The common prototype manufacturing methods
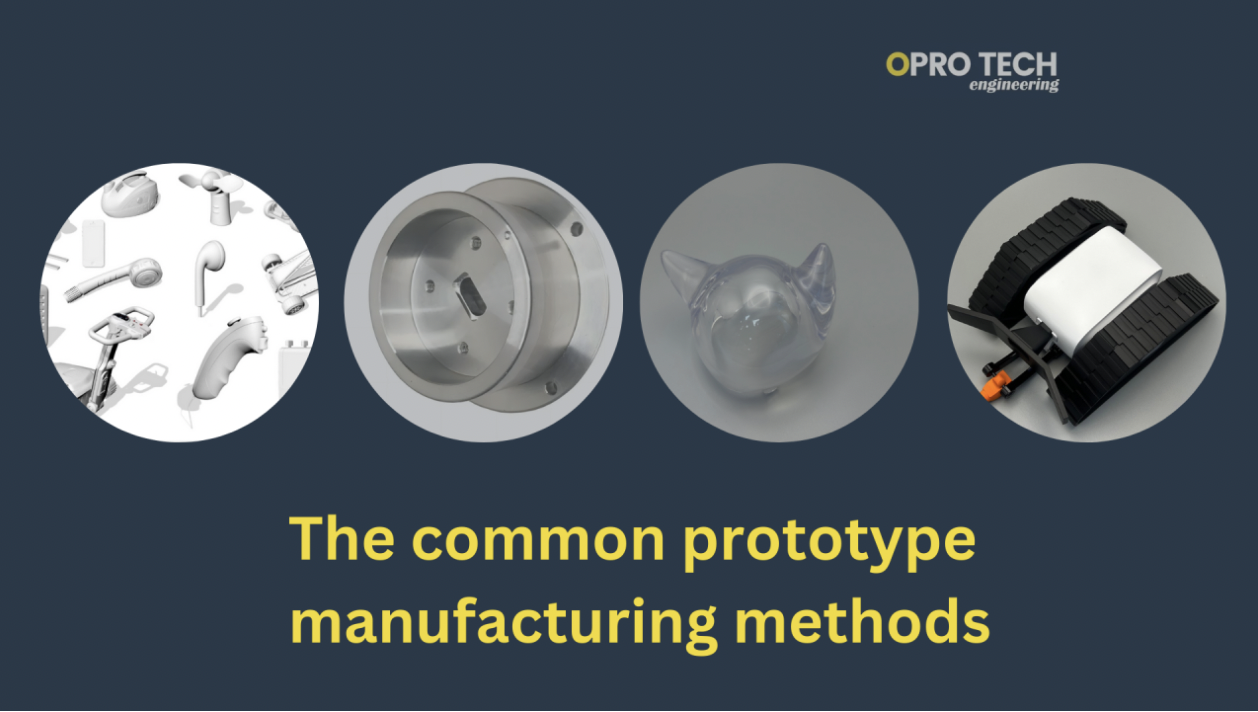
1. CNC Machining Prototype
CNC machining is a common method for creating prototypes.
Its advantages include high precision and a refined appearance, making it suitable for products that require a certain level of quality.
The process starts with a 3D design, which is either split into parts for individual machining or processed as a whole.
Most CNC machines used for prototype manufacturing are 3-axis machines. Complex workpieces may need to be divided into sections, machined separately, and then manually assembled, since a 3-axis machine can only process one surface at a time.
For example, a bottle with a small neck and a large body needs to be split into two parts for machining and then joined together.
CNC machining can handle various materials, such as ABS, PC, PMMA, POM, PP, PA66, PPS, flame-retardant ABS, ABS+PC, PC+GF, aluminum alloy, brass, stainless steel, iron, and more.
This method is suitable for products that require high material toughness, large size, and high precision.
2. 3D Printing Rapid Prototyping
With the development of 3D printing technology, rapid prototyping using 3D printing has become increasingly popular in prototype manufacturing.
Many engineers now prefer 3D printing for the initial prototype because it is cost-effective, quick, and capable of producing complex structures in a single piece.
However, the downside of 3D printing is its relatively rough finish, making it unsuitable for products requiring high precision.
The best current 3D printing method is SLA laser rapid prototyping, which offers high precision and relatively smooth surfaces. The printed material is similar to ABS, and the method is particularly favored for graduation projects. It also allows for post-processing like coloring and electroplating.
3. Silicone Mold Replication - Vacuum Casting
Silicone mold replication involves creating a mold using silicone materials and then using this mold to replicate the product.
The process of making the mold is similar to that of fiberglass molds, but with different materials.
First, a master model is created, which is then placed into liquid silicone.
After the silicone cures, the master model is removed, leaving behind a mold. This silicone mold is used to cast liquid materials under vacuum to avoid incomplete filling, which would cause defects in the product.
Silicone mold replication is suitable for small-batch production, particularly when a metal mold has not yet been made or when the product demand is low.
For example, medical devices, which are large in size but produced in limited quantities, often use this method because creating metal molds is costly and time-consuming.
Silicone mold replication can produce materials such as ABS, PC, PP, soft rubber, PMMA, nylon, PVC, and more. However, the downside is that the dimensional accuracy is not very high, with a tolerance range of 0.1-0.2mm due to the soft nature of the mold.
As the prototype industry evolves, manufacturing methods will continue to advance with productivity improvements, and more advanced prototype processing methods will emerge.
Opro-Tech Engineering Ltd can also offer small-batch production services through prototype manufacturing. If you have any prototype needs, feel free to contact us.
WhatsApp: +66 807412390
WeChat : +86 18128665523
Email: xiu@opro-tech.com