What is an Insert Molding?
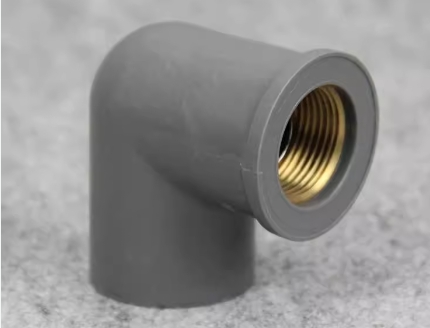
Insert Molding is an injection molding technology that embeds metal or other materials into plastic parts during the injection molding process. This approach allows disparate materials to be integrated together in a single injection molding process, creating composite parts with multiple functions. It is often used to produce parts that require high strength, complex structure or multi-functional requirements, such as electronic equipment, automobile parts, etc.
Insert molding advantages:
Increase product strength: Injection molded parts can be made stronger and stiffer by embedding metal or other strong materials into plastic.
Improved overall performance: Insert molding enables the integration of multiple materials in a single step, thereby improving the overall performance and functionality of the product.
Improved electrical conductivity: If conductive materials are embedded in injection molded parts, the electrical conductivity of the product can be improved, which is suitable for some applications that require the integration of electronic components.
Reduced assembly steps: Insert molding can reduce product assembly steps because some parts are already embedded during the injection molding process, reducing the complexity of subsequent assembly.
Reduce the number of parts: Through insert molding, multiple parts can be integrated into one, reducing the number of parts and simplifying the product structure.
Insert molding disadvantages:
Manufacturing Complexity: The manufacturing process of insert molding is relatively complex and requires careful design and adjustment of the injection mold to ensure that the embedded parts are positioned correctly and maintain good quality.
Cost: Insert molding can be more expensive to manufacture due to the additional materials and complex mold design involved.
Restrictions on material selection: Selecting an insert material suitable for insert molding may be subject to some limitations, including factors such as compatibility with the plastic material and melting temperature.
Possible increase in production cycle: Due to the multiple processes involved, the production cycle of the product may be increased, especially when customized molds are required.
If you are about to start a new project, welcome to contact Opro-tech. Our professional team has extensive knowledge and can assist you with comprehensive cost analysis, mold design evaluation and production efficiency evaluation.
To understand better about insert molding and over molding or 2K molding, here is the video link for better understanding. Published by Star rapid.
https://www.youtube.com/watch?v=kDrdtRFZPrQ&t=82s
And what's more? For your insert molding project, we can do the prototyping first.