Why would you use CNC methods for production?
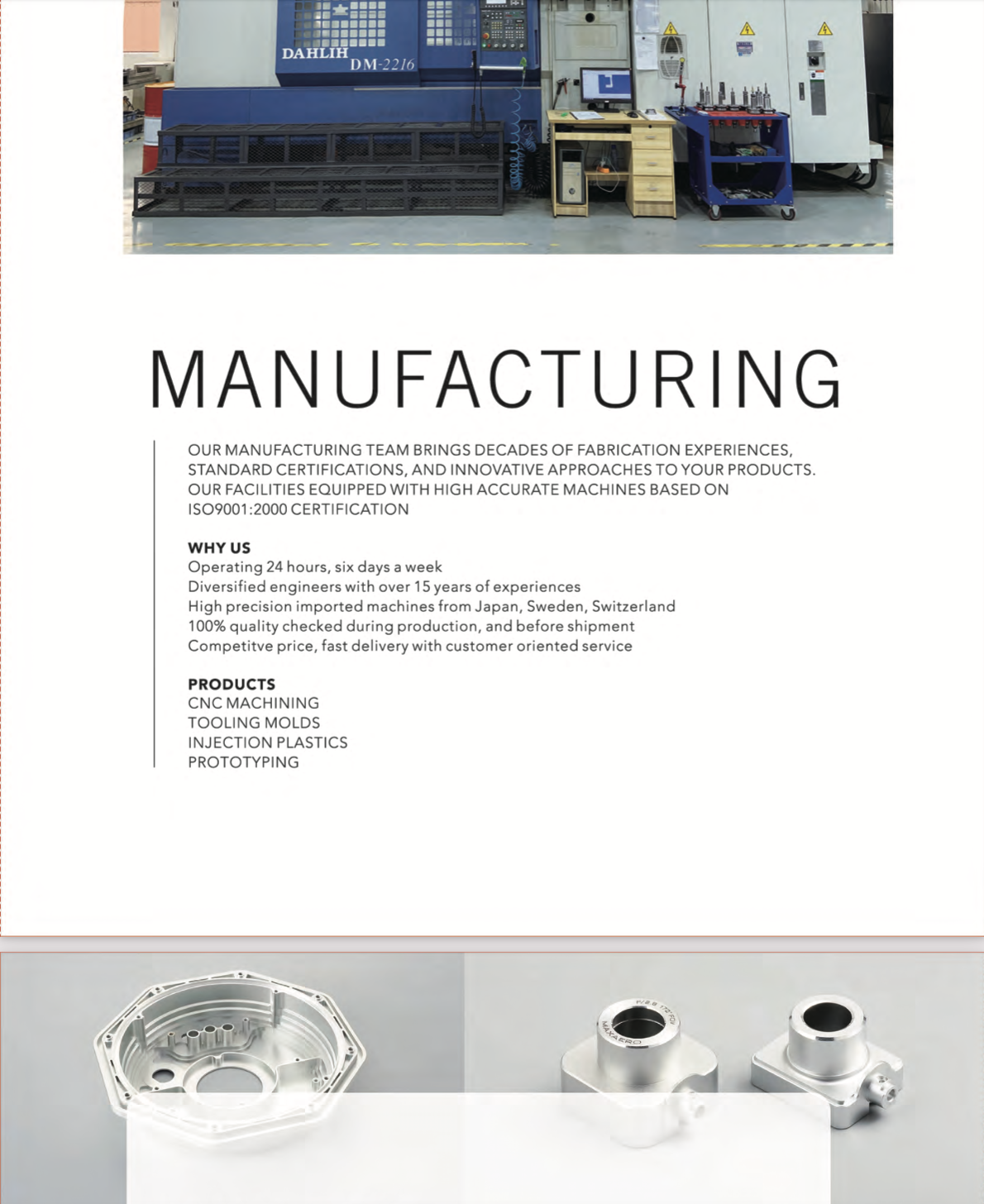
CNC (Computer Numerical Control) methods are employed for production for several compelling reasons:
Precision: CNC machines offer exceptional precision and accuracy, making them ideal for creating intricate and complex parts with tight tolerances.
Repeatability: CNC machines can reproduce the same part or product consistently and with high repeatability, ensuring uniform quality across a production run.
Efficiency: CNC machining is highly efficient, reducing waste and minimizing the need for manual labor. It can produce parts quickly and cost-effectively.
Complex Geometries: CNC methods are capable of producing parts with complex shapes and geometries that would be challenging or impossible to achieve with traditional methods.
Versatility: CNC machines can work with a wide range of materials, from metals and plastics to composites and wood, making them suitable for various industries and applications.
Automation: CNC machines are automated and programmable, reducing the need for constant human intervention and supervision in the production process.
Customization: CNC machining allows for easy customization and quick adjustments to design specifications, making it suitable for both prototyping and mass production.
Reduced Lead Times: CNC methods can significantly reduce lead times in the production process, contributing to faster product development and time-to-market.
Quality Control: CNC machines can be equipped with sensors and quality control measures to ensure the quality of the produced parts.
Cost-Effective: In many cases, CNC machining can be cost-effective, especially for medium to high production volumes, as it minimizes manual labor costs and material waste.
Overall, CNC methods provide a versatile, efficient, and highly precise means of production suitable for a wide range of industries and applications.
We specialize in precision hardware and CNC machining parts for a wide range of materials, including but not limited to tungsten steel, imported materials like SKD11 and SKD61, various stainless steel grades such as SUS303, SUS304, SUS316, SUS316L, as well as A5052, AL6061, AL6063, AL7075, LY12, 65Mn, Cr12, 40CrMo, 45#, Q275, ST12.03, SS2331, SS1994-04, AISI12L14, Y15, bakelite, POM, steel, nylon, teflon, and acrylic, among others.
Additionally, we offer a comprehensive range of surface treatments, including anodizing, chrome plating, nickel plating, zinc plating (black zinc), blackening, electropolishing, passivation, titanium plating, powder coating, and electrophoresis. Our heat treatment capabilities encompass processes such as vacuum quenching, salt bath nitriding, nitriding, carburizing, carbonitriding, high-frequency firing, carbon immersion firing, quenching and tempering, and more.
Contact us at danny@opro-tech.com for more detailed information.