Digital Light Processing):
DLP utilizes a digital light projector to flash entire layers of a 3D object at once, solidifying a liquid resin. It's quick and effective, making it ideal for industries requiring rapid prototyping, such as consumer electronics and healthcare.
In the dynamic landscape of 3D printing, these technologies are shaping the way we design, prototype, and manufacture. Whether it's the precision of SLA, the metal prowess of SLM, the versatility of SLS, the speed of MJF, or the efficiency of DLP, each method adds its unique flavor to the incredible palette of additive manufacturing.
The Importance of Post-Processing in 3D Printing
When embarking on a 3D printing project, it is essential to understand that the journey does not end when the parts emerge from the printer. While 3D printing offers unparalleled design flexibility and rapid prototyping capabilities, the initial output often requires significant refinement to achieve the desired quality and aesthetics. This is where the expertise of skilled craftsmen and advanced post-processing techniques become crucial.
Skilled Craftsmanship: Turning Rough Prints into Masterpieces
3D printed parts typically come out of the machine with a rough surface finish and visible layer lines. These imperfections need to be meticulously addressed to meet the high standards of functionality and appearance. Skilled craftsmen play an indispensable role in this process, bringing their experience and precision to the table. Their tasks often include:
- Sanding and Smoothing: Carefully sanding down rough surfaces to achieve a smooth, uniform finish.
- Polishing: Enhancing the surface shine and smoothness through various polishing techniques.
- Detailing: Adding intricate details that might not have been captured fully during the printing process.
Advanced Post-Processing Technologies
In addition to manual craftsmanship, several advanced post-processing technologies are employed to refine 3D printed parts:
- Surface Treatment: Techniques such as vapor smoothing or chemical polishing can be used to dissolve surface imperfections and achieve a glossy finish.
- Painting and Coating: Applying primer, paint, or protective coatings to enhance the appearance and durability of the parts.
- Assembly and Finishing: For multi-part assemblies, ensuring precise fit and finish through careful alignment and bonding.
The Result: High-Quality, Aesthetic Products
The combination of skilled handcrafting and advanced post-processing transforms rough 3D printed items into high-quality, aesthetically pleasing products. This meticulous refinement ensures that the final parts not only meet but often exceed, the original design specifications in terms of both form and function.
In the world of 3D printing, the post-processing phase is as important as the printing itself. It is this stage that bridges the gap between raw, rough prints and polished, market-ready products. By investing in skilled craftsmanship and utilizing advanced post-processing technologies, we can ensure that every 3D printed item achieves its full potential, delivering exceptional quality and beauty.
At Opro-tech Engineering, we understand that the true potential of 3D printing is realized through meticulous post-processing and skilled craftsmanship. Our commitment to quality ensures that every 3D printed item is refined to perfection, meeting the highest standards of functionality and aesthetics.
We invite you to experience the exceptional quality and precision that Opro Tech Engineering offers. Whether you need rapid prototypes or high-quality finished products, our team is ready to bring your vision to life. Contact us today to discuss your 3D printing projects and discover how we can help you achieve outstanding results.
Send us your inquiries and let's embark on a journey of innovation and excellence together.
Dan
Business development manager
Phone: +86 134 1699 5669
Skype: danny@opro-tech.com
Factory add: No 39, Zhen an west road, Changan town , Dong guan city, China.
Injection Mold / CNC Machining / 3D Printing / Prototyping / Sheet Metal