Consideration of sub gate in tooling mold design
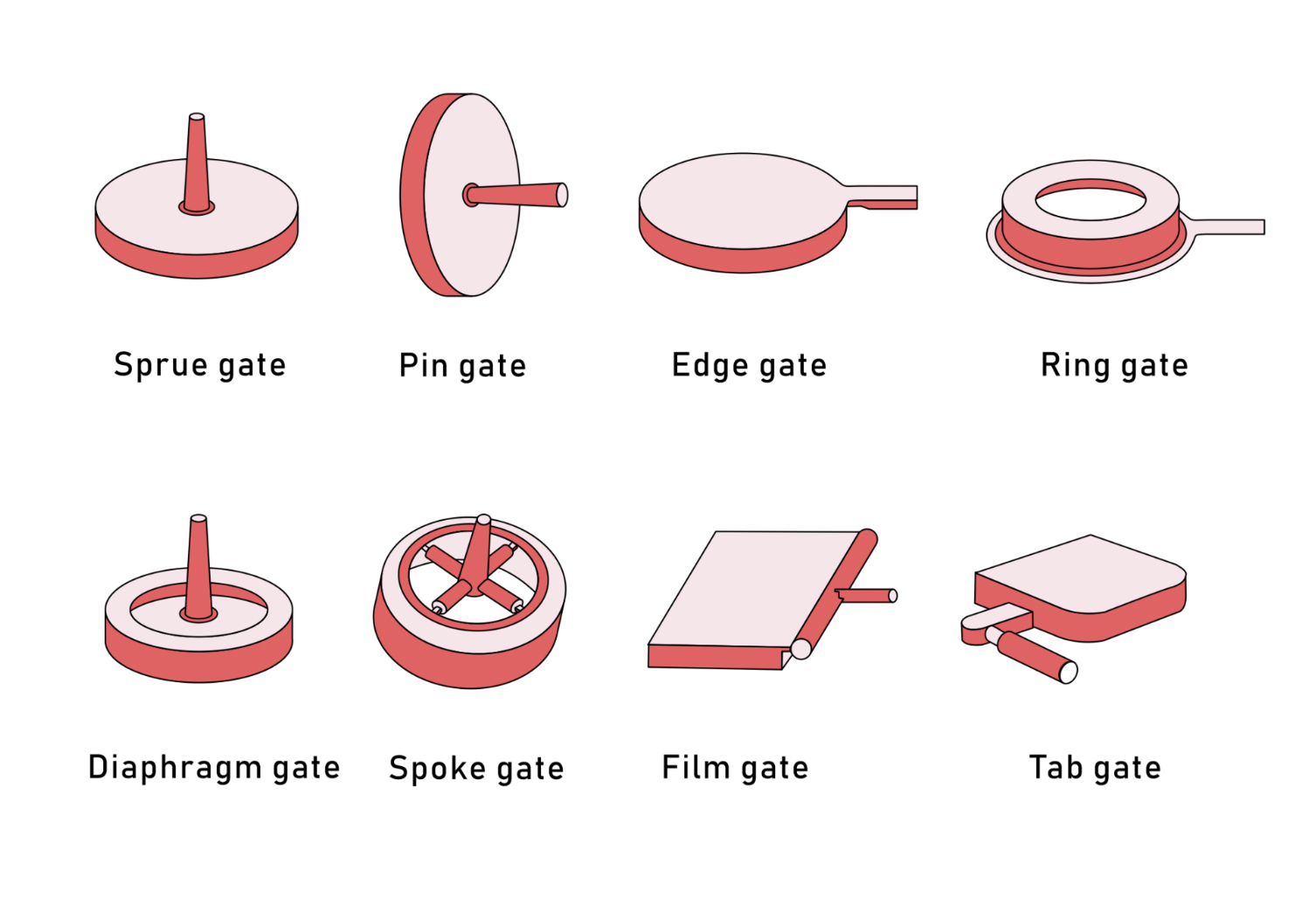
Today, I received a positive comment from Musbbir Design Space regarding my study note on sub gates in tooling mold design. I want to express my gratitude to Musbbir for the thumbs up, and I'm committed to continuously enhancing technical knowledge in the manufacturing field. In response to the question, the following is my study note.
The effectiveness of sub gates can be influenced by the material being used and the specific geometry of the molded part. While sub gates are versatile and suitable for many applications, there are situations where other gate types might be more advantageous. Here are some considerations:
Material Flow Characteristics:
High Viscosity Materials: Sub gates may face challenges with high-viscosity materials that do not flow easily. In such cases, a gate type with better flow characteristics, like a fan gate, might be more effective.
Part Geometry:
Thin-Walled Parts: Sub gates work well for a variety of part geometries, but for extremely thin-walled parts, a gate type that provides more controlled filling, such as a pinpoint gate, might be preferred.
Complex Parts: Parts with intricate designs or those requiring specific flow patterns might benefit from gates that allow for more control over the flow, like edge gates.
Mold Design:
Placement Restrictions: Depending on the mold design and part layout, there might be spatial restrictions that limit the use of sub gates. In such cases, a gate type that offers more flexibility in placement, such as an edge gate, could be chosen.
Cycle Time Considerations:
Cycle Time Sensitivity: In situations where cycle time is critical, gate types that promote faster filling and cooling, such as edge gates, might be favored.
Sub gates are a type of gating system used in injection molding, and their suitability depends on the specific characteristics of the product being manufactured. Here are considerations for when to use sub gates and when they may not be suitable:
Products Suitable for Sub Gates:
Thin-Walled Parts: Sub gates are effective for molding thin-walled parts where a traditional gate might leave visible marks on the surface.
Aesthetic Surfaces: When the aesthetic appearance of the product is crucial, sub gates can be advantageous as they minimize gate vestiges on the visible surfaces.
Cosmetic Parts: Products with cosmetic requirements, such as consumer electronics casings or medical devices, can benefit from sub gates to enhance the overall appearance.
Reduced Warpage: Sub gates can help reduce warpage issues in certain products, especially those prone to distortion during the cooling phase.
Products Not Suitable for Sub Gates:
Thick Parts: For products with thick sections, sub gates may not be as effective. Traditional gates or other gating techniques may be more appropriate to ensure proper filling and reduce the risk of voids.
High Flow Resins: Certain high-flow resins may not be suitable for sub gates as they can cause issues with drooling or stringing.
Large Parts: Sub gates may not be practical for larger parts where the gate size required for proper filling becomes a limitation.
Structural Parts: Products requiring high structural integrity may not be suitable for sub gates, as they may not provide the necessary flow characteristics.
High Viscosity Materials: Materials with high viscosity may pose challenges with sub gates, affecting the flow and filling of the mold.
Thank you for being part of this exciting learning experience, if you have any questions or comments, please leave message below or feel free to reach out to me at danny@opro-tech.com. Your feedback is highly valued.